rambomenaa كبير مهندسين


عدد المساهمات : 2041 التقييم : 3379 تاريخ التسجيل : 21/01/2012 العمر : 46 الدولة : مصر العمل : مدير الصيانة بشركة تصنيع ورق الجامعة : حلوان
 | موضوع: كتاب Welding Handbook - Volume 1 الإثنين 29 أكتوبر 2012, 8:51 pm | |
| 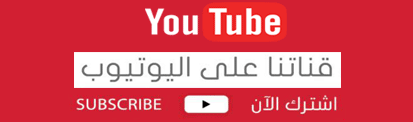
أخوانى فى الله أحضرت لكم كتاب Welding Handbook Ninth Edition Volume 1 Welding Science and Technology Prepared Under the Direction of the Welding Handbook Committee Cynthia L. Jenney Annette O’Brien Editors
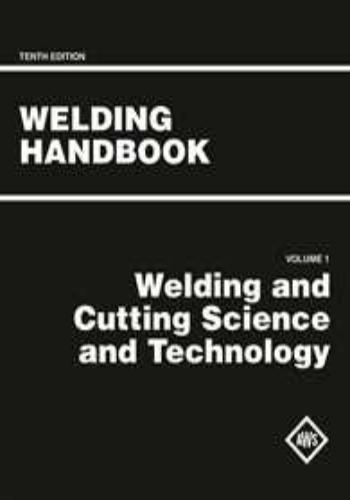 و المحتوى كما يلي :
CONTENTS PREFACE . xi ACKNOWLEGEMENTS xii CONTRIBUTORS . xiii CHAPTER 1-SURVEY OF JOINING, CUTTING, AND ALLIED PROCESSES . 1 Introduction 2 Joining Processes . 3 Cutting Processes . 42 Thermal Spraying 47 Conclusion 49 Bibliography 49 CHAPTER 2-PHYSICS OF WELDING AND CUTTING 51 Introduction 52 Fusion and Solid-State Welding . 52 Energy Sources for Welding . 57 Arc Characteristics 67 Metal Transfer . 73 Melting Rates 78 Physical Properties of Metals and Shielding Gases . 81 Conclusion 84 Bibliography 84 CHAPTER 3-HEAT FLOW IN WELDING . 87 Introduction 88 Heat Flow Fundamentals . 88 Quantitative Calculation of Heat Transfer in Fusion Welding . 95 Conduction of Heat during Fusion Welding 97 Convective Heat Transfer in the Weld Pool . 105 Relative Importance of Conduction and Convection . 108 Conclusion 111 Bibliography 112 CHAPTER 4-WELDING METALLURGY 115 Introduction 116 Physical Metallurgy . 116 Metallurgy of Welding . 130 Weldability of Commercial Alloys . 140 Corrosion in Weldments 149 The Brazed or Soldered Joint . 151 Corrosion in Brazed and Soldered Joints . 154 Conclusion 154 Bibliography 155 CHAPTER 5-DESIGN FOR WELDING . 157 Introduction 158 Properties of Metals 158 Weldment Design Program 166 Welded Design Considerations . 170viii Design of Welded Joints .182 Selection of Weld Type .193 Sizing of Steel Welds .196 Tubular Connections 216 Aluminum Structures .226 Conclusion .236 Bibliography .237 CHAPTER 6-TEST METHODS FOR EVALUATING WELDED JOINTS 239 Introduction .240 Testing for Strength 241 Hardness Tests .256 Bend Tests 260 Fracture Toughness Testing 261 Fatigue Testing .272 Corrosion Testing .277 Creep and Rupture Testing .280 Testing of Thermal Spray Applications .281 Weldability Testing .284 Conclusion .292 Bibliography .292 CHAPTER 7-RESIDUAL STRESS AND DISTORTION .297 Introduction .298 Fundamentals .298 Nature and Causes of Residual Stress .300 Effects of Residual Stress 308 Measurement of Residual Stress .313 Residual Stress Distribution Patterns 318 Effects of Specimen Size and Weight .322 Effects of Welding Sequence .325 Residual Stress in Welds Made with Different Welding Processes .326 Weld Distortion 328 Reducing or Controlling Residual Stress and Distortion .351 Conclusion .354 Bibliography .354 CHAPTER 8-SYMBOLS FOR JOINING AND INSPECTION .359 Introduction .360 Fundamentals .361 Welding Symbols 361 Welding Symbols for Specific Weld Types .373 Brazing Symbols .381 Soldering Symbols 382 Inspection Symbols .385 Conclusion .393 Bibliography .393 CHAPTER 9-WELDMENT TOOLING AND POSITIONING 395 Introduction .396 Fixtures 396ix Positioners . 403 Conclusion 419 Bibliography 419 CHAPTER 10-MONITORING AND CONTROL OF WELDING AND JOINING PROCESSES 421 Introduction 422 Principles of Monitoring and Control 422 Sensing Devices . 423 Process Instrumentation 428 Process Monitoring Systems 429 Process Control Systems 429 Monitoring and Control Systems . 431 Conclusion 448 Bibliography 448 CHAPTER 11-MECHANIZED, AUTOMATED, AND ROBOTIC WELDING 451 Introduction 452 Mechanized Welding . 453 Automated Welding . 458 Robotic Welding 467 Planning for Automated and Robotic Welding 474 Conclusion 482 Bibliography 482 CHAPTER 12-ECONOMICS OF WELDING AND CUTTING . 483 Introduction 484 The Cost Estimate . 484 Economics of Welding . 485 Automated and Robotic Systems . 498 Economics of Resistance Spot Welding 510 Capital Investment in Welding Automation and Robotics . 514 Control of Welding Costs 517 Economics of Brazing and Soldering 523 Economics of Thermal Cutting 530 Conclusion 531 Bibliography 531 CHAPTER 13-WELD QUALITY 533 Introduction 534 Defining Weld Quality . 534 Overview of Weld Discontinuities 536 Discontinuities Associated with Fusion Welding 538 Discontinuities Associated with Resistance Welding 562 Discontinuities Associated with the Solid-State Welding Processes . 