Admin مدير المنتدى


عدد المساهمات : 18726 التقييم : 34712 تاريخ التسجيل : 01/07/2009 الدولة : مصر العمل : مدير منتدى هندسة الإنتاج والتصميم الميكانيكى
 | موضوع: كتاب Machine Elements in Mechanical Design - Sixth Edition الإثنين 07 أغسطس 2023, 1:53 am | |
| 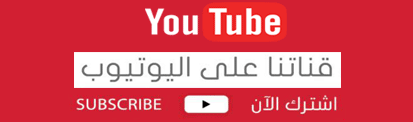
أخواني في الله أحضرت لكم كتاب Machine Elements in Mechanical Design Sixth Edition Robert L. Mott University of Dayton Edward M. Vavrek Purdue University Jyhwen Wang Texas A&M University
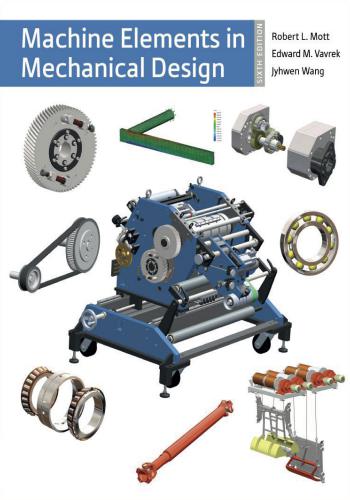 و المحتوى كما يلي :
2–9 Tool Steels 51 2–10 Cast Iron 51 2–11 Powdered Metals 53 2–12 Aluminum 56 2–13 Zinc Alloys and Magnesium 58 2–14 Nickel-Based Alloys and Titanium 59 2–15 Copper, Brass, and Bronze 60 2–16 Plastics 61 2–17 Composite Materials 64 2–18 Materials Selection 76 References 81 Internet Sites Related to Design Properties of Materials 82 Problems 83 Supplementary Problems 85 Internet-Based Assignments 86 3 Stress and Deformation Analysis 87 The Big Picture 87 You Are the Designer 88 3–1 Objectives of This Chapter 91 3–2 Philosophy of a Safe Design 91 3–3 Representing Stresses on a Stress Element 92 3–4 Normal Stresses Due to Direct Axial Load 93 3–5 Deformation Under Direct Axial Load 94 3–6 Shear Stress due to Direct Shear Load 94 3–7 Torsional Load—Torque, Rotational Speed, and Power 94 3–8 Shear Stress due to Torsional Load 96 3–9 Torsional Deformation 98 3–10 Torsion in Members Having Non-Circular Cross Sections 98 3–11 Torsion in Closed, Thin-Walled Tubes 100 3–12 Torsion in Open, Thin-Walled Tubes 100 3–13 Shear Stress Due to Bending 102 Preface ix Acknowledgments xv PART 1 Principles of Design and Stress Analysis 1 1 The Nature of Mechanical Design 2 The Big Picture 2 You Are the Designer 7 1–1 Objectives of This Chapter 8 1–2 The Design Process 8 1–3 Skills Needed in Mechanical Design 9 1–4 Functions, Design Requirements, and Evaluation Criteria 10 1–5 Example of the Integration of Machine Elements into a Mechanical Design 12 1–6 Computational Aids 13 1–7 Design Calculations 14 1–8 Preferred Basic Sizes, Screw Threads, and Standard Shapes 14 1–9 Unit Systems 20 1–10 Distinction Among Weight, Force, and Mass 21 References 22 Internet Sites for General Mechanical Design 22 Internet Sites for Innovation and Managing Complex Design Projects 23 Problems 23 2 Materials in Mechanical Design 25 The Big Picture 25 You Are the Designer 26 2–1 Objectives of This Chapter 27 2–2 Properties of Materials 27 2–3 Classification of Metals and Alloys 39 2–4 Variabilty of Material Properties Data 43 2–5 Carbon and Alloy Steel 43 2–6 Conditions for Steels and Heat Treatment 46 2–7 Stainless Steels 51 2–8 Structural Steel 51 CONTENTSiv Contents 5–8 Recommended Design and Processing for Fatigue Loading 188 5–9 Design Factors 189 5–10 Design Philosophy 189 5–11 General Design Procedure 191 5–12 Design Examples 193 5–13 Statistical Approaches to Design 203 5–14 Finite Life and Damage Accumulation Method 204 References 207 Internet Sites Related to Design 208 Problems 208 6 Columns 217 The Big Picture 217 6–1 Objectives of This Chapter 218 You Are the Designer 219 6–2 Properties of the Cross Section of a Column 219 6–3 End Fixity and Effective Length 220 6–4 Slenderness Ratio 221 6–5 Long Column Analysis: The Euler Formula 221 6–6 Transition Slenderness Ratio 222 6–7 Short Column Analysis: The J. B. Johnson Formula 223 6–8 Column Analysis Spreadsheet 226 6–9 Efficient Shapes for Column Cross Sections 227 6–10 The Design of Columns 229 6–11 Crooked Columns 232 6–12 Eccentrically Loaded Columns 233 References 237 Problems 237 PART 2 Design of a Mechanical Drive 241 7 Belt Drives, Chain Drives, and Wire Rope 244 The Big Picture 244 You Are the Designer 246 7–1 Objectives of This Chapter 246 7–2 Kinematics of Belt and Chain Drive Systems 246 7–3 Types of Belt Drives 251 7–4 V-Belt Drives 252 7–5 Synchronous Belt Drives 262 3–14 Shear Stress Due to Bending – Special Shear Stress Formulas 103 3–15 Normal Stress Due to Bending 104 3–16 Beams with Concentrated Bending Moments 105 3–17 Flexural Center for Beam Bending 110 3–18 Beam Deflections 110 3–19 Equations for Deflected Beam Shape 112 3–20 Curved Beams 113 3–21 Superposition Principle 120 3–22 Stress Concentrations 122 3–23 Notch Sensitivity and Strength Reduction Factor 129 References 129 Internet Sites Related to Stress and Deformation Analysis 129 Problems 129 4 Combined Stresses and Stress Transformation 142 The Big Picture 142 You Are the Designer 143 4–1 Objectives of This Chapter 144 4–2 General Case of Combined Stress 144 4–3 Stress Transformation 145 4–4 Mohr’s Circle 150 4–5 Mohr’s Circle Practice Problems 157 4–6 Mohr’s Circle for Special Stress Conditions 159 4–7 Analysis of Complex Loading Conditions 164 Reference 164 Internet Sites Related to Stress Transformation 164 Problems 165 5 Design for Different Types of Loading 166 The Big Picture 166 You Are the Designer 168 5–1 Objectives of This Chapter 168 5–2 Types of Loading and Stress Ratio 168 5–3 Failure Theories 172 5–4 Design for Static Loading 173 5–5 Endurance Limit and Mechanisms of Fatigue Failure 175 5–6 Estimated Actual Endurance Limit, sn= 178 5–7 Design for Cyclic Loading 185Contents v 9–11 Computer-Aided Spur Gear Design and Analysis 407 9–12 Use of the Spur Gear Design Spreadsheet 409 9–13 Power-Transmitting Capacity 412 9–14 Plastics Gearing 413 9–15 Practical Considerations for Gears and Interfaces with other Elements 418 References 422 Internet Sites Related to Spur Gear