Admin مدير المنتدى


عدد المساهمات : 18726 التقييم : 34712 تاريخ التسجيل : 01/07/2009 الدولة : مصر العمل : مدير منتدى هندسة الإنتاج والتصميم الميكانيكى
 | موضوع: كتاب Foundry Technology الأربعاء 08 سبتمبر 2021, 12:19 am | |
| 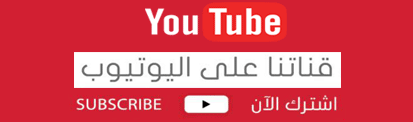
أخواني في الله أحضرت لكم كتاب Foundry Technology Second Edition Peter Beeley BMet, PhD, DMet, CEng, FIM, FIBF Life Fellow and formerly Senior Lecturer in Metallurgy, University of Leeds
 و المحتوى كما يلي :
Contents Preface to the second edition vii Preface to the first edition ix About the author xi Introduction 1 1 Liquid metals and the gating of castings 15 2 Solidification 1 Crystallization and the development of cast structure 51 3 Solidification 2 The feeding of castings 100 4 The moulding material: properties, preparation and testing 178 5 Defects in castings 239 6 Quality assessment and control 319 7 Casting design 362 8 Production Techniques 1 The manufacture of sand castings 443 Part 1. Mould Production 443 Part 2. Melting and Casting 487 Part 3. Finishing Operations 525 9 Production Techniques 2 Shell, investment and die casting processes 547 10 Production Techniques 3 Further casting techniques 622 11 Environmental protection, health and safety 675 Appendix 687 Index 69 Index Abrasive belts, 532 Abrasive cleaning, 526 Abrasive wheels characteristics of, 531 operating speeds of, 529, 531 Accuracy, see Dimensional accuracy Acid demand, 196 Additives to moulding sands, 106, 214, 250 Acurad Process, 605 Aeration of moulding sand, 220, 226 Ageing heat treatment, 539 influence of, in CO2 process, 211 Airlock defect, 254 All-core moulding, 452, 475 Alloys casting, 5 corrosion resistance of, 414 design criteria and data for, 397–420 feeding characteristics of, 102–107 for die casting, 592, 594, 595 fluidity of, 18 foundry properties of, 405 melting losses in, 501–504 melting practice for, 495–501 properties of, sources of design data, 407–420 response to heat treatment, 407 summary of characteristics and applications, 418 weldability of, 406, 417 see also Mechanical properties and under individual properties Aluminium alloys in die casting, 592, 594–597, 602 melting losses in, 501, 502 melting of, 499 welding of, 311 see also Alloys, properties of Aluminosilicates in investments, 570 in mould coatings, 218 Ammonium bifluoride, as reaction inhibitor, 214, 262 Analysis, chemical, 264, 255, 509 Angularity, coefficient of, 202 Anisotropy in castings, 78, 80, 380 Annealing, 539 Antioch process, 587 Anti-piping compounds, 147 AOD Process, 508 Arc cutting, 530 Arc feeding, 145 Arc furnaces, 489, 493 Arc welding, 307 Aspiration, in gating, 28 Atmospheric head, 142 Atmospheric puncture, 142, 274 Austempering, 539 Austempered ductile iron, 411 Automatic fettling, 533 Automatic pouring, 519–522, 609 Automation in investment casting, 569, 577 Backing sand, 231 Baffle core, 38 Bale out furnaces, 493 Ball plug, 38 Banding, in centrifugal castings, 639 Bars feeding distance in, 135 solidification of, 125 Basin, in gating, 28, 43, 45 Bearing properties and alloys, 403, 414 Bench life, of moulding material, 180, 191 Bend test, 332700 Index Bentonite, 203 Bernoulli’s theorem, 27 Betatron, in radiography, 343 ‘Big bang’ nucleation, 76 Bimetal casting techniques, 394 in centrifugal casting, 642 Binders, 198, 202–213 cement, 210 cereals, 205 chemical, 206–213 clays, 202–205 cold setting, 208 content of, 202 ethyl silicate, 568 gas and vapour hardening, 210 heat curing, 207 in investment casting, 568 linseed oil, 206 shell moulding. 550 synthetic resin, 206 thermal breakdown of, 182, 206–213 Blades, gas turbine, 80–82, 583 Blast cleaning, 526 Blind heads, 141 Block mould techniques, 452 Block moulds, in investment casting, 568, 587 Blowholes, 254, 258 Blowing in sand mould compaction, 461 of cores, 477 of shell moulds, 556 Blow-squeeze mould compaction, 461 Boil, 500 role of in degassing, 257–266 Bonding materials, see Binders Boric acid, as mould reaction inhibitor, 214, 262 Bottom gating, 31 Boxes, moulding, 293, 448 Brackets, 432 Brazing, 312 Breakdown characteristics of sands and binders, 182, 206–213 Breaker cores, 275 Brinell hardness test, 331 British Standards for castings, 409, 687 for inspection and testing, 692 for sieves, 197 Bubble nucleation, 259 Bulk density, of moulding material, 187, 200, 455 Burning-on, as rectification technique, 312 Burst feeding, 104 Bush, runner, 28, 43, 45 C process, see Shell moulding CADCAM, 363 Carbon boil, 257, 266, 500 Carbon dioxide process, 210–212, 485 Carriers, core, 476, 485 Cast alloys, see Alloys Cast irons, compression strength of, 412, 438 damping capacity of, 84 feeding of, 162 gating systems for, 47 graphite in, 84, 88, 89 inoculation of, 88, 91 melting losses in, 502, 504 section sensitivity of properties, 328, 381 solidification of, 88–91, 105–107 weldability of, 310 see also Alloys, properties of, etc. Cast steels, gating of, 47 melting of, 500 weldability of, 308, 310 see also Alloys, properties of, etc. Cast structure, see Structure Cast-welded construction, 367, 386–392 Castable sand process, 210 Castability of liquid metals, 15 Casting defects, see Defects Casting design, see Design Casting processes, 385, 444–670 Casting shape, influence of in feeding, 121, 129–133 see also Shape features in casting Casting temperature, see Pouring temperature Casting yield, 112, 368Index 701 Casting, characteristics of economic, 368 dimensional, 371 metallurgical, 379 Castings comparison with wrought products, 380–383 design of, 362–440 heat treatment of, 537–540 structure and properties of, 70–96 379–385 Caulking, 313 Cavities gas, 258 influence on stress distribution, 301–304 shrinkage, 271–277 Cellular structure, 62 in eutectics, 68 Cement bonded sands, 210 Cement moulding process, 210, 453 Centreline shrinkage, 135, 272 Centrifugal casting, 622–645, 667 De Lavaud