567 Discontinuities in Brazed and Soldered Joints 569 Significance of Weld Discontinuities 572 Conclusion 575 Bibliography 576x CHAPTER 14-WELDING INSPECTION AND NONDESTRUCTIVE EXAMINATION .579 Introduction .580 Personnel Qualifications .581 The Inspection Plan 583 Nondestructive Examination 584 Metallographic Examination Methods .633 Inspection of Brazed and Soldered Joints 634 Conclusion .634 Bibliography .634 CHAPTER 15-QUALIFICATION AND CERTIFICATION 637 Introduction .638 Welding and Brazing Procedure Specifications 640 Qualification of Welding and Brazing Procedures .655 Performance Qualification 668 Standardization of Qualification Requirements 678 Conclusion .679 Bibliography .679 CHAPTER 16-CODES AND OTHER STANDARDS .683 Introduction .684 Standards-Developing Organizations and Welding-Related Publications 685 Guidelines for Participating in International Standards Activities .708 Conclusion .708 CHAPTER 17-SAFE PRACTICES .711 Introduction .712 Safety Management 712 Protection of the Work Area 714 Personal Protective Equipment .719 Protection against Fumes and Gases .724 Safe Handling of Compressed Gases 733 Protection against Electromagnetic Radiation 738 Electrical Safety 738 Fire Prevention .741 Explosion Prevention 743 Process-Specific Safety Considerations 743 Safety in Robotic Operations .753 Conclusion .754 Bibliography .754 APPENDIX A-TERMS AND DEFINITIONS .759 APPENDIX B-METRIC PRACTICE GUIDE FOR THE WELDING INDUSTRY 849 INDEX OF MAJOR SUBJECTS: Eighth Edition and Ninth Edition, Volume 1 .873 Types of Regulatory Documents .684 INDEX OF NINTH EDITION, Volume 1 . This page has been reformatted by Knovel to provide easier navigation. INDEX Index Terms Links A AA. See Aluminum Association. AAR. See Association of American Railroads. AASHTO. See American Association of State Highway and Transportation Officials. ABS. See American Bureau of Shipping. ACGIH. See American Conference of Governmental Industrial Hygienists. Acoustic emission testing 628 accumulation of data 629 acoustic sources, position of 629 applications 628 description 628 equipment 629 evaluation of data 629 limitations 630 monitoring during proof testing 629 monitoring during welding 629 monitoring time, postweld 629 procedures 629 standards for, ASTM and ASME 629 test results, recording of 630 Adaptive control, definition of 430 Adaptive control welding 452 467 Adherends 34 Adhesive bonding 34 752 advantages 34 description of 34 limitations of 34Index Terms Links This page has been reformatted by Knovel to provide easier navigation. Adhesive bonding (Cont.) safe practices 752 Aerospace Material Specifications 705 Air carbon arc cutting (CAC-A) 43 45 AISC. See American Institute of Steel Construction. Allowable stress design (ASD) 196 Alloys 117 aluminum 143 230 cobalt 145 copper 144 magnesium 144 multiphase 118 228 nickel-based 144 precipitation-hardened 137 steels 142 titanium 145 transformation-hardening 138 Aluminum Association (AA) 226 708 Aluminum structures, design of 226 aluminum alloys, welded, tensile strength of 230 butt joints 228 concepts and methods 227 designing for welding 227 fatigue strength 234 fatigue stress ratio 235 fillet weld shear strength 233 fillet weld size, minimum 233 heat-affected zone, effect of 230 joint design 229 lap joints 228 mechanical properties 230 residual stresses in 235 service temperature, effect of 236Index Terms Links This page has been reformatted by Knovel to provide easier navigation. Aluminum structures, design of (Cont.) service temperature, loss of strength at 236 sniping 233 stress distribution 233 thermal treatments 233 236 T-joints 229 weld joint design 227 weld joint types 227 welding effects on strength 230 American Association of State Highway and Transportation Officials (AASHTO) 203 685 publications 686 American Bureau of Shipping (ABS) 685 publications 687 American Conference of Governmental Industrial Hygienists (ACGIH) 724 732 American Institute of Steel Construction (AISC) 203 685 687 American Iron and Steel Institute (AISI) 708 publications 687 American National Standards Institute (ANSI) 687 international standards 668 U.S. national standards 687 American Petroleum Institute (API) 685 688 publications 688 American Railway Engineering and Maintenance-of-Way Association (AREMA) 203 685 688 publications 689 American Society for Testing and Materials (ASTM) 