Design 423 Problems 423 10 Helical Gears, Bevel Gears, and Wormgearing 428 The Big Picture 428 You Are the Designer 430 10–1 Objectives of This Chapter 430 10–2 Forces on Helical Gear Teeth 430 10–3 Stresses in Helical Gear Teeth 433 10–4 Pitting Resistance for Helical Gear Teeth 433 10–5 Design of Helical Gears 434 10–6 Forces on Straight Bevel Gears 439 10–7 Bearing Forces on Shafts Carrying Bevel Gears 441 10–8 Bending Moments on Shafts Carrying Bevel Gears 444 10–9 Stresses in Straight Bevel Gear Teeth 444 10–10 Forces, Friction, and Efficiency in Wormgear Sets 456 10–11 Stress in Wormgear Teeth 461 10–12 Surface Durability of Wormgear Drives 461 10–13 Emerging Technology and Software for Gear Design 464 References 466 Internet Sites Related to Helical Gears, Bevel Gears, and Wormgearing 467 Problems 467 11 Keys, Couplings, and Seals 470 The Big Picture 470 You Are the Designer 471 11–1 Objectives of This Chapter 471 11–2 Keys 471 11–3 Materials for Keys 476 11–4 Stress Analysis to Determine Key Length 476 7–6 Chain Drives 278 7–7 Wire Rope 292 References 301 Internet Sites Related to Belt Drives and Chain Drives 301 Problems 302 8 Kinematics of Gears 304 The Big Picture 304 You Are the Designer 308 8–1 Objectives of This Chapter 308 8–2 Spur Gear Styles 309 8–3 Spur Gear Geometry-Involute-Tooth Form 309 8–4 Spur Gear Nomenclature and Gear-Tooth Features 311 8–5 Interference Between Mating Spur Gear Teeth 321 8–6 Internal Gear Geometry 322 8–7 Helical Gear Geometry 323 8–8 Bevel Gear Geometry 326 8–9 Types of Wormgearing 330 8–10 Geometry of Worms and Wormgears 332 8–11 Gear Manufacture 337 8–12 Gear Quality 340 8–13 Velocity Ratio and Gear Trains 343 8–14 Devising Gear Trains 351 References 356 Internet Sites Related to Kinematics of Gears 357 Problems 357 9 Spur Gear Design 362 The Big Picture 362 You Are the Designer 363 9–1 Objectives of This Chapter 364 9–2 Concepts From Previous Chapters 364 9–3 Forces, Torque, and Power in Gearing 365 9–4 Introduction to Stress Analysis for Gears 374 9–5 Bending Stress in Gear Teeth 374 9–6 Contact Stress in Gear Teeth 387 9–7 Metallic Gear Materials 389 9–8 Selection of Gear Materials 393 9–9 Design of Spur Gears to Specify Suitable Materials for the Gears 400 9–10 Gear Design for the Metric Module System 405vi Contents 13–10 Robust Product Design 560 References 560 Internet Sites Related to Tolerances and Fits 561 Problems 561 14 Rolling Contact Bearings 563 The Big Picture 563 You Are the Designer 564 14–1 Objectives of This Chapter 565 14–2 Types of Rolling Contact Bearings 565 14–3 Thrust Bearings 567 14–4 Mounted Bearings 568 14–5 Bearing Materials 569 14–6 Load/Life Relationship 570 14–7 Bearing Manufacturers’ Data 571 14–8 Design Life 575 14–9 Bearing Selection: Radial Loads Only 576 14–10 Bearing Selection: Radial and Thrust Loads Combined 576 14–11 Bearing Selection from Manufacturers’ Catalogs 578 14–12 Mounting of Bearings 578 14–13 Tapered Roller Bearings 580 14–14 Practical Considerations in the Application of Bearings 582 14–15 Importance of Oil Film Thickness in Bearings 584 14–16 Life Prediction under Varying Loads 585 14–17 Bearing Designation Series 586 References 586 Internet Sites Related to Rolling Contact Bearings 587 Problems 587 15 Completion of the Design of a Power Transmission 589 The Big Picture 589 15–1 Objectives of This Chapter 590 15–2 Description of the Power Transmission to be Designed 590 15–3 Design Alternatives and Selection of the Design Approach 591 15–4 Design Alternatives for the Gear-Type Reducer 592 15–5 General Layout and Design Details of the Reducer 593 11–5 Splines 479 11–6 Other Methods of Fastening Elements to Shafts 482 11–7 Couplings 486 11–8 Universal Joints 494 11–9 Other Means of Axial Location 499 11–10 Types of Seals 502 11–11 Seal Materials 503 References 505 Internet Sites for Keys, Couplings, and Seals 505 Problems 506 12 Shaft Design 509 The Big Picture 509 You Are the Designer 510 12–1 Objectives of This Chapter 510 12–2 Shaft Design Procedure 510 12–3 Forces Exerted on Shafts by Machine Elements 513 12–4 Stress Concentrations in Shafts 516 12–5 Design Stresses for Shafts 517 12–6 Shafts in Bending and Torsion Only 520 12–7 Shaft Design Examples—Bending and Torsion Only 521 12–8 Shaft Design Example—Bending and Torsion with Axial Forces 529 12–9 Spreadsheet Aid for Shaft Design 533 12–10 Shaft Rigidity and Dynamic Considerations 534 12–11 Flexible Shafts 535 References 535 Internet Sites for Shaft Design 535 Problems 536 13 Tolerances and Fits 546 The Big Picture 546 You Are the Designer 547 13–1 Objectives of This Chapter 547 13–2 Factors Affecting Tolerances and Fits 547 13–3 Tolerances, Production Processes, and Cost 548 13–4 Preferred Basic Sizes 550 13–5 Clearance Fits 551 13–6 Interference Fits 554 13–7 Transition Fits 555 13–8 Stresses for Force Fits 555 13–9 General Tolerancing Methods 557Contents vii 18–3 Helical Compression Springs 659 18–4 Stresses and Deflection for Helical Compression Springs 666 18–5 Analysis of Spring Characteristics 667 18–6 Design of Helical Compression Springs 670 18–7 Extension Springs 677 18–8 Helical Torsion Springs 681 18–9 Improving Spring Performance by Shot Peening and Laser Peening 687 18–10 Spring Manufacturing 687 References 688 Internet Sites Related to Spring Design 688 Problems 689 19 Fasteners 691 The Big Picture 691 You Are the Designer 692 19–1 Objectives of This Chapter 693 19–2 Bolt Materials and Strength 693 19–3 Thread Designations and Stress Area 695 