process of, 629 fundamentals of, 623–625 inclusions, separation of, 627 Moore process of, 630 of investment moulds, 576 of rolls, 642 of short pots, 628, 632 of tubes, 629–632 process variables in, 636 production techniques in, 628–639 rotational speed in, 623, 636 semicentrifugal and pressure casting, 635 solidification and feeding in, 626 Centrifugal castings, 622–645 applications of, 642–645 banding in, 639 bimetal, 642 comparison with other products, 641 defects in, 637 structure and properties of, 639–642 Ceramic cores, 572 Ceramic mould process, 587 Ceramic shell technique, 567, 569, 570 Cereal binders, 205 as aid to breakdown, 205 Chamotte, 199, 215 Channel furnaces, 493 Channel segregation, 300 Chaplets, 48, 423, 476, 487 Charge in melting, 263 shaped, 503 Chemical bonding, 206 Chemical cleaning, 528 Chemical etching, 335 Chill tests, for melt quality, 510 Chill zone, 80 Chilling, influence on structure, 593 Chilling power of mould materials, 159, 216 Chills effect in feeding, 90, 118, 135, 139, 156–160 influence on mode of freezing, 104 influence on structure, 90 non-metallic, 159 porosity due to, 160 Chipping, 531 Chlorine, as scavenging gas, 265 Chromite, 216 Chworinov Rule, 109 CLA index of surface roughness, 326 CL Processes, 655 Clays, 202–205 tests on, 198 Cleaning blast, 526 chemical, 528 ‘Clinks’, 288 Closed system pouring, 522 Closing, 486 of shell moulds, 554 Coal dust in moulding sands, 107, 214 Coatings core, 219, 486 die, 602 mould, see Mould coatings Cobalt 60, in radiography, 342 COD test, 399 Cold box process, 483 Cold chamber die casting machines, 597 Cold cracking, 288, of welds, 309 Cold crucible melting, 665702 Index Cold hearth refining, 666 Cold laps and shuts, 30, 241 Cold set process, 483 binders for, 208 Cold shell moulding, 558 Collapsibility, of moulding material, 179, 182, 195, 206 Colony structure, 52, 67 Columnar structure, 55, 71, 78–80 Compactability of sand, 186 Compaction of cores, 477 of moulds, 454–466 Compo, 215 Composition, metal influence in hot tearing, 280 influence on structure, 70 inspection aspects of, 327 Compression strength of grey cast iron, 412, 438 of moulding materials, test for, 185 Computer modelling, 164 Connor runner, 37 Constitutional undercooling, 59 Consumable electrode vacuum melting, 665 Continuity, equation of, 27 Contirun system, 45 Contour squeeze moulding, 457 Contraction allowances, 447 anomalous, 293, 371 defects, 275–289 liquid, 48 solid, 277 solidification, 100 Contrast, radiographic, 340 Control charts, quality and process, 351–359 Convection, effects in solidification, 76, 300 Cooling fins, 122 Cooling modulus, 109, 123 Cooling rate, see Solidification rate Copper alloys gating systems for, 47 melting losses in, 501, 502 melting of, 499 welding of, 307, 311 see also Alloys, properties of, etc. Core assembly moulding, 452, 475 Core coatings, 486 Coreblowing, 477 Coreboxes, 476 Cored holes, minimum diameters of, 424 Coremaking processes, 474–486 carbon dioxide, 484, binder, 210 cold box, 483 cold set, 483, binders, 208 fluid or castable sand, 210 hot box 482, binders, 207 machines, 477 warm box, 483 summary of process characteristics, 424 Coreprints, 48, 475 Cores, 474–486 baking of, 484 carriers, 476, 485 ceramic, 572 collapsibility, need for, 182 compaction of, 477 design aspects of, 423 extrusion of, 477 forces acting on, 47 functions of, 450, 474 hardening of, 480, 484, 485 in gravity die casting, 592 in investment casting, 572 influence on freezing rate, 109, 123 jointing of, 486 soluble, 593, 663 special types of, 662 shell, 482, 554, 556 support of, 48 surface coatings for, 219, 486 venting of, 479 Coresand mixtures, 214 requirements of, 181 Coreshooting, 477 Corestoves, 484–485 Coring and cored structures, 62, 295 Corrosion products, contamination from, 260Index 703 Corrosion resistance of alloys, 404, 414, of welds, 311, 417 Corrugation, in design, 287, 437 COSHH regulations, 682 Costs influence of yield on, 111 in precision casting processes, 615–619 of alloys, 409 of casting, 368, 439 of inspection, 323 of patterns and tooling, 7, 368–369 of production, 368–369, 615–619 related to accuracy, 548 Cosworth process, 654 Cothias process, 648 Counter gravity casting, 653–657 Counter pressure casting technique, 606, 654 Cover core, 475 Cracking, 287 in welds, 309 Creep, 402 Cristobalite, 247, 571 Critical defect size, 303, 399 Croning process, see Shell Moulding Cross jointing, 293 Crucible furnaces, 489, 491 Crush, mould, 246 Crystal multiplication, fragmentation, 75, 95 Crystallisation, 52–76 growth, 54 nucleation, 52 Cumulative grading plots, 200 Cupola, 491 Curing, of resin binders, 208, 481–484, 552 Cutting, 529–531 D process, 556 DS casting, 80, 583 Davis wheel, 644 Defects in castings, 239–314 classification of, 240 contraction, 275–290 dimensional, 292–293 gas, 254–271 inclusions and sand, 241–254 internal, tests for, 338–350 of shape, 240 origins of, 239 rectification of, 305–314 segregation, 294–300 shrinkage, 271–277 significance of, 301–305 surface, tests for, 334–338 Defects in centrifugal castings, 637 Defects in die castings, 611 Defects in investment castings, 580 Defects in shell moulded castings, 560 De Lavaud process, 629 Definition, radiographic, 341 Deformation of moulding material, 179, 188 in relation to hot tearing, 285–287 Degassing of molten metal, 265–271 scavenging gas technique of, 269 spontaneous, 265 vacuum, 267–270 Dendrite fragmentation, 76 Dendritic growth and structure, 60–62, 71–74, 86 Dendritic segregation, 295 Denseners, see Chills Density as indication of soundness, 104, 274, 511 bulk, of sand, 455 radiographic, 338, 340 Deoxidation of liquid metals, 266, 499, 504 Design, 362–440 aims in, 362 characteristics of castings, 2–8, 368–385 dimensional, 371 economic, 368 metallurgical, 7, 379 cost aspects of, 411 data, sources of, 407 engineering aspects