538 606 685 676 690 publications 691 American Society of Mechanical Engineers International (ASME) 575 606 630 638 642 651 669 670 673 679 685 689 698Index Terms Links This page has been reformatted by Knovel to provide easier navigation. American Society of Mechanical Engineers (Cont.) publications 689 American Society for Nondestructive Testing (ASNT) 538 581 676 690 publications 690 American Society for Quality (ASQ) 691 American Water Works Association (AWWA) 685 692 publications 692 American Welding Society (AWS) 692 filler metal specifications 694 publications 692 qualification and certification programs 638 qualification standards 695 reference publications 692 safety and health standards 695 standard definitions 692 standard symbols 692 structural welding codes 694 testing standards 695 thermal spraying standards 693 welding application standards 693 welding inspector qualification and certification program 581 678 welding process standard 693 AMS. See Aerospace Material Specifications. ANSI. See American National Standards Institute. API. See American Petroleum Institute. Arc blow 72 Arc characteristics 67 arc blow 71 72 arc plasma 67 arc radiation 69 anode fall space 70 anode spot 70Index Terms Links This page has been reformatted by Knovel to provide easier navigation. Arc characteristics (Cont.) cathode fall space 70 cathode spot 70 electrical features 70 Elenbass-Heller energy balance 69 impedance, arc 70 magnetic fields, influence of 71 thermal equilibrium 68 Arc efficiency 54 89 Arc spraying (ASP) 47 48 See also Thermal spraying. Arc strike 544 Arc stud welding (SW) 16 advantages 17 capacitor discharge welding 17 description of 16 discontinuities associated with 537 equipment 16 ferrule composition 16 limitations 18 manual arc welding of studs 16 power sources for 17 skill requirements, operator 17 Arc voltage control, welding 432 Arc welding 3 See also Arc stud welding; Electrogas welding; Flux cored arc welding; Gas metal arc welding; Gas tungsten arc welding; Shielded metal arc welding; Submerged arc welding; and Plasma arc welding. automated 461 cost definitions 500 deposition of heat in 95Index Terms Links This page has been reformatted by Knovel to provide easier navigation. Arc welding (Cont.) description of 3 equations used to estimate direct costs of 499 energy absorption efficiency in 89 estimating the direct costs of 498 monitoring and control of 431 robotic systems 467 safe practices 720 745 procedure specifications 641 AREMA. See American Railway Engineering and Maintenance-of-Way Association. ASME. See American Society of Mechanical Engineers. ASNT. See American Society for Nondestructive Testing. ASQ. See American Society for Quality. ASP. See Arc Spraying. ASTM. See American Society Testing and Materials. Association of American Railroads (AAR) 686 publications 656 Austenite decomposition products 122 bainite 124 cementite (iron carbide) 122 ferrite 122 isothermal transformation diagram 124 martensite 124 pearlite 123 transformation diagrams, continuous cooling 125 transformation diagrams, time-temperature 124 Automated and robotic systems, economics of 498 cycle-time estimation 501 formulas 501 general formulas, sequential welding centers 501 505 general formulas, simultaneous welding centers 503 machine chart, operators 502Index Terms Links This page has been reformatted by Knovel to provide easier navigation. Automated and robotic systems, economics of (Cont.) methodology used in 500 multiple operators, multiple machine system 502 504 506 multiple operators, multiple welding center system 507 multiple operators, single machine system 504 506 multiple welding centers 501 507 sequential welding centers 501 505 simultaneous welding centers 501 502 single operator, multiple welding center system 503 505 507 single operator, single machine system 502 505 welding center configurations 501 welding manufacturing systems, types of 498 Automated and robotic welding, planning for 474 atmospheric contamination 479 changeover time and inventories 480 environment 479 equipment location 479 ergonomics, safety, and health 479 facilities 477 fixturing 459 476 floor space 480 integration, automated or robotic system 480 investment 480 maintenance 479 480 manufacturing feasibility studies 476 motion operation 460 operator, training and education 476 479 personnel requirements 480 procedures