19–4 Clamping Load and Tightening of Bolted Joints 696 19–5 Externally Applied Force on a Bolted Joint 698 19–6 Thread Stripping Strength 700 19–7 Other Types of Fasteners and Accessories 700 19–8 Other Means of Fastening and Joining 702 References 702 Internet Sites Related to Fasteners 703 Problems 704 20 Machine Frames, Bolted Connections, and Welded Joints 705 The Big Picture 705 You Are the Designer 706 20–1 Objectives of This Chapter 706 20–2 Machine Frames and Structures 706 20–3 Eccentrically Loaded Bolted Joints 710 20–4 Welded Joints 712 References 719 Internet Sites for Machine Frames, Bolted Connections, and Welded Joints 720 Problems 721 15–6 Final Design Details for the Shafts 605 15–7 Assembly Drawing 608 References 611 Internet Sites Related to Transmission Design 612 PART 3 Design Details and Other Machine Elements 613 16 Plain Surface Bearings 614 The Big Picture 614 You Are the Designer 616 16–1 Objectives of This Chapter 616 16–2 The Bearing Design Task 616 16–3 Bearing Parameter, mn/p 617 16–4 Bearing Materials 618 16–5 Design of Boundary-Lubricated Bearings 619 16–6 Full-Film Hydrodynamic Bearings 624 16–7 Design of Full-Film Hydrodynamically Lubricated Bearings 625 16–8 Practical Considerations for Plain Surface Bearings 630 16–9 Hydrostatic Bearings 632 16–10 The Kugel Fountain—A Special Example of a Hydrostatic Bearing 635 16–11 Tribology: Friction, Lubrication, and Wear 635 References 638 Internet Sites Related to Plain Bearings and Lubrication 639 Problems 640 17 Linear Motion Elements 641 The Big Picture 641 You Are the Designer 643 17–1 Objectives of This Chapter 644 17–2 Power Screws 644 17–3 Ball Screws 649 17–4 Application Considerations for Power Screws and Ball Screws 652 References 652 Internet Sites for Linear Motion Elements 653 Problems 653 18 Springs 655 The Big Picture 655 You Are the Designer 656 18–1 Objectives of This Chapter 657 18–2 Kinds of Springs 657viii Contents 22–14 Drum Brakes 768 22–15 Band Brakes 772 22–16 Other Types of Clutches and Brakes 773 References 775 Internet Sites for Clutches and Brakes 775 Problems 775 23 Design Projects 778 23–1 Objectives of This Chapter 778 23–2 Design Projects 778 List of Appendices 781 Appendix 1 Properties of Areas 782 Appendix 2 Preferred Basic Sizes and Screw Threads 784 Appendix 3 Design Properties of Carbon and Alloy Steels 787 Appendix 4 Properties of Heat-Treated Steels 789 Appendix 5 Properties of Carburized Steels 791 Appendix 6 Properties of Stainless Steels 792 Appendix 7 Properties of Structural Steels 793 Appendix 8 Design Properties of Cast Iron—U.S. Units Basis 794 Appendix 8A Design Properties of Cast Iron—SI Units Basis 795 Appendix 9 Typical Properties of Aluminum 796 Appendix 10–1 Properties of Die-Cast Zinc Alloys 797 Appendix 10–2 Properties of Die-Cast Magnesium Alloys 797 Appendix 11–1 Properties of Nickel-Based Alloys 798 Appendix 11–2 Properties of Titanium Alloys 798 Appendix 12 Properties of Bronzes, Brasses, and Other Copper Alloys 799 Appendix 13 Typical Properties of Selected Plastics 800 Appendix 14 Beam-Deflection Formulas 801 Appendix 15 Commercially Available Shapes Used For Load-Carrying Members 809 Appendix 16 Conversion Factors 829 Appendix 17 Hardness Conversion Table 830 Appendix 18 Stress Concentration Factors 831 Appendix 19 Geometry Factor, I, for Pitting for Spur Gears 834 Answers to Selected Problems 837 Index 848 21 Electric Motors and Controls 723 The Big Picture 723 You Are the Designer 725 21–1 Objectives of This Chapter 725 21–2 Motor Selection Factors 725 21–3 AC Power and General Information about AC Motors 726 21–4 Principles of Operation of AC Induction Motors 727 21–5 AC Motor Performance 728 21–6 Three-Phase, Squirrel-Cage Induction Motors 729 21–7 Single-Phase Motors 731 21–8 AC Motor Frame Types and Enclosures 733 21–9 Controls for AC Motors 735 21–10 DC Power 742 21–11 DC Motors 742 21–12 DC Motor Control 744 21–13 Other Types of Motors 744 References 746 Internet Sites for Electric Motors and Controls 746 Problems 747 22 Motion Control: Clutches and Brakes 749 The Big Picture 749 You Are the Designer 751 22–1 Objectives of This Chapter 751 22–2 Descriptions of Clutches and Brakes 751 22–3 Types of Friction Clutches and Brakes 751 22–4 Performance Parameters 756 22–5 Time Required to Accelerate or Decelerate a Load 758 22–6 Inertia of a System Referred to the Clutch Shaft Speed 760 22–7 Effective Inertia for Bodies Moving Linearly 761 22–8 Energy Absorption: Heat-Dissipation Requirements 762 22–9 Response Time 762 22–10 Friction Materials and Coefficient of Friction 764 22–11 Plate-Type Clutch or Brake 765 22–12 Caliper Disc Brakes 767 22–13 Cone Clutch or Brake 767 848 A Abrasion resistance, 298 Adhesives, 702 Aerospace Materials System (AMS), 39–40 Air blasting, 466 Allowable stress, 189 Allowance, 547, 548 Aluminum, 56–58, A–9 casting alloys, 57–58 forging alloys, 58 Aluminum Association (AA), 39 American Gear Manufacturers Association, (AGMA), 311, 317, 320, 381, 382, 390–395, 397–399, 415, 416, 419, 420, 433, 437, 438, 444–453, 455, 461, 462, 465, 637 American Iron and Steel Institute (AISI), 39 American National Standards Institute, (ANSI), standards, 547, 548, 551, 554, 584 American Society for Testing and Materials, (ASTM), 16, 30, 31, 34–36, 40–43, 51–53, 663–666, A–7, A–8 American Society of Mechanical Engineers, (ASME), standard, 551, 554, 558 American standard beam shapes, 16, A–15–10 Angles, equal and unequal leg, 18, A–15–1, A–15–2, A–15–3 Annealing, 