of casting shape, 437 for casting production, 362, 420 casting stage, 424 moulding stage, 421704 Index Design (continued) freedom of, 2, 370 influence in hot tearing, 284 initial considerations in, 366–385 machining factors in, 434 modifications for feeding, 154 process and alloy selection in, 385–420 property criteria in, 397–407 shape features in, 420–440 surface treatments, 395 tooling costs in, 7, 368 see also Alloys, properties of etc. see also Mechanical properties Destructive tests on castings, 333 Dewaxing techniques, 574 Dextrin, 205 Die casting, see Gravity die casting see Low pressure die casting see Pressure die casting Die castings applications of, 611–615 characteristics of, 609 design of, 610 limitations of, 611 dimensional accuracy and tolerances of, 610 Dies for gravity die casting, 592 for investment casting, 564 for pressure die casting, 600 Dilation, mould, 105 Dimensional accuracy and tolerances, 371–378, 548 economic aspects of, 548 of investment castings, 579 of pressure die castings, 610 of shell moulded castings, 559 Dimensional errors, 292, 371 Dip and stucco investment, 567 Dip forming, 645 Directional solidification, 101, 104 controlled, 80 design for, 428 Directionality, in castings, 78–82, 380 in wrought materials, 380, 383 Disamatic moulding system, 461, 463 Discharge coefficient, 43 Distortion, casting, 287, 289 Distribution coefficient, 294 Downrunner, 26 dimensions of, 28 Downsand frame, 458 ‘Draw’, 275 Dressing of castings, 531–535 Dressings, see Mould coatings Driers, core, 476, 485 Dross traps, 37 Dry strength, of sand, 179, 184 Drying of cores, 484 of investment casting moulds, 574 of moulds, 181, 472–474 Drysand practice, characteristics of, 181 Ductility, 402 Durability, of moulding material, 180 Dust, 535 Dye penetrant testing, 334 Dypur direct pour unit, 43 Electric arc feeding, 145 Electric melting furnaces, 489–495 Electromagnetic pumping, 522 Electromagnetic stirring, 95 Electromagnetic testing, 350 Electron beam melting, 667 Electroslag casting, 647 Electroslag feeding, 145 Electrostatic coatings, 220 Elongation, 402 Embrittlement by gases, 254, 271 by segregated impurities, 304 in welding, 309 Endogenous inclusions, 242 Endurance ratio, 399 Entropy of fusion, role in crystallisation, 67 Environment Agency, 677 Environmental impact, 678 Environmental protection, 675–685 Equiaxed structure, 64, 65, 73–76, 79–80 Erosion scabs, 246Index 705 Etching, 335 Ethyl silicate binder, 568, 588 Eutectics anomalous, 66 cellular structure in, 67 lamellar, 65 modification of, 77, 92 morphology of, 65, 84, 88, 91 refinement of, 84–90 solidification of, 52, 64–69, 91–95 Evaporative pattern casting, 659 Exogenous inclusions, 243 Exothermic feeding, 127, 147–151 Exothermic padding, 161 Expansion defects, 246–251 additives to counter, 250 influence of process variables on, 250–251 Expansion stage in freezing, 105 Expansion, thermal, of moulding material, 216, 247 Explosion: role in metal penetration, 252 Exposure, radiographic, 339 Extended launder furnace, 523 Extraction systems, dust and fume, 535 Extrusion casting, 649 Fabrication, 1, 367, 370 Facing-backing sand practice, 230 Falling crystallites, 76 Fatigue limit, 399, 412 Feeder heads, 118–152 aids to efficiency of, 145 atmospheric, 142 blind, 141 design and location of, 118–144 exothermic, 127, 147 insulation of, 146 knock-off, 154, 528 junction of, with castings, 152 positioning of, 133–140 purpose of, 100 removal of, 529–531 shape of, 119 shared, 140 size of, 120–133 summary of design principles for, 140 whirlgate, 144 Feeding of castings, 100–173 burst, 104 casting shape, effect on, 107, 129 casting temperature, influence on, 117 characteristics of alloys, 102–107 compounds, 146 cooling modulus and, 123 design for, 154, 426–430 distance, in parallel sections, 135–139 effect of chills on, 118, 156–160 electric arc, 145 exothermic, 127, 147–151 electroslag, 145 gating techniques for, 113–117 intergranular and interdendritic, 100, 105 mass, 79, 100 methods for, 110–164 orientation for, 113 padding for, 154 pouring rate and temperature, influence of, 117 pressure for, 139, 151 range, 119, 135 restricted neck, 109, 152 temperature gradients in, 101, 113–118 Feeding of centrifugal castings, 626 Fettling, 525 characteristics of, 537 chipping, 531 grinding, 531 hot, 533 Filamentary shrinkage, 274 Fillet radii, 431, 437 Filling compounds, 314 Films, surface, on liquid metals, 20, 22, 260 Filtration in gating systems, 39 of molten metal, 245 Fineness, of moulding material, 180706 Index Finger gates, 33 Finishing operations, 525–542 cutting, 529–531 dust in, 535 dressing, 531–533 for pressure die castings, 609 initial cleaning, 525–528 see also Fettling Flame cutting, 530 Flash gate, 35 Flasks, see Moulding boxes Flaw detection, see Non-destructive testing Flaws, see Defects Floor moulding, 450 Flow of liquid metals, 23–47 design for, 426 from ladles, 513–517 in moulds, 23–48 in pressure die casting, 603 influence of mould conditions on, 23 laminar, 27 summary of factors affecting, 25 turbulent, 27 Flowability of sand, 178, 186, 200 Fluid life, 16 Fluid sand process, 210 Fluidity, 15–23 effect of surface tension and films on, 20 measurement of, 16 variables influencing, 17 Fluoroscopy, see X-ray fluoroscopy Flushing treatments, gas, 265 Flux injection process, 507 Fluxes brazing and soldering, 313 inspissated, 499 melting, 264, 497–500, 664 welding, 307 Forgings, compared with castings, 1, 382–385 Forming of metals, 1, 366 Foundry industry, 8–10 Foundry properties of alloys, 405 Fracture tests for melt quality, 510 Fracture toughness, 398 Freckling; freckle segregation, 300 Freezing range of alloys influence in feeding, 102–105 influence on fluidity, 19 Freezing time criterion, in feeding, 116 Freezing, see Solidification Friability of mould surface, 244 Friction cutting, 529 Full mould