and scheduling 475 process selection and WPS qualification 476 procurement scheduling 477 product design 475 production volume 475Index Terms Links This page has been reformatted by Knovel to provide easier navigation. Automated and robotic welding (Cont.) quality control 477 selection of welding equipment 476 training requirements, recommended 479 weld development and testing program 476 welding standards 476 workpiece tolerances 461 475 Automated arc welding 461 475 See also Automated welding; Robotic arc welding systems. feeding devices 463 power sources 462 seam-tracking systems 462 system components 462 system controller 462 welding interface 462 welding schedules 462 welding torches 462 Automated welding 458 See also Automated arc welding; Robotic arc welding systems. advantages of 460 automated arc welding 461 conversion to 476 definition of 452 fundamentals 459 limitations 461 resistance welding automation 463 robotic arc welding 467 robotic resistance welding 473 robotic welding 467 Automation 458 application 459Index Terms Links This page has been reformatted by Knovel to provide easier navigation. Automation (Cont.) definition of 458 fixturing and tooling 459 468 integration of 477 fundamentals of 474 justification for automatic equipment 459 manufacturing considerations 459 Automation, arc welding 461 See also Automation; Automated welding. equipment 462 seam tracking systems 462 Automation, resistance welding 463 See also Automation; Automated welding. ancillary equipment 466 applications 463 controls 465 description of 463 input/output communication 466 interface between components 466 microcomputer controls 465 monitoring devices 466 monitoring equipment 466 production rates 464 quality control 467 spot welding guns 465 spot welding machines 465 welding cycle 464 465 welding electrodes 465 welding system components 465 Automation, welding. See also Automated welding; Automation; Automation, arc welding; Automation, resistance welding. fixturing 459Index Terms Links This page has been reformatted by Knovel to provide easier navigation. Automation, welding (Cont.) flexibility 475 process variables 480 production considerations 475 safety and health 479 safety standards for 479 Automotive welding standards 705 AWS. See American Welding Society. AWWA. See American Water Works Association. B Backing left on 544 Bainite 124 Base metal 140 642 cracking of 550 Bend tests 260 description of 260 fixtures for 260 guided bend test 260 longitudinal bend tests 260 qualification by 260 test specimens for 260 transverse bend tests 261 Beryllium 149 Brazed and soldered joints, corrosion in 154 stress-corrosion cracking 154 stress-corrosion cracking, procedures to reduce 154 stresses, cold-forming 154 Braze welding (BW) 42 applications 42 description of 42 Brazed or soldered joint, the 151 advantages 151 alloys, brazing and soldering 153Index Terms Links This page has been reformatted by Knovel to provide easier navigation. Brazed or soldered joint, the (Cont.) beryllium 153 brazing filler metals 151 153 cadmium-silver alloy solder 154 cadmium-zinc alloy solder 154 contaminants 152 disadvantages 151 intergranular penetration of 153 intermetallic compound formation 152 153 intrusion in 153 metallurgical considerations 151 molybdenum and tungsten, brazing of 153 niobium, brazing of 153 operations 151 process variations 152 properties of 152 soldering alloys 153 tantalum, brazing of 153 154 tin-copper-silver alloy solder 154 tin-lead alloy solder 154 tin-silver alloy solder 154 wetting of base metal 152 Brazing 37 See also Brazing symbols; Joining Process(es); Soldering. description of 37 Brazing and soldering 34 advantages 36 discontinuities associated with 569 similarities of 35 Brazing procedure specifications (BPS) 660 Brazing symbols 381 See also Welding symbols.Index Terms Links This page has been reformatted by Knovel to provide easier navigation. Brazing symbols (Cont.) brazed joints 381 letter designations for 381 Brinell hardness test 256 British Standards Institute (BSI) 575 Brittle failures 163 BSI. See British Standards Institute. Buckling 173 Burn-through 544 BW. See Braze welding. C CAC-A. See Air carbon arc cutting. Canadian Standards Association International (CSA) 581 695 publications 696 Capital investment, justification of 514 automated and robotic systems, advantages of 516 combined operations 