47 Areas, properties of, A–1 Austempered ductile iron (ADI), 53, A–8 Automotive universal joints, 495, 496 Average stress, 100 Axiomatic design, 8 B Babbitt, 618 Ball screws, 649–651 column buckling, 652 efficiency, 651 materials, 652 performance, 649–650 torque, 651 travel life, 651 Basic sizes, preferred, 14, A–2 Beams, 104 bending stress, 104–105 concentrated bending moment, 105–109 curved, 113–120 deflections, 110–112, A–14 flexural center, bending, 110 shapes, A–15 shear center, 110 Bearings, plain surface, 615–638 bearing characteristic number, 627 bearing parameter, mn/p, 616–618 boundary lubrication, 619–624 operating temperature, 620–621 oscillating loading, 623–624 pV factor, 619–620 wear considerations, 624 clearance, diametral, 621–622, 626 coefficient of friction variable, 617, 619, 628 design of full film hydrodynamic bearings, 624–630 film thickness variable, 624–626 friction torque and power, 640 full-film (hydrodynamic) lubrication, 615, 616, 624–625 geometry, 615 grooving, 630–631 hydrostatic bearing performance, 632–635 journal, 614 Kugel Fountain, 635 length, 619 materials, 618–619 mixed-film lubrication, 616, 624 mn/p parameter, 617–618 pressure, 620, 624–625 pV factor, 619–620 Sommerfeld number, 627–628 Stribeck curve, 617 surface roughness, 625 temperature of lubricant, 626–627 viscosity, 627 wear factor, 638 Bearings, rolling contact, 563–586 brinelling, 571 design life, 575–576 dynamic load rating, 571 equivalent load, 576–578 flange units, 569 grease for, 582, 583 installation, 583 life factor, 575 load/life relationship, 570–571 locknuts, 579–580 lubrication, 582–583 manufacturers’ data, 571–575 materials, 569–570 mean effective load, 585–586 mounted bearings, 568–569 mounting, 578–580 oil film thickness, 584–585 pillow blocks, 591 preloading, 583 rated life (L10), 571 reliability, 578 rotation factor, 576 sealing, 583–584 selection, 576–578 sizes, 571 speed factor, 575 speeds, limiting, 584 standards, 584 static load rating, 571 INDEXIndex 849 pitch, 278–279 power ratings, 283–285 roller chain, 278–280 service factors, 286 sizes, 279 sprockets, 278 styles, 279 U.S. units, 279 Channel beam shapes, 16, A–15–4 to A–15–8 Charpy test, 36 Clearance fits, 551–553, 626 Clevis joints, 126 Clutches and brakes, 749–774 actuation, 753–756 applications, typical, 752 band brakes, 753, 772–773 brake, defined, 750 brake, fail-safe, 754 clutch-brake module, 751 clutch, coupling, 751 clutch, defined, 750 coefficient of friction, 764–765 cone clutch or brake, 752–753, 767–768 disc brakes, 752, 767 drum brakes, 768–772 eddy current drive, 774 energy absorption, 762 fiber clutch, 774 fluid clutch, 774 friction materials, 764–765 inertia, effective, 760–762 jaw clutch, 773 overload clutch, 774 performance, 756–757 plate type, 756, 765–767 radius of gyration, 758 ratchet, 774 response time, 762–764 single-revolution clutch, 774 slip clutch, 751, 755 sprag clutch, 774 tensioners, 774 types, 751–756 wear, 764–765 Wk2, inertia, 758–764 wrap spring clutch, 774 Coefficient of friction, 457, 458, 619, 764–765 Coefficient of thermal expansion, 39 Collars, 501 Columns, 217–239 buckling, 217–218 column constant, 222 crooked, 232–233 design factors for, 222 design of, 229–232 eccentrically loaded, 233–236 effective length, 220–221 efficient shapes for column cross sections, 227–229 end fixity, 220–221 Euler formula, 221–223 J. B. Johnson formula, 223–226 radius of gyration, 218 secant formula, 233–234 slenderness ratio, 221 Combined stresses, 144–150 Complex loading conditions, 164 Composite materials. See Materials, composites Computational aids, 13–14. See also MDESIGN software; Spreadsheets as design aids stiffness, 583 take-up bearings, 569 tapered roller bearings, 580–582 thrust bearing, 567–568 thrust factor, 581 tolerances, 584 types, 565–567 varying loads, 585–586 Belleville spring, 657–658 Belt drives, 246–251 belt, chain speed, 246 configuration, 248 fixed center distances, 276 kinematics of, 246–251 multiple shaft drive, 276–277 pitch circle diameter, 247 pulleys, 246 span belt, 249 speed increaser, 248 speed reducer, 248, 249, 251 twin power belts, 276, 278 types of, 251–252 whip belt, 249 Belt pulleys, flat, 516 Belts and chains. See Chain drives; V-belt drives Bending normal stress, 104–105 shear stress, 102–103 Bolted connections, 696–698, 710–712 Brakes. See Clutches and brakes Brass, 60–61 properties, A–12 Brazing, 702 Brinell hardness, 31 Bronze, 60–61, 392–393 properties, A–12 sintered, 618 Buckling of columns, 189 Buckling of springs, 667 Bushing, split taper, 485 C Carbo-nitriding, 49 Carburized steels, properties of, A–5 Carburizing, 49, 391–392, A–11 of gear teeth, 392 Cardan universal joint, 494 Case hardening flame hardening, 48–49 heat treating operations, cautions, 49–50 induction hardening, 48–49 Cast iron, 392–393 SI units (design properties) basis, A–8A U.S. units (design properties) basis, A–8 Ceramics, bearing material, 570 Chain drives, 246–251, 278–291 attachments, 279 center distance formula, 281–282 configuration, 248 conveyor chain, 279, 282 design of, 279–291 forces on shafts, 514–515 kinematics of, 246–251 length of chain formula, 282 lubrication, 286–291 metric sizes, 280 multiple strands, factors, 281850 Index Direct axial load deformation, 94 normal stress, 93–94 Direct Gear Design , 465 Direct shear stress, 94 Distortion energy theory (DET), 174, 510, 518–520 Double cardan universal joint, 494 Drawings, assembly, 608–611 shaft details, 605–608 Drop weight test, 36 Ductile