casting process, 139, 660 Fumeless refining, 500 Furan resin binders, 209 Furnace charge and additions, 496 gas contamination from, 263 Furnaces, melting, see Melting furnaces Gamma radiography, 341 Gas absorption of, in melting, 259 estimation of, in liquid metals, 509 evolution from moulding materials, 192 solution, origins of, 255 scavenging, 265 Gas defects, 254–271 types of, 254, 258 formed by entrapment, 254–255 formed by precipitation, 254–258 preventive measures, 263–271 Gas-metal equilibria, 255 Gas welding, 307 Gassing time, influence of in CO2 process, 211 Gating of castings, 25–47 for feeding, 113–117 metal factors in, 46 moulding factors in, 45 objectives in, 25 relevance to hot tearing, 284 Gating ratio, 29 Gating systems bottom, 31 essentials of, 26 filtration in, 39 finger, 33 horn, 31 in pressure die casting, 603 knife, 35Index 707 pencil, 30 removal of, 528 side, 31 step, 35, 116 top, 30 traps in, 37 Gelling index, of clay, 198 Gooseneck die casting machine, 596 Gouging for welding, 307 Grading, mechanical, of sand, 197, 200 Grain shape of moulding material, 200 Grain size of moulding material, 199 Grain structure in cast alloys, 52, 59, 77 Grain refinement, 77, 84–96, 505 Grain shape and orientation, 78, 380 Grain size, 77, 82, 380 Graphite in cast iron, 65, 88, 91–93 Graphite moulds, 653, 667 Gravity die casting, 592 Gravity segregation, 299 of nuclei, 90 Gravity transport of crystals, 76 Green strength of moulding material, 178 Greensand practice, characteristics of, 180 Griffin Process, 653 Grinding, 531–533 Growth, crystal, 54–69 cellular, 62, 67 columnar, 55 dendritic, 60 in alloys, 56 in pure metals, 54 planar, 55 Hand ramming, 455 Hardenability, 407 Hardness in design, 403, 414 tests, for castings, 331 tests, for moulds, 188, 191 Heads, see Feeder heads Health and Safety, 682–685 Hearth furnaces, 489, 491 Heat affected zone, in welding, 309 Heat diffusivity, of moulding material, 24 Heat resisting alloys, 413, 415 Heat treatment, 537–540 furnace loading aspects of, 540 homogenisation, 300, 358 processes for castings, 537–540 response of alloys, 407 section thickness effects, 540 time, 540 Heterogeneous nucleation, 53, 90–93 Heuvers circle, 152, 154 Hexachloroethane as degassing compound, 265 as mould coating constituent, 24 High pressure moulding, 106, 457 High speed melting, 503 High temperature properties of alloys, 278, 280–283, 402, 413 of moulding materials, 193 Historical development of founding, 8 Holding furnaces, 489, 492, 493 Holes, cored, dimensions of, 423–426 Homogeneous nucleation, 53 Homogenisation, 300, 358 Horn gates, 31 Hot box process, 482 binders for, 207 Hot chamber die casting machines, 596 Hot deformation, of moulding materials, 195 Hot distortion test, 193 Hot fettling, 533 Hot isostatic pressing, 314, 540–542 Hot spots, 108, 275 Hot strength, of moulding material, 179, 194 Hot tearing, 278, 279–287 design and production factors in, 283–287 design for prevention of, 284, 430–433 in centrifugal castings, 638 influence of alloy composition on, 280 influence of mould on, 285 influence of segregation on, 282 Hydraulic cleaning, 528 Hydraulic soundness, 79, 84, 301, 304708 Index Hydrogen in liquid metals, 256–271 in welding, 310 melt quality tests for, 509 see also Gas see also Gas defects see also Gas-metal equilibria Illite, 203 Immersion pyrometry, 512 Impact moulding, 464 Impact penetration test, 192 Impact tests, 332 Impregnation, of porous castings, 105, 313 In-situ composites, 652 Inclusions, see Non-metallic inclusions Independent nucleation, 63 Indigenous inclusions, 242 Indirect padding, 154 Indirect squeeze casting, 650 Induction degassing, 268 Induction melting furnaces, 493 vacuum, 665 Induction skull melting, 665 Ingates, 26 Inhibitors, of metal-mould reaction, 262 Injection pressure, in die casting, 596, 597, 603, 605 In-line moulding systems, 467 Inoculation by additives to mould coatings, 93, in cast iron, 85, 91, 505, 507 Inserts in castings, 393, 663 in die castings, 611 Inspection of castings, 322 composition and mechanical properties, 326 costs of, 323 destructive tests, 333 dimensional, 325 functions and aims of, 322 material and product testing, 324–351 non-destructive testing, 333–350 organisation of, 319–322 Inspissated fluxes, 499 Insulation differential, of mould cavity, 161 of feeder heads, 146 Integrated casting systems, 670 Integrated pollution control, 677 Intensive sand mixers, 221 Interdendritic feeding, 100, 105 Intergranular corrosion, 311, 404, 596 Intergranular feeding, 100 Intergranular segregation, 295 Internal chills, 156 Internal hot tears, 279 Intersections design of, 429–431 solidification of, 108 use of chills at, 157 Inverse modelling, 169 Inverse segregation, 299 Investment casting, 563–591 automation in, 569, 577 block moulds for, 570 cores in, 572 dies for, 564 drying and firing of moulds in, 574 investment, 567–571 master patterns for, 565 melting and casting in, 575 pattern production, 565 pattern elimination, 574 permanent pattern processes, 585–591 shaping of cavities in, 571 Shaw process, 587 shell moulds for, 567, 569 Unicast process, 590 Investment castings, 567 applications of, 580–584 characteristics of, 578–580 comparative costs of, 583, 617–619 defects in, 580 dimensional accuracy of, 579 quality of, 577 Isotropy of castings, 8, 78, 380–381 Jet degassing, 266 Joining, see Fabrication Joint line, see Parting line Jointing of cores, 486Index 709 Jolt-squeeze moulding machines, 456 Jolting, in machine moulding, 457 Jominy test, 407 Kaolinite, 203 Keel blocks, 327 Kinematic viscosity, 16 influence on flow of metal in moulds, 27 Knife gate, 35 Knock-off heads, 528 Knockout interval, 228, 522 Knockout temperature, 522 L sections, design of, 429, 431 Ladle degassing, 268–270, 504 Ladle furnaces, 508, 509 Ladles, 513–519 flow rate from, 514 insulation of, 517 porous