516 cost benefit factors 514 cost forecast factors 514 deposition efficiency, improved 516 improved throughput 517 improvement factor, overall 516 installation costs 515 material handling 515 manufacturing, agile 516 manufacturing options 516 operation factors, improved 516 production volume estimates 514 safety 515 special requirements 514 weld joint design, efficient 516 workpiece accuracy 515 workpiece geometry 515Index Terms Links This page has been reformatted by Knovel to provide easier navigation. Carbon arc welding (CAW) 537 Cascade soldering (CS) 41 CAW. See Carbon arc welding. Center of gravity 405 411 CEN. See European Committee for Standardization. CGA. See Compressed Gas Association. Charpy V-notch impact test 263 Cobalt alloys 145 Codes. See Codes and Other Standards; Standards. Codes and other standards 684 definition of terms 684 guidelines for participating in national standards 708 standards-developing organizations and welding-related publications 685 supplementary reading list 709 types of regulatory documents 684 Cold welding (CW) 27 357 Cold working 121 619 Columbium 147 Compressed Gas Association (CGA) 696 733 735 publications 696 Compressed gas cylinders 733 See also Compressed gases, handling of. cylinder safety device 737 filling cylinders and mixing gases 733 gas withdrawal 734 labeling 733 pressure-relief devices 734 securing 733 storage 733 734 storage precautions 733 usage 733 valve protection cap 734 valves, cylinder 734Index Terms Links This page has been reformatted by Knovel to provide easier navigation. Compressed gases, safe handling of 733 See also Compressed gas cylinders. flowmeter(s) 735 fuel gases 735 manifolds 734 735 oxygen 735 piping systems 735 regulators 735 storage and usage 733 regulator(s), pressure-reducing 735 regulator adaptors 735 Concavity 540 544 Conductance and convection, relative importance of 108 cooling rates 110 solidification structure, simple features of 110 variable penetration 109 Consumable guide electroslag welding (ESW-CG) 34 35 advantages 34 applications 34 description of 34 electrodes 34 Continuous cooling transformation diagrams 125 Convexity 540 544 Copper alloys 44 Corner joints 195 Corrosion fatigue 277 Corrosion properties 168 See also Corrosion resistance; Corrosion testing of welded joints. Corrosion resistance 166 Corrosion testing of welded joints 277 factors influencing 277 general corrosion 279Index Terms Links This page has been reformatted by Knovel to provide easier navigation. Corrosion testing of welded joints (Cont.) preferential corrosion 277 279 salt spray testing 279 surface preparation 278 test methods 278 visual inspection of specimens 278 279 weight-loss test 279 Cost control, welding 517 consumable electrodes, advantages of 519 eliminating operations 520 field welding 521 joint design 517 manageable costs 517 manufacturing, guides for 521 mistake-proofing 518 overwelding 522 process selection 518 production planning, guidelines for 520 quality costs, hidden 521 quality factors 521 supporting activities 521 unforeseen costs 521 weldment design 517 welding procedures 492 521 Cost estimating, welding 485 deposited metal weights 486 492 deposition efficiency 492 549 deposition rate 492 gas 492 labor 495 miscellaneous workplace time, definition of 495 operator factor, the 495 standards preparation 497Index Terms Links This page has been reformatted by Knovel to provide easier navigation. Cost estimating, welding (Cont.) typical variables used 485 welding procedure specification (WPS), use of 485 Cracking 544 base metal 549 550 causes and remedies 551 factors affecting 549 hydrogen-induced 550 in solid-state welds 568 measurement of residual stress by 318 resistance to 549 stress corrosion 313 under hostile conditions 313 weld metal 549 Cracks 544 600 base metal 549 causes and remedies 549 550 cold cracking 550 crater 546 547 delayed 550 face 546 547 heat-affected zone (HAZ) 546 hydrogen effects 550 in brazed and soldered joints 571 indications of 600 longitudinal 545 546 547 root 547 548 root surface 547 548 throat 547 548 toe 547 548 transverse 545 547 548 underbead 547 550 weld interface 547Index Terms Links This page has been reformatted by Knovel to provide easier navigation. Cracks (Cont.) weld metal 547 548 549 Creep, definition of 165 Creep rate(s) 165 Creep-rupture of metals 165 Creep and rupture testing 280 