iron, 52–53, A–8 Ductility, 29 E Early cycle yielding, 186 Elastic limit, 28 Electrical conductivity, 39 Electrical resistivity, 39 Endurance limit, 178–185 actual, 178 graph vs. tensile strength, 179 size factors, U.S. customary units, 181 Endurance strength, 36 Equivalent torque, 161 Euler formula for columns, 221–223 Evaluation criteria, 10–11 Extra improved plow steel (XIP), 297 F Factor of safety. See Design factor Failure modes, 92, 645 Failure modes and effects analysis (FMEA), 9 Failure theories, 172–173 Fasteners, 691–702 adhesives, 702 American Standard, 695 bolted joints, 696–698 bolt materials, 693–695 brazing, 702 clamping load, 696–697 coatings and finishes, 695 head styles, 692 locking devices, 701 metric, 696 screws, 693 set screws, 700 soldering, 702 strength, 693–695 thread designations, 695–696, A–2 thread stripping, 700 tightening torque, 697 washers, 698 Fatigue, 36 failures, stress analysis high-cycle fatigue (HCF), 175–176 low-cycle fatigue (LCF), 175–178 loading, 169, 188–189 resistance, 298 Fiber core (FC), 292 Fillets, shoulder, 474 Finite-element analysis (FEA), 164 Finite life method, 204–207 Fits, 547–548 for bearings, 601 clearance, 551–553 locational, 553 running and sliding, 551 Concentrated bending moment, 105–109 Connections, keyless, 483–484 Constant velocity (CV) joint, 494 Conversion factors, A–16 Coordinate measurement machine (CMM), 342 Copper, 60–61 properties, A–12 Copper Development Association (CDA), 39 Cornay universal joint, 494–495, 497 Coulomb-Mohr theory (CMT), 174–175 Couplings, 470–505 bellows, 488 chain, 487 D-Flex, 488 Dynaflex , 489 Ever-Flex, 487 flexible, 487–490 floating shaft–type, 493, 494 FORM-FLEX , 489 gear, 488 Grid-Flex, 487 jaw-type, 489 PARA-FLEX , 488 polygon connection, 484–485 rigid, 486–487 Ringfeder Locking Assemblies , 483 Creep, 36–37 Criteria for machine design, 10–11 Critical speed, 534, 535, 652 Crushing resistance, 298 Curved beams composite cross sectional shape, 117–120 cross sectional shape, 114–116, 118 general procedure, bending moment, 114–117 stress analysis, 113–114, 120 Cyaniding, 49 Cyclic loading brittle materials, 188 ductile materials, 185–186 Smith diagram, 186–188 D Damage accumulation method, 204–207 Decision analysis, 592 Deflected beam shape, equations, 112–113 Deformation, 94 Density, 38 Designation comparison, steels and aluminum, 42 Design calculations, 14 Design details, power transmission, 589–611 Design factor, 189 Design for six sigma (DFSS), 8 Design philosophy, 189–191 Design problem examples, 193–203 Design procedure, 191–193 Design process axiomatic designx, 8 design for six sigma (DFSS), 8 engineering design process-embodiment design, 9 example, 12–13 failure modes and effects analysis (FMEA), 9 product design for manufacture and assembly, 9 quality function deployment (QFD), 8 total design, 9 TRIZ (Theory of Inventive Problem Solving), 8 Design projects, 778–780 Design requirements, 10–11 Design skills, 9–10Index 851 form milling, 338 hobbing, 338 measurement, 340–343 quality numbers (AGMA standards), 382–384 shaping, 338 stress analysis, 374 worm. See Wormgearing Gears, spur, 311–321, 362–422 addendum, 317 backlash, 317 center distance, 317 clearance, 379 contact stress, 387–389 dedendum, 415 design of, 400–412 dynamic factor, 382 efficiency, 367 elastic coefficient, 387–389 face width, 401, 402 forces on shafts, 513–516 forces on teeth, 513 gear teeth geometry, 311–317 AGMA standards, 311 comments, 317 design considerations, 311 metric module system, 311, 316 geometry, 375, 376 geometry factor, 377, A–19 Hertz stress on teeth, 387 idler, 394 internal, 338 involute tooth form, 309–311 base circle, 310 conjugate curves, 309 constant angular velocity ratio, 309 law of gearing, 310 Lewis form factor, 375, 416 life factor, 394 load distribution factor, 378–380 lubrication, 419–420 manufacture, 337–339 materials, 393–396 material specification, 413 metric module, 405 overload factor, 378 pitch, diameter, 364–365 pitch, diametral, 365 pitting resistance, 413, A–19 plastics gearing, 414–415 power flow, 367 power transmitting capacity, 412–413 pressure angle, 365 quality, 340–343 rack, 349 reliability factor, 394 rim thickness factor, 380–381 size factor, 378 stresses, allowable, 374 stresses in teeth, 374–384 styles, 309 undercutting, 322 Gear trains devising designing, single pair, 353 factoring approach, compound gear trains, 355–356 hunting tooth, 351–353 residual ratio, 354–355 train value, 345–347, 351–356 velocity ratio, 343–345, 353 interference, 554–555 force fits, 554–555 locational, 553 shrink, 554 stresses for, 555–557 transition, 555 Flame hardening, gears, 48, 390, 391 Flexible couplings, 487–490 effects on shafts, 516 torque capacity, shafts, 535 Flexible disc coupling selection procedure, 490–494 Flexural center, 110 Flexural modulus, 30–31 Flexure formula, 105 Fluctuating stress, 170–172 Force, 21 Force fits, 555–557 stresses for, 555–557 Forces exerted on shafts by machine elements, 513–516 Friction, 636 Function statements, 11 G Garter springs, 657 Gearmotors, 462 Gears bevel, 326–330, 439–456 allowable bending strength number, 448–450 bearing forces, 441–444 bending moments on shafts, 443–444 bending stress number, 445 contact stress number, 449–455 dynamic factor, 446 forces on, 439–441 geometry, 326–330 geometry factor, 446, 448 load distribution factor, 446, 447 material selection, 446 miter gears, 326 overload factor, 445 pitch cone angle, 326 pitch diameter, 445 pitches, 445 pitting