plug, 508 preheating of, 517 segment, 516 Lamellar eutectics, 65 Laminar flow, 27 Laps, 30, 240 in centrifugal castings, 638 Laser treatment, 395 Latent heat of fusion, 52, 56 Launder, extended, 523 Layer manufacturing, 363 Layer porosity, 273 Levitation melting, 668 Lift off coil furnace, 494 Lift out crucible furnace, 493 Lifters, 470 Light alloys see Aluminium alloys see Magnesium alloys Linear accelerator, in radiography, 343 Linseed oil, 206 Liquid forgings, stampings, 649 Liquid limit, of clays, 198 Liquid metals, 15–48 castability of, 15 contraction of, 48 degassing of, 265–271 flow of, in moulds, 23–48 fluidity of, 15 oxidation of, 266, 497 pyrometry, 512 solubility of gases in, 255 viscosity of, 15 Loam moulding mixtures, 217 principle, 454 Local air pollution control, 677 Locating systems for moulds, 448, 453 for shells, 554 Locking force of die casting machines, 598 Loose pieces in moulding, 450, 451 expendable, 450 Loss coefficients, in metal flow, 28 Losses melting, 111, 264, 501–504 fettling, 111 Lost crucible melting, 503 Lost foam process, 659 Lost wax process, see Investment casting Low pressure casting, 117 of investment moulds, 575 Low pressure die casting, 594 Low pressure sand casting, 654 Lustrous carbon defect, 245 McCannacore process, 662 Machinability of alloys, 406, 416 Machine compaction of moulds, 456–466 Machine cutting, 529 Machine moulding, 456–467 compaction in, 456–466 high pressure, 457 plant, 466 Machining allowances, 376, 434–437 in pressure die casting, 610 as method of shaping, 1, 371 factors in casting design, 434 for head removal, 529 Macrosegregation, 297 Macrostructure of castings, 70–96710 Index Magnesium alloys casting technology of, 664 melting losses in, 502 in die casting, 597, 611 melting of, 499 welding of, 311 see also Alloys, properties of, etc. Magnesium in cast iron, 91, 261, 505–507 Magnetic flaw detection, 335 Magnetic separators, 227 Magnets, columnar structure in, 80 Mains frequency induction furnace, 494 Malleablising, 539 Mansfield sand, 199 Maraging steel, 411 Mass effect in heat treatment, 381, 407, 538 Mass feeding, 79, 100 Master patterns, for investment casting, 565 Matchplates, 452 Mechanical grading, of moulding materials, 195, 197, 199 Mechanical properties, 397–404, 411–414 criteria in design, 397–404 directionality of, 78–82, 380 ductility, 402 endurance ratio, 399 fatigue limit, 399, 412 fracture toughness, 398 hardness, 403, 414 high temperature, 402, 403 influence of defects on, 301–304 influence of section thickness on, 328–330, 381 influence of structure on, 76–96, 380 notched bar impact, 398 scatter of, 381 stages in cooling, 278, 280–283, 328, 330, 381 strength-weight ratio, 413 tensile strength, 397, 401 testing for, 326–333 yield or proof stress, 397, 401 Young’s modulus, 397, 407 Mechanical testing, 326–333 Mechanical working, 1 Medium frequency coreless induction furnace, 494 Melt quality tests, 264, 509–511 Melt sequence, 511 Melt spinning, 647 Melt treatments, 504 Melting, 487–525 charges, 496 developments in, 503 high speed, 503 losses, 111, 264, 501–504 practice, for alloys, 495–501 precautions in, 263 Melting furnaces, 488–495, 503 classification of, 490 design of, 489 efficiencies of, 491–495 extended launder, 522 instrumentation of, 495 self tapping, 503 shaft or tower, 492 Merrick furnace, 575 Metal are welding, 307 Metal cost, 368 Metal flow, see Flow of liquid metals Metal matrix composites, 651 Metal melting, see Melting Metal-mould reaction, 252, 260, 271 inhibitors, 262 Metal penetration, 252 Metals, shaping of, 1, 366–371 Methods, casting, see Feeding of castings Microporosity, effect on properties, 83, 304 Microsegregation, 295 influence in hot tearing, 282 Microshrinkage, 273 Microstructure of castings, 70–96 Mismatch, 293 Misrun castings, 240 Mixers, sand 220–226 intensive, 221 trough, 224 Modelling, see Computer modelling see Process modelling see Simulation see Solidification modellingIndex 711 Modification, of eutectics, 85, 93 Modulus, cooling, 109, 123 Moisture in moulding sands, 202–205 testing, 195 Molochite, 218, 570 Moore process of centrifugal casting, 630 Montmorillonite, 203 Mould closing, 486 coatings, 218–220 as media for nucleants, 93 drying of, 219, 472 influence on metal flow, 23 compaction, 454 crush, 246 dilation, 105 distortion, 293 drying, 181, 472–474 erosion, 246 factors in metal flow, 23 forces acting on, 47 gases, 254 hardening, 181, 472–474 hardness, 188, 191 influence on hot tearing, 285 metal reaction, 252, 260, 271 location, 448, 453, 554 parting, 421 production, 441–487 reinforcement, 467, 470 restraint, 285 reversal casting, 116 temperature, in centrifugal casting, 636 venting, 255, 470 weighting of, 48, 487 Mouldable exothermics, 148, 161 Moulding, 443–472 boxes, 293, 448, 456 closing, 486 core assembly and block moulding, 452 cores, 423, 474–486 design limitations in, 423 direct mould cavity generation, 453 equipment, 444 factors in design, 421 floor, 450 hand, 455 high pressure, 457 loam, 217 machines, 456–467 shell, 555–558 patterns in, 444, 449 practice, 449 processes, summary of, 487 sandslinger, 465 strickle, 454 Moulding material, 178–236 additives to, 106, 214, 250 aeration of, 220–222 bonding materials in, 202–213 cement sand, 210 circulation, in systems, 226 functional requirements of, 178–180 loam, 217 mixing of, 220 mixtures, 214 non-siliceous refractory, 216 preparation of, 220 reclamation of, 231 reconditioning of, 226–231 sands, 198–202 natural, 198 synthetic, 198 systems, 226 testing of, see Sand testing Nails, 251, 470 Naturally bonded sands, 198 Neck, restricted, 109, 152 Nickel alloys melting of, 499 welding of, 311 see also Alloys, properties of, etc. Nitrogen as grain refiner, 91 as impurity, 255–271 as scavenging gas, 265 atmosphere, for pouring, 522 in liquid metals, 255 see also Gas see also Gas defects see also