Cryogenic cylinders and tanks 737 Cryogenic liquids 737 Cryogenic piping systems 735 CS. See Cascade soldering. CSA. See Canadian Standards Association. Cutting processes 42 See also Thermal cutting; Oxyfuel gas cutting; Plasma arc cutting; Air carbon arc cutting; Laser beam cutting; Water jet cutting. CW. See Cold welding. Cyclic loading 164 D DB. See Dip brazing. Delamination 540 559 Depth of fusion, definition of 564 Design for welding 158 aluminum structures 226 bibliography 237 considerations 170 equations 171 introductory overview 158 major factors 167 objectives 158 selection of weld type 193 sizing of steel welds 196 supplementary reading list 237Index Terms Links This page has been reformatted by Knovel to provide easier navigation. Design for welding (Cont.) tubular connections 216 welded joints 182 Destructive tests. See Inspection plan; Nondestructive examination; Proof testing; Spot welds, tests of. macroscopic examination 633 metallographic examination 633 microscopic examination 634 Detonation flame spraying (DFSP) 48 DFSP. See Detonation flame spraying. DFW. See Diffusion welding. Diffusion brazing 39 Diffusion welding (DFW) 25 57 65 description of 25 discontinuities associated with 537 energy sources 65 equipment 25 mechanisms for 65 Dip brazing (DB) 39 Dip soldering (DS) 41 Direct drive friction welding 24 Discontinuities, brazed and soldered joints 569 acceptance limits 569 base metal erosion 571 cracks 571 discontinuities, common 569 discontinuous fillets 571 flux entrapment 571 lack of fill 570 surface appearance, unsatisfactory 571 Discontinuities, fusion welds 538 599 arc craters 539 arc strike 539 544Index Terms Links This page has been reformatted by Knovel to provide easier navigation. Discontinuities, fusion welds (Cont.) backing left on 539 544 base metal 558 burn-through 539 544 causes and remedies 549 characteristics of 538 classification of 538 concavity 539 540 544 convexity 539 540 544 cracks 539 540 544 600 crater crack 540 546 definition of 539 delamination 540 559 design-related 539 discontinuity indications, relevant 607 dimensional discrepancies 559 distortion 559 560 face 546 flux inclusions 551 geometric factors 552 heat-affected-zone cracks 546 551 hydrogen, effect of 555 inclusions, slag and tungsten 540 550 559 incomplete joint penetration 540 553 600 624 incomplete fusion 539 540 552 600 624 incorrect joint preparation 559 lamellar tear 539 559 laminar discontinuities 627 laminations 558 laps and seams 559 location and occurrence of 539 longitudinal 546 melt-through 539 544Index Terms Links This page has been reformatted by Knovel to provide easier navigation. Discontinuities, fusion welds (Cont.) metallurgical 538 overlap 539 554 overview of 536 oxide film 539 555 oxide inclusions 552 porosity 539 540 555 599 porosity, aligned 539 540 555 porosity, causes of 555 porosity, cluster 539 540 555 porosity, elongated 539 540 555 porosity, piping 539 540 555 porosity, scattered 539 540 555 procedure and process related 538 root 548 root surface 548 slag, entrapped 552 slag inclusions 552 spatter 539 556 surface irregularities 556 terms, definition of 580 throat 548 toe 548 transverse 548 tungsten inclusions 550 underbead 546 undercut 540 557 600 underfill 540 558 661 weld joint mismatch 539 560 weld joint properties, inadequate 561 weld metal 548 551 weld profile 560 weld reinforcement, excessive 550 weld size, incorrect 560Index Terms Links This page has been reformatted by Knovel to provide easier navigation. Discontinuities, resistance welds 562 common 562 depth of fusion 564 discontinuities, internal 565 ductility, incorrect 564 expulsion 566 incomplete joint penetration 564 incorrect strength 564 sheet separation, excessive 566 surface appearance, undesirable 562 weld quality indicators 562 weld quality, maintaining consistent 566 weld size, incorrect 563 welding procedure specifications (WPS), factors addressed 566 Discontinuities, solid state welds 567 cracking 568 decarbonization 569 fibrous metallurgical structures 569 flat spots 569 oxidation, intergranular 568 solid state weld discontinuities, common 567 upset, insufficient 567 void, inclusions, in welds 569 weld joint mismatch 567 Dissimilar metal welds 166 Distortion, control of 299 351 assembly procedure 352 correction of 353 design factors 352 elastic prestraining 353 mechanical straightening 354 preheating 