resistance, 413 practical considerations, 456 reducers, 420 size factor for bending strength, 445–446 stresses in, 444–456 stresses in teeth, 416 tangential force, 445 cutting tools, 338 design process non-standard gearing and gear tooth forms, 465 peening, 465–466 software, 466 helical, 323–326, 430–439 crossed, 305 design of, 434–439 forces on teeth, 430–433, 513 geometry, 323–326 geometry factor, 375–378 helix angle, 514 pitches, 324–325 pitting resistance, 433–434, 437, 438 reducers, 390, 391 stresses in teeth, 433 internal, 322–323 manufacture and quality, 337–343852 Index types, 472–475 Woodruff, 473, 475 Keyseats and keyways dimensions, 475 fillets, 474 selections and installations, 474–475 stress concentrations, 516–517 Kugel Fountain, 635 L Law of gearing, 308 Leaf springs, 657 Lewis form factor, 461 Linear motion elements, 641–652 Loading types, 167, 172 Locknuts, 501, 579 Lubricants, 636–638 solid, 638 Lubrication bearings plain. See Bearings, plain surface rolling contact, 471 chain drives, 286 gears, 419 Lug joints. See also Clevis joints stress concentration factors, 126–129 M Machinability, 35 Machine frames and structures, 705–719 deflection limits, 707 materials, 707 torsion, 709–710 Magnesium alloys, 59 die-cast alloys, A–10–2 Malleable iron, 52, A–8 Mass, 21 Materials in mechanical design, 25–81 aluminum, 56–58, A–9 brass and bronze, 60–61, 393, A–12 carbon and alloy steel, 43–46, 390–391, A–3, A–4 cast iron, 392–393, A–8, A–8A composites, 64–76 advantages of, 67–68 construction of, 70–71 design guidelines, 72–76 filament winding, 67 limitations of, 70–71 preimpregnated materials, 66 pultrusion, 67 reinforcing fibers, 64 sheet molding compound, 67 wet processing, 66 copper, 60–61 decision analysis, 77–78 gear, 393–400 nickel alloys, 59 other considerations, 78–81 plastics, 61–64, 413–418, A–13 powdered metals, 53–56 process, 76 properties, 27–39 selection, 76–81 stainless steels, A–6 structural steel, A–7 thermoplastics, 62 thermosets, 62 titanium, 60, A–11 zinc, 58–59, A–10 Gear-type speed reducers, 420–422, 509, 567, 746 Geometry factor, I, A–19 Gerber criterion, 186 Goodman criterion, 186 Goodman method, 168 Gray iron, 27, 52, A–8, A–8A Greases, 637 H Hardness, 31–34 carburizing, A–5 conversions, 32, A–17 measurement, 33 properties, A–4 Heat treating of steels annealing, 46, 47 carbo-nitriding, 48, 49 carburizing, 49, 50, 391–392 case hardening, 48–49, 391 flame hardening, 48–49, 391 induction hardening, 48–49, 391 nitriding, 48–49, 183, 392 normalizing, 47 tempering, 47–48 through-hardening, 47–48 Heavy-duty industrial type double universal joint, 494, 496 Heavy-duty right angle gear reducer, 456 Hertz stress, 387 Hollow structural shapes (HSS), 18 Hunting tooth, 351–353 Hydrodynamic lubrication, 625–630 Hydrostatic bearings, 632–635 I I-beam shapes, 41, 42, A–15–9 to A–15–13 Idler gear, 347–348 Impact energy, 35–36 Impact loading, 172 Improved plow steel (IPS), 297–298 Inconel alloys, 694 Independent wire rope core (IWRC), 292, 300 Induction hardening, gears, 48–49, 391 Interference, 637 fits, 554–555 Internal gear, 322–323 International Organization for Standardization (ISO), 465 Involute tooth form, 374–376 Izod test, 35 J J. B. Johnson formula for columns, 223–226 J-factor for helical gears, 433–435 for spur gears, 375 K Keys, 471–505 chamfers, 472, 474 design of, 477, 478 forces on, 476, 477 gib head, 472, 475 materials for, 476 parallel, 472, 473 pin, 472–473, 475 sizes, 472, 473 stresses in, 476–478 taper, 472, 475 tolerances, 472, 605Index 853 starters, 736–739 stepping motors, 746 synchronous motors, 730 three phase power, 737 torque motors, 744 universal motor, 730–731 wound rotor motor, 729 Motor starters, 736–740 N Nanotechnology applications, materials, 75–78 National Electrical Manufacturers Association (NEMA), 729 Nickel-based alloys, 59–60 properties, A–11–1 Ni-resist alloy, 59 Nitriding, 183, 392 Non-circular gears, 465 Normalizing, 47 Normal stress, 92 bending, 104–105 direct axial load, 93–94 element, 93 Notch sensitivity, 129 O Oils, 636–637 Open tube, 100 P Palmgren–Miner rule, 585 Percent elongation, 29 Pillow blocks, 568 Pinning, 482–483 Pipe, 19 Pitch circle diameter, 247 Plastic gear materials, 414–415 Plastics, 61–64, 413–415, 619 bearing material, 569 properties, A–13 Poisson’s ratio, 29 Polar section modulus, 97 Polygon connection, 484–485 Powdered metals, 53–56 application, disadvantages, 53 examples, 54 industrial application, 56 processing, 53 proprietary formulations and grades, 53–56 Powder metallurgy (PM). See Powdered metals Power, 94–96 Power screws, 644–649 Acme thread, 644, 647–648 buttress thread, 644 efficiency, 647 lead angle, 647 metric thread, 645–647 power required, 648 self-locking, 647 square thread, 647 torque required, 647 Power–torque–speed relationship, 94 Press fit, 486. See also Fits, interference; Force fits; Shrink fits Pressure angle spur gears, 335 wormgearing, 335 Principal stress, maximum and minimum, 145 Maximum normal stress theory (MNST), 174 Maximum principal stresses, 145 Maximum shear stress, 146 Maximum shear stress theory (MSST), 164, 173–174 MDESIGN software synchronous belts, 303 Mechanical design process. See Design process Megagear , 465 Metallic gear materials allowable bending stress number, AGMA 2001-DO4, 390 Metal Powder Industries Foundation (MPIF), 53 Metals and alloys, classification, 39–42 Metric power screws, 645 trapezoidal screw thread, examples, 646 Metric sizes, keys. See Keys Metric units, 19 MGT Frictionless