Gas-metal equilibria Nodes, cast, 386–389 Nodularizing treatments, 505712 Index Noise at work, 684 Non-destructive testing, 333–350 chemical etching, 335 electromagnetic methods, 350 magnetic flaw detection, 335 penetrant methods, 334 proof loading and pressure testing, 350 radiography, 338–347 ultrasonic testing, 347–350 Non-metallic inclusions, 241–245 centrifugal separation of, 627 filtration for, 39, 245 gravity separation of, 242 indigenous, 242 exogenous, 243 Normal segregation, 297 Normalising, 539 Notch effects, 302, 398, 401, 427 Notch sensitivity, 383, 398 Notched bar impact properties, 398 tests for, 332 Nozzles, ladle, 514 Nucleation, 52 ‘big bang’, 76 dynamic, 95 heterogeneous, 53, 90–93 homogeneous, 53 influence of refining techniques on, 84–96 independent, 63 mould coatings to promote, 93 shower, 95 Nucleus, critical size of, 53 Oddside, in moulding, 451 Oil and chalk testing, 335 Olivine, 216 Optical pyrometers, 513 Organic binders, 202, 206–213 Orientation of mould cavity for casting, 113, 420 preferred, 54, 60, 78, 80 Osprey process, 648 Ostwald ripening, 61 Overgassing, in CO2 process, 211 Oxidation of liquid metals, 266, 497 Oxide film defect, 244 Oxyacetylene cutting, 530 Oxyacetylene welding, 307 Oxygen injection, 266 reactions with, in melting, 497 Oxypropane welding, 307 Padding, 154 exothermic, 161 indirect, 154 Paints, see Mould coatings Partial mould reversal casting, 116 Parting line, 449–452 design aspects, 42 Partition coefficient, 294 Pasty mode of solidification, 102 Patches, 313 Pattern draw, 449, 450, 471 machines, 455 Pattern elimination, in investment casting, 574 Pattern production, expendable, for investment casting, 565 Patterns, 444–448, 449–454 aspects of in casting inspection, 325 colour coding of, 447 contraction allowances for, 447 cost of, 5, 368 design aspects of, 421 expendable, in investment casting, 565 expendable, in full mould casting, 659 loose, 449 mounted, 451 split, 451 Pencil gates, 30 Penetrameters, radiographic, 346 Penetration, metal, 252 Peritectic reactions, 67 Peritectic hypothesis of grain refinement, 91 Permanent mould casting, 592 Permeability, 180, 188 pH value of investments, 568 of sands, 196Index 713 Phenol formaldehyde binders, 206 Physical properties of alloys, 409 Pickling, 335 Pinholing, 254, 258, 261, 262, 267 Pins, moulding box, 448 Pipe, 104, 106, 273 Pipes, casting of, 629–632 Pitch, as sand additive, 107 Plane front solidification, 54 Plasma cutting, 530 Plasma melting, 492, 667 Plaster investments, 586 Plaster moulding, 586 Plasticity, of clays, 156 Plates, feeding distance in, 135 Plates, solidification of, 125 Plugs, 313 Pneumatic scrubbing of moulding material, 233 Pneumatic testing of castings, 350 Pneumonoconiosis, 525 Pollution control, 676–680 Pore-free die casting, 606 Pore nucleation, 104, 259 Porosity from chills, 160 gas, 254–263 influence on properties, 304 reaction, 257–263 shrinkage, 104, 273 steam, 258 Porous plug ladle, 270, 509 Portland cement, as binder, 210 Postheating of welds, 307–310 Pots, centrifugally cast, 632 Pouring, 511–522 automatic, 519–522 basin, 28, 43, 45 bush, 28, 43, 45 closed system, 522 equipment and techniques, 513–522 in centrifugal castings, 637 ladles, 513 rate for feeding, 117 from ladles, 514 influence in hot tearing, 285 in centrifugal casting, 637 temperature, 512–513 control of, 512 for feeding, 117 in centrifugal casting, 627 influence in hot tearing, 284 influence on structure, 76 measurement of, 512–513 Powder cutting, 530 Powder dispensers, 500, 507, 530 Powder metallurgy, 2 Powder washing, 533 Power load management, 495 Precipitation hardening stainless steel, 411, 582 Precision casting processes characteristics of, see under individual processes economic comparison of, 615–619 Precision in casting, 547, 615 Preferred orientation, 54, 60, 78, 80 Preheating for welding, 307–310 of furnace charges, 263 Premium quality castings, 79, 90, 156, 330, 382 Pressure casting of investment moulds, 575 Pressure die casting, 595–615 alloys, 595 cold chamber machines, 597 dies for, 600 finishing of, 609 flow of metal in, 603 gating systems in, 603 hot chamber machines, 596 injection conditions in, 603–607 machines, 596–600 vacuum, 605 Pressure die castings, see Die castings Pressure testing, 104, 350 Pressure tightness, 37, 79, 84, 304 Process capability, 352 Process control, 12, 351–359 Process modelling, 164–173 Processes, 385 casting, 443–679 moulding, summary of, 487 see also individual processes714 Index Production techniques, see Processes Proof loading, 350 Proof stress, 397 Properties of casting alloys, see Alloys, properties of, and under individual properties Property criteria in design, 397–404 Prototyping, 363 ‘Pulls’, see Hot tears Pumping, of liquid metal, 522 Punctures, surface, 274 Pure metals, solidification of, 54 Pyrometry immersion, 512–513 optical and radiation, 513 Quality definition and assessment of, 322 standards for, 321, 323 systems and management, 319 see also Inspection of castings see also Non-destructive testing and under individual tests Quality and process control applications in founding, 358 charts, 352 organization of, 319 Quartz, 199 expansion characteristics of, 217, 247, 571 Quenching, 539 stresses in, 291 Quickly replaceable loop (QLR) system for channel furnace, 494 for ladle heating, 518 Radiation pyrometers, 513 Radii, fillet, at intersections, 431, 437 Radiographs, characteristics of, 340, 341 Radiography, 338–347 equipment for, 343 exposure in, 339 gamma, 341 sensitivity of, 345 Radioisotopes, 342 Ramming of cores, 477 of moulds, 454–467 of test specimens, 183 Ramming density, 454 influence on scabbing, 250 Randupson process, 210, 453 Rapid mixers, 221 Rapid prototyping, 363 Rapid solidification processing, 646 Rat tail defect, 247 Reaction porosity, 257–262 Reactive casting techniques, 652 Reactive