353 thermal methods 351Index Terms Links This page has been reformatted by Knovel to provide easier navigation. Distortion, steel vs. aluminum 350 longitudinal bending 347 angular change, fillet welds 350 transverse shrinkage, butt joints 350 longitudinal distortion 350 Distortion, weld 298 328 angular change and distortion, relationship of 340 angular change, butt joints 337 angular change, fillet weld 339 angular distortion, aluminum vs. steel fillet welds 343 angular distortion, butt joints 343 353 angular distortion, fillet welds 339 angular distortion, minimization of 337 bending distortion, induced longitudinal shrinkage 343 bibliography 354 buckling distortion 347 butt joint, longitudinal shrinkage 337 butt joints 337 butt joints, transverse shrinkage in 328 fillet welds 336 339 fillet welds, transverse shrinkage in 336 fundamental dimensional changes 328 joint restraint 330 longitudinal shrinkage 337 multipass welding 332 residual stress, reduction of 300 supplementary reading list 356 transverse shrinkage 328 350 wavy 339 Distortion in butt joints 328 longitudinal shrinkage 337 longitudinal shrinkage, estimation of 337 procedure variables, effect on shrinkage 333Index Terms Links This page has been reformatted by Knovel to provide easier navigation. Distortion in butt joints (Cont.) restraint, effect on transverse shrinkage 330 rotational distortion 330 transverse shrinkage 328 transverse shrinkage, effect of heat input on 336 transverse shrinkage, factors affecting 329 DOD. See U.S. Department of Defense. DOE. See U.S. Department of Energy. DOT. See U.S. Department of Transportation. DS. See dip soldering. E EBW. See Electron beam welding. Economics of brazing and soldering 524 assembly and fixturing 526 brazing costs, estimating and controlling 525 chemical compositions 525 526 cost control, steps in establishing solder 526 joint clearances 525 526 joint design 525 labor costs, soldering 526 material costs, soldering 526 precleaning and surface preparation 526 service requirements 526 soldering costs, estimating and controlling 526 type of joint 525 variables affecting costs, typical 525 Economics of resistance spot welding (RSW) 510 air cost, estimating 513 consumables costs, welding machine 512 cooling water costs, estimation of 513 cost model 510 cycle time, definition of 571 electrode replacement costs, calculation of 513Index Terms Links This page has been reformatted by Knovel to provide easier navigation. Economics of resistance spot welding (RSW) (Cont.) manufacturing costs, factors involved in 510 overhead ratio 510 power costs, estimating 513 spot welding machine cycle time, estimating 511 total spot welding time calculation 514 total wear costs 513 Economics of thermal cutting 530 capital costs 530 controlling costs 530 cutting processes 530 estimating costs 530 implementing plan 530 Economics of welding 485 bill of materials 486 estimating direct costs 498 estimating labor hours 496 filler metal deposition rate 492 labor costs, direct 485 495 manufacturing costs 485 materials estimates 486 operator factor 496 overhead, factory 498 standards development 497 supplemental requirements for consumables 492 Economics of welding and cutting 484 bibliography 531 capital investment, automation and robotics 514 control of welding costs 517 cost estimate, the 484 estimating cycle time 501 general overview 484 supplementary reading list 531Index Terms Links This page has been reformatted by Knovel to provide easier navigation. Eddy current examination 625 advantages 627 applications 626 coils 626 coils, electromagnetic properties of 626 coils, impedance 626 cracks, effect of 625 626 depth of penetration 627 description 625 eddy currents, properties of 626 limitations 627 skin effects 626 theory 625 Edison Welding Institute (EWI) 679 Effective throat 195 201 EGW. See Electrogas welding. Electric resistance welding 21 See also Upset welding. Electrical conductivity 166 Electrical safety 738 electric shock 738 741 equipment, modification and maintenance 738 equipment selection 739 grounding, work lead vs. grounding lead 739 operations, safe 740 modification procedures, equipment 741 multiple arc operations 741 sources of electric shock 738 special precautions, pacemaker wearers 741 training program 738 welding operations 739 740 Electrogas welding (EGW) 13 applications 14Index Terms Links This