Drive System , 465 Miner’s rule, 205–206, 585 Minimum principal stresses, 145 Miter gears, 326 Modified Mohr theory (MMT), 175 Modulus of elasticity in shear, 29 spring wire, 668 in tension, 28–29 Mohr’s circle, 150–156 practice problems, 157–159 special stress conditions, 159–164 three-dimensional stresses, 156 tresca stress, 156 von mises stress, 156 Molding, 486 Monel alloys, 569–570 Moore, R.R. fatigue test device, 169 Motion control. See Clutches and brakes Motors, electric, 723–746 AC motors and types, 727, 733–735 AC variable speed drive, 740 AC voltages, 726 brushless DC, 746 capacitor start, 731–732 compound-wound, DC, 744 controls, AC, 735–742 DC motor control, 744 DC motor types, 743–744 DC power, 742 enclosures, motors, 734 frame sizes, 734–735 frame types, 733 induction motors, 729–731 linear motors, 746 NEMA AC motor designs B, C, D, 729 overload protection, 739–740 performance curves, AC motors, 729–733 permanent magnet, DC, 744 permanent split capacitor, 732 printed circuit motors, 746 rectifiers (SCR), 742 selection factors, 725–726 series-wound, DC, 743 servomotors, 744–746 shaded pole, 732–733 shunt-wound, DC, 743 single-phase motors, 731–733 single-phase power, 736 sizes, 736 speed control, AC, 744 speeds, 729 split-phase, 731 squirrel cage motors, 729–731854 Index face, 503, 504 gaskets, 505 O-rings, 502 packings, 505 rigid materials, 505 shafts, 505 T-rings, 502 types, 502–504 Section modulus, 105 polar, 97 Self-locking, 460 Set screws, 485 Shaft design, 509–535 design stresses, 517–520 dynamic considerations, 534–535 equation for diameter, 519 examples, 519–520 fastening elements keyless hub, 483–484 Ringfeder Locking Assemblies , 483 flexible, 535 forces exerted on shafts, 513–516 preferred basic sizes, 521, A–2 procedure, 510–512 stress concentrations in, 516–517 Shapes commonly used metals, 41–42 load-carrying members, A–15 section properties, 16, A–15 types, 16–19. See also Structural shapes Shaping of gears, 339 Shear center, 110 Shear pin, 387 Shear strength, 29 Shear stress, 92 direct, 94 due to torsional load, 96–98 element, 92–93 formulas, 97 horizontal, 102 on keys, 95 positive and negative, 93 special shear stress formulas, 103–104 vertical, 102–103, 518–519 Sheaves, 246 forces on shafts, 515–516 Shock loading, 172 Shot peening, 465, 466 Shoulders, shaft, 501, 579 Shrink fits, 554 stresses for, 555–557 SI units, 20 prefixes, 20 typical quantities in machine design, 20 Size factor, 181–182, 378 Slenderness ratio for columns, 221 Smith diagram, mean stress, 186–188 Society of Automotive Engineers (SAE), 39, 40, 479, 765 Soderberg criterion, 185–186 Soldering, 702 Sommerfeld number, 627–628 Spacers, 501 Special stress conditions, Mohr’s circle biaxial tension and compression, 160 combined tension and shear, 161–162 cylinder with internal pressure, 162–164 pure shear, 161 uniaxial compression, 160 uniaxial tension, 159, 161 Specific modulus, 67 Specific strength, 67 Product design for manufacture and assembly, 9 Product realization process, 9 Properties of materials in mechanical design coefficient of thermal expansion, 39 creep, 36–37 density, 38 ductility elongation, 29 elastic limit, 28 electrical resistivity, 39 endurance strength, 36 fatigue strength, 36 flexural modulus, 30–31 flexural strength, 30–31 hardness, 31–34 impact energy, 35–36 machinability, 35 modulus of elasticity in shear, G, 29 in tension, E, 28–29 non-destructive measurement, 29–30 percent elongation, 29 Poisson’s ratio, v, 29 proportional limit, 28 relaxation, 37–38 shear strength, Sys and Sus, 29 tensile strength, Su, 28 thermal conductivity, 39 toughness, 35–36 wear, mechanical devices, 34 yield strength, Sy, 28 Proportional limit, 28 Pulleys flat belt, 516 V-belt, 244, 515–516. See also Sheaves Pure oscillation, 186 Pure pulsating stress, 186 pV factor, 619 Q Quality function deployment (QFD), 8 R Rack, 349–350 Radius of gyration, 218 Random loading, 172 Ratchet, 774 Relaxation, 37–38 Reliability factors, 180–181, 448, 449 Residual stress, 183 Resistivity, electrical, 39 Retaining ring grooves, 517 Retaining rings, 499, 500 Reyn, 627 Ringfeder Locking Assemblies , 483 Robust product design, 560 Rockwell hardness, 31 Rotational speed, 94–96 R.R. Moore fatigue test device, 169 S SAE numbering system alloy groups, 44 designation, 43–45 Sand blasters, 466 Screw threads, 14–16, 695, A–2 Seals, 502–505 bearings, 503, 504, 583–584 diaphragm, 502, 503 elastomers, 504Index 855 Strength endurance, 36 reduction factor, 129 shear, 29 tensile, 28 yield, 28 Stress allowable for gears, 374 amplitude, 168, 176 combined bending and torsion on circular shafts, 520, 521 combined stress, general, 144–145 concentration factors, 516–517, A–18 concentrations, 122–129 defined, 122, 123 factors, lug joints, 126–129 general guideline, for use, 124–126 keyseats, 516 in shaft design, 516–517 design, for shafts, 517–520 direct shear, 91 due to shrink or force fits, 555–557 elements, 92–93 fluctuating, 170–172 gear analysis, 374 high-cycle fatigue (HCF), 175–176 longitudinal, 162 low-cycle fatigue (LCF), 175–178 maximum shear, 146 normal, direct axial load, 93–94 principal, 145 ratio, 168–172 repeated and reversed, 169–170 special shear stress formulas, 103–104 static, 168–169 torsional shear, 96–98 transformation maximum and minimum principal stresses, 145 maximum shear stress, 146 principal stress element, angle, 145–146 three-dimensional, 146 vertical shearing stress, 102–103 Stress-life diagram, 176 Structural shapes, 16–18, A–15 