metals, casting of, 664–668 Reclamation, of moulding sand, 231 Rectification, of defects, 305–314 Reduced pressure test, for liquid metals, 509 Refinement, of structure, 77, 83–96, 505 mould coatings as medium for, 93 Refractories as sources of gas contamination, 260, 264 in investment casting, 568 in mould coatings, 218 mould, 198, 215–217 Refractoriness, 179, 199 Refractory inclusions, 243 Replicast process, 661 Residual stresses, 287–290 due to welding, 311 Resin binders, 206–213 curing of, 203–213, 481–485, 510–554 Resistance furnaces, 495 Restricted neck feeding, 109, 152 Retained strength, of moulding material, 195, 212 Reverbatory furnaces, 492 Reversal casting, 116 Reynolds number, 27 Rheocasting, 668 Ribs, 432 Ring heads, 120 Ripening, 61 Risers, see Feeder heads Risk assessment, 684 Robotic coating, 569, 577Index 715 Robots, in die casting, 609 in fettling, 533 in pouring, 522 Rockwell hardness test, 332 Rod feeding, 141, 145 Roll casting, 642 Rotary degassing, 266 Rotary furnaces, 292 Rotary moulding systems, 466, 658 Runners, see Gating systems Safety at work, 682–685 Safety factors in design, 398, 401 Salt cores in gravity die casting, 593 in pressure die casting, 611 Sampling for inspection, 324 of melts, 509–511 for quality control, 353–358 Sand adherence, 252–254 Sand casting process, 444–542 limitations of, 548 Sand, compaction of, 454–466 Sand cooling, 222, 227 Sand inclusions, 241 Sand mills and mixers, 220–226 Sand preparation, 220–231 Sand systems, 226–231 circulation in, 228 Sand reclamation, 231 Sand testing, 182–198 acid demand and pH, 196 active clay, 196 bench life, 191 collapsibility test, 195 compactability, 186 composition and grading tests, 195 expansion test, 195 flowability tests, 186 gas evolution, 192 hot distortion test, 193 hot strength tests, 194 impact penetration test, 192 mechanical grading, 197 moisture tests, 195 permeability tests, 188 reproducibility in, 182 scratch hardness test, 191 shatter test, 191 specimens for, 183 strength tests, 184–186 surface hardness tests, 188 for high temperature properties, 193 for chemically bonded sands, 190–193 Sand-to-metal ratio, 234 Sands, base, 198 see also Moulding material Sandslingers, 465 Sawing, 529 Scabs erosion, 246 expansion, 246–251 Scaling resistance, 404, 415 Scavenging gas treatments, 265 Scleroscope, 332 Screens in gating, 39 in radiography, 340, 341 in sand systems, 227 Secondary steelmaking, 508 Section sensitivity of properties, 328–330, 381 Section thickness in design, 424–428 Sedimentation, 197 Segment ladles, 516 Segregation, 294–300 channel, 300 dendritic, 295 freckle, 300 grain boundary, 295 gravity, 299 homogenisation, 300, 538 in centrifugal castings, 638 influence in hot tearing, 282 influence on properties, 304 inherent tendency to, 294 inverse, 299 macro-, 297 micro-, 295 patterns of, 297 Selective Laser Sintering, 364 Self tapping furnace, 503, 522, 576, 584 Semicentrifugal casting, 622, 685 Semi-solid casting, 668–670716 Index Shaft furnaces, 492 Shanks, 511 Shape defects on pouring, 240 Shape factor in feeding, 109, 121, 129 Shape features of castings engineering aspects of, 437 in design, 420–440 influence in solidification, 107–109, 122 Shape, suitability for casting, 2, 370 Shaped charges in melting, 503 Shaping of metals, 1, 366–371 Shared feeder heads, 140 Shatter test, 191 Shaw process, 587 Shear test, for moulding materials, 185 Shell moulded castings applications of, 56 characteristics of, 558 dimensional accuracy of, 559 defects in, 560 Shell moulding, 550–563 binders, 550 closing, 554 cold process, 558 D process, 556 location, 554 machines, 555 production, 550 comparative costs of, 562, 617–619 Shell moulds, ceramic, 567, 569, 570 Shockless jolt principle, 457 Short run castings, 240 Shotblasting, 526 Shower nucleation, 95 Shrinkage cavities in castings, 271–277 in feeder heads, 127 Shrinkage, liquid, 48 Shrinkage, solidification, 118 Side gating, 31 Sievert’s Law, 255 Sieves, 197 Silica, 199, 247, 569 Silicon carbide as abrasive, 531 as chill, 159 Sillimanite, 218, 570 Simpson mixer, 220 Simulation, process, 168 Single crystal casting, 81, 583 Sinks, 274 Skeleton patterns, 454 Skimmer core, 38 Skin drying of moulds, 476 Skin forming alloys, 102 Skull melting, 665–667 Slag inclusions, 243 Slags, 496, 497, 500 Slitting, 529 Slug melting, 503–668 Slurry casting, 668–670 Slush casting, 648 Snapflasks, 448, 453 Sodium silicate, as binder, 210, 485 Soldering, 312 Solidification characteristics of alloys, 100–107 contraction, 100, 118 directional, for feeding, 101, 104 eutectic, 64 expansion stage, in cast irons, 105 geometric influences on, 107–110 modes of, 100–107 modelling, 164 of alloys forming solid solutions, 56 of centrifugal castings, 626 of pure metals, 54 rate, influence on structure, 70–73, 79, 85–90 significance of, in castings, 51 time, 108–110, 116 criterion in feeding, 118–123 influence of chilling on, 156–161 unidirectional, 80, 583 see also Crystallisation see also Feeding of castings see also Structure Soluble cores, 593, 663 see also Salt cores Soundness of castings, 51, 100–173 hydraulic, 79, 84, 301, 304 testing for, 333 Specific surface, 201 Specifications, role of, 323 see also Standards Specimen size effect, 331Index 717 Spheroidal graphite in cast iron, 84, 88, 89 see also Cast irons Spinner, see Whirlgate Spiral fluidity test, 16 Spirit based mould coatings, 218 Splat cooling, 87, 646 Spray casting, 646 Spray forming, 646 Sprigs, 449, 470 Sprue, 26 dimensions of, 28 Squeeze action, machine moulding, 457 Squeeze casting, 649 Stack moulding, 444 Stamping of castings, 325 Standards for castings, 323, 331, 687 for environmental protection, 680 for inspection and testing, 359, 692 for quality management, 321, 359 see also Appendix Staples, 480 Starch, as binder, 205 Straube-Pfeiffer test, 509 Steam porosity, 258 Steelmoulders’ composition, 215 Steels, see Cast steels Step gates, 35, 116 Stepped joints, 449 Stereolithography, 363 Stokes’s law, 197, 242, 627 Stove drying of cores, 484 of moulds, 181, 472–474 Straightening, 292 Strainer core, 39 Stream droplet degassing, 268 Streamlining of casting design, 420, 437 of gating systems, 27, 35 Strength, of alloys, 411–414 Strength-weight ratio, 413 Stress concentration, at defects, 302 factor, 302, 388, 431, 437 Stress corrosion, 404, 415 Stress relief, 289–291, 539 of welds, 311 Stresses contraction, 277–279 design to minimise, 430 in welding, 311 relief of, 290 residual, 287–290 Strickle moulding, 454 Strip time, of moulding material, 191 Structure cast, characteristics of, 7, 379–385 cellular, 62 chill zone, 80 columnar, 55, 71, 78–80 control of, 76–96 cored, 62, 295 dendritic, 60–62, 71–74, 86 development of, in solidification, 51–96 directionality of, influence on properties, 78 eutectic, 64–69 equiaxed, 64, 65, 73–76, 79, 80 grain, 52, 59, 77 of castings, 7, 70–96 of centrifugal castings, 639–642 refinement of, 77, 83–96, 505 significance of, 76 Structure-sensitive properties, 379–385, 397–420 Studs, 48, 423, 476, 487 Substructure, 60–69, 77, 82, 84, 380 Sulphur as reaction inhibitor, 214, 262 Supercooling, see Undercooling Superheating, influence on grain structure, 79, 93 Surface characteristics of castings, 371 Surface coatings, see Coatings Surface defects, 301 test for, 334 Surface drying of moulds, 181, 473 Surface films, on liquid metals, 20, 241, 244 Surface finish of castings, 377 measurement of, 325 Surface porosity, 274 Surface punctures, 274 Surface, rough, on castings, 252 Surface tension, of liquid metals, 20718 Index Surface treatment of castings, 395 Swarf contamination from, 263 melting of, 494, 496 Sweep moulding, see Strickle moulding Swelling capacity, of clays, 198, 204 Synthetic sands, 198, 215, 229 T sections, design of, 429, 432 Taper draft, moulding, 422 of downrunner, 28 of dies, 600 padding, 154 Tapping temperature, 512 Teapot ladle, 513 Tears, see Hot tears Temperature gradients effect in feeding, 101, 113–117 influence on structure, 59, 64, 70–74, 79 influence in hot tearing, 284, 285 Temperature, measurement of, 512 Temperature, tapping and pouring, 512 Tempering, 539 Tensile test, 331 for moulding materials, 185 Test bars, 327–330 relationship to castings, 328, 330 Testing material and product, 324–351 mechanical, 326–333 of moulding materials, see Sand testing non-destructive, see Non-destructive testing Thermal diffusivity of alloys, 104 Thermal lance cutting, 530 Thermal reclamation of sand, 233 Thermit reaction, 147 Thickness effects in heat treatment, 381, 538 of metal, in design, 426–428 minimum, of mould members, 423 see also Section sensitivity Thixocasting, 669 Tiles, refractory, 30, 45, 244 Titanium as nucleant, 665 casting of, 667, 669 Toe cracking, 309 Tooling costs, 7, 368 Tolerances, see Dimensional accuracy and tolerances Top gating, 31 Topping up, 145 Toughness, of moulding material, 191 Tower furnace, 492 Transparent systems, solidification in, 67, 76 Transverse test, for moulding materials, 185 Traps, in gating systems, 37 Trough mixers, 224 Turbulent flow, 27 Turnings, see Swarf Ultrasonic testing, 347–350 Underbead cracking, 309 Undercooling, 85 constitutional, 59 Unidirectional solidification, 80, 583 Unit sand practice, 230 Unbonded sand, 213 Unicast process, 590 Upward fill casting, 653–657 Uranium, melting and casting of, 667 Urea formaldehyde binders, 206 Urea furan binders, 209 V process, 657 Vacural process, 605 Vacuum–compression treatment of cast metal, 270 Vacuum cooling, of sand, 222 Vacuum die casting, 605 Vacuum fluidity test, 18 Vacuum melting, 264, 500, 665 in investment casting, 576, 584, 670 in reactive metal casting, 665–667 Vacuum squeeze moulding machine, 465 Van’t Hoff equation, 256Index 719 Ventilation, 535–537 Venting of blind feeder heads, 144 of cores, 479, 480 of moulds, 255, 470 for coreblowing, 477, 479 Vibration for stress relief, 291 influence on structure, 95 in moulding, 460 Vibratory shakeout, 524 Vibratory squeeze moulding, machine, 460 Vickers hardness test, 332 Viscosity of liquid metals, 15 of shell moulding binders, 551 Void nucleation, 104, 259 Volatile mould dressings, 218–220, 486 Volume feed capacity criterion in feeding, 118 Volume to surface area ratio of castings, 109 Wall thickness of castings, see Thickness Warm box process, 483 Washburn core, 109 dimensions of, 152 Washes, see Coatings Waste management, 676 Wax patterns for investment casting, 565 elimination of, 574 Wear resistance of alloys, 403, 414 Web gate, 35 Webs, 287 Wedge test for cast iron, 510 Weight range capability of castings, 2, 370 Weight variation of castings, 377 Weighting of moulds, 48, 487 Weld decay tests, 333 Weld fabrication, 370 castings in, 370, 386–392 Weldability of alloys, 309, 311, 406, 417 Welding, 1, 306–309 arc, 307 gas, 307 development of stresses in, 311 fluxes, 307 influence on mechanical properties, 309 influence on corrosion resistance, 311 of steel castings, 308 preparation for, 307 Wet strength of moulding material, 248 Whirlgate, 38 Whirlgate head, 144 Whistlers, 255, 471 Williams head, see Atmospheric head Wrought products, compared with castings, 382–385 X sections, in design, 429 X-ray computed tomography, 344 X-ray fluoroscopy for study of flow in moulds, 29 possibilities for research into cavity formation, 275 X-ray sources for radiography, 343 X-rays, 339 Yield casting, 112, 368 overall, 114 Yield stress, 397 Young’s modulus, 397, 407 Zinc alloy die castings, 595–597, 602 Zircon sand, 199, 216 Zirconium, casting of, 665, 667
كلمة سر فك الضغط : books-world.net The Unzip Password : books-world.net أتمنى أن تستفيدوا من محتوى الموضوع وأن ينال إعجابكم رابط من موقع عالم الكتب لتنزيل كتاب Foundry Technology رابط مباشر لتنزيل كتاب Foundry Technology 
|
|