angles, A–15–1 to A–15–3 channels, A–15–4 to A–15–8 I-shapes, A–15–9 to A–15–13 pipe, A–15–17 tubing mechanical, round, A–15–18, A–15–19 square and rectangular, A–15–14 to A–15–16 Structural steel, A–7 Superposition principle, 120–122 Surface finish, 180, 558, 560, 687 Synchronous belts, 251, 262–278 configurations for, 275–278 construction of, 264 kinematics of, 246 MDESIGN software for, 303 metric sizes, 262, 266 selection procedure, 266, 270–273 taperlock bushings, 264–265 T Taguchi method, 560 Taper and screw, 485, 486 Tapered roller bearings, 580–582 Taperlock bush, 264–265 Tempering, 47, A–3 to A–7 Tensile strength, 28 Tensile stress, 120 The engineering design process-embodiment design, 9 Specific weight, 38 Splines, 479–482 fits, 480–481 geometry, 479 involute, 480–482 modules, 482 pitches, 481–482 straight-sided, 479–481 torque capacity, 480 Split taper bushings, 499 Spreadsheets as design aids chain design, 291 columns, 226–227, 229, 232 force fits, stresses, 558 gear design, 409–412 shaft design, 533 springs, design, 673–677 Springs helical compression, 659–666 allowable stresses, 680 analysis, 667–670 buckling, 667 deflection, 666–667 design of, 670–677 end treatments, 659 materials, 663, 668 number of coils, 662 pitch, 662 pitch angle, 662–663 spring index, 662 spring rate, 662 stresses, 666–667 Wahl factor, 667 wire diameters, 659–660 helical extension, 677–681 allowable stresses, 663–666, 680 end configurations, 677–680 helical torsion, 681–687 deflection, 682 design procedure, 682–687 design stresses, 682 number of coils, 682 spring rate, 682 stresses, 682 types, 657–659 manufacturing, 687–688 shot peening, 687 Sprockets, chain, 262, 514–515 Stainless steel, A–6 Statical moment, 102 Static loading brittle materials, 174–175 ductile materials, 173–174 Statistical approaches to design, 203–204 Steel, 43–53 alloy groups, 45–46 bearing, 45, 569–570 carbon and alloy, 43–46, 390, 391, A–3 to A–7 carbon content, 45 carburized, 49, 391–392, A–5 conditions, 46–51 designation systems, 43–45 heat treating, 46–51 high-carbon, 45 low-carbon, 45 medium-carbon, 45 properties, heat-treated, A–3 to A–7 stainless, A–6 structural, A–7 uses for, 46 Stochastic methods, 203856 Index austempered ductile iron (ADI), 52 bronze, 60 CMNCs.(ceramic matrix nano composites), 76 gray iron (ADI), 52 malleable iron (ADI), 52 steel, 31 Weight, 21 Welded joints, 712–719 allowable stresses, 712, 714 geometry factors, 715 size of weld, 713–714, 716 treating weld as a line, 714 types of joints, 713 types of welds, 713 Wheel blasting, 466 White iron, 53 Wide flange beam shapes, 18–19, A–15–9 Wire ropes, 292–300 application of, 292 classification, 292–293 construction, 292–293, 298 design factors, 299–300 lay of, 294 material and grades, 297 nominal diameter, 292 properties of, 300 roller bearing, 296 selection of, 298–299 sheave and drum design, 295–297 strand construction, 293–295 tread diameter, 295 working loads, 299–300 Woodruff keys, 473, 475, 479 Wormgearing, 330–337, 456–464 coefficient of friction, 457, 458 efficiency, 458–460 face length of worm, 336 forces on, 456–460 friction force, 458 geometry, 332–337 input power, 458 lead, 333 lead angle, 333 output torque, 457 pitches, 332 pitch line speed, 456 power loss, 458 pressure angle, 335 reducer, 331, 332, 456 self-locking, 335, 460 shell worm, 335, 336 stresses, 461 surface durability, 461–464 threads (teeth), 332 tooth dimensions, 335 types, 330–332 velocity ratio, 334, 456 worm diameter, 335 wormgear dimensions, 335–336 Y Yield locus, 173 Yield point, 28 Yield strength, 28, 173–175, 185, 186, 188–190 Z Zinc, 58–59 die-cast alloys, A–10–1 Thermal conductivity, 39 Thermal expansion coefficient, 555 Three-stage industrial gear reducer, 456 Thrust bearings, 567–568 Titanium, 60, A–11–2 Titanium/nickel alloys, bearing material, 569 Tolerance, 546–560 geometric, 558, 559 grades, 548, 550 Torque, 94–96 equivalent, 161 tubes, 495, 497–499 Torsion in closed thin-walled tubes, 100 deformation, 98 in noncircular cross sections, 98–100 in open thin-walled tubes, 100–101 shear stress formula, 97–98 stress distribution, 97 Torsional deformation, 98 Torsional shear, 96 stress formula, 97–98 Total design, 9 Toughness, 35–36 Train value, 345–346 Transition fits, 555 Transmission, design of, 590–611 Tresca criterion, 164 TRIZ (Theory of Inventive Problem Solving), 8–9 Tubes, stresses in, 100–101, 103 U Undercutting of gear teeth, 322 Unified numbering system, UNS, 39–40 Unimegagear , 465 Unit systems, 20–21 Universal joints, 494–499 U.S. customary units, 20 typical quantities in machine design, 20 V V-belt drives, 252–262 angle of contact, 253 angle of wrap correction factor, 259 belt construction, 252 belt cross sections, 253 belt lengths correction factor, 259 formula, 257 standard, 260 belt tension, 262 center distance formula, 261 design of, 253–262 forces on shafts, 515–516 kinematics of, 246 metric sizes, belt cross section, 253 power rating charts, 257, 258 pulleys. See Sheaves SAE standards, 286 service factors, 256 sheaves, 251–255 span length, 253 Velocity ratio, gears, 334 gear trains, 343–344 Viscosity, 627 Viscosity index (VI), 637 von Mises criterion, 164 W Wear, 638 Wear resistance
كلمة سر فك الضغط : books-world.net The Unzip Password : books-world.net أتمنى أن تستفيدوا من محتوى الموضوع وأن ينال إعجابكم رابط من موقع عالم الكتب لتنزيل كتاب Machine Elements in Mechanical Design - Sixth Edition رابط مباشر لتنزيل كتاب Machine Elements in Mechanical Design - Sixth Edition 
|
|