page has been reformatted by Knovel to provide easier navigation. Electrogas welding (EGW) (Cont.) deposition rates 14 description of 13 electrodes 13 equipment 13 Electromagnetic examination 624 See also Eddy current examination. advantages 627 calibration standards 625 eddy current examination 625 description 624 limitations 627 procedures 624 quality standards 625 theory of 624 variables, metallurgical 624 variables, physical 624 Electron beam welding (EBW) 29 absorption efficiency in 93 advantages 30 description of 29 discontinuities associated with 537 efficiency 31 93 equipment 29 limitations 30 monitoring and control systems 442 process variations 30 safe practices 747 33 Electroslag welding (ESW) 33 advantages 33 applications 33 consumable guide method 34 deposition rates 33Index Terms Links This page has been reformatted by Knovel to provide easier navigation. Electroslag welding (ESW) (Cont.) description of 33 discontinuities associated with 537 electrodes for 33 equipment 33 Elevated-temperature tests 280 See also Creep testing; Creep-rupture testing. creep data 280 creep-rupture phenomena 280 creep-rupture properties 280 creep-rupture testing 280 defining creep-rupture properties 280 Larson-Miller parameter 281 metallurgical reactions during creep tests 280 parameters for creep-rupture testing 281 preparation of test specimens 280 primary creep 280 stages of creep 280 stress-rupture curves 280 test machines 280 test methods 280 test specimens 280 time-temperature phenomenon 280 types of tests 280 Energy input 53 Energy sources for welding 57 arc welding, for 58 chemical sources 60 electrical sources 57 electroslag welding, for 60 mechanical sources 63 oxyfuel gas welding, for 60 resistance welding, for 58 thermite welding 61Index Terms Links This page has been reformatted by Knovel to provide easier navigation. ERW. See Electric resistance welding. ESW. See Electroslag welding. ESW-CG. See Consumable guide electroslag welding. European Committee for Standardization (CEN) 697 700 Explosion welding (EXW) 26 description of 27 discontinuities associated with 537 energy sources, mechanical 64 safe practices 749 EWI. See Edison Welding Institute (EWI). Excessive sheet separation, definition of 566 EXW. See Explosion welding. F Fatigue failure 162 Fatigue fractures 203 Fatigue life 162 Fatigue strength of aluminum structures 234 Fatigue testing 272 corrosion fatigue 277 cover plates, effect of 274 crack growth rate 272 273 277 definition of 272 fatigue crack 272 fatigue life 272 fatigue variables 273 fundamentals 272 Paris law 273 progressive failure 272 rate of crack growth 274 specimen geometry, effect of 275 stress range, effect of 273 277 surface conditions, effect of 275 surface discontinuities, effect of 275Index Terms Links This page has been reformatted by Knovel to provide easier navigation. Fatigue testing (Cont.) test methods 276 weld reinforcement, effect of 275 weld soundness, effect of 275 welded versus rolled beams, fatigue life of 273 FCAW. See Flux cored arc welding. Federal standards 699 Filler metal specifications 705 Fillet weld(s) 191 Fillet weld(s), skewed 191 Fillet weld applications 191 Fillet welds, single 191 Fillet weld size 191 Fillet weld strength 191 Fillet welds, double 191 Fire prevention and protection 741 Fire prevention, clothing 730 Fitness for service 575 fracture mechanics, linear elastic 575 published standards 575 Fixtures 396 476 applications 399 arrangement, three-piece 403 arrangement, two-piece 402 applications 401 basic design requirements 397 benefits 396 clamping and holding systems 398 clamping device factors 396 definition of 396 design and manufacture 396 design, electrical 397 design requirements 397Index Terms Links This page has been reformatted by Knovel to provide easier navigation. Fixtures (Cont.) holding fixtures 401 precision 401 production 397 purposes 396 robotic welding 401 safety considerations 397 seam welding 400 standard components for 397 tacking 399 400 tooling, modular 398 Flame spraying (FLSP) 47 See also Thermal spraying. Flash welding (FW) 20 537 applications 20 description of 20 Fluorescent penetrant testing. See Liquid penetrant examination. Flux cored arc welding (FCAW) 13 applications 13 deposition efficiency 13 deposition rates 13 description of 13 discontinuities associated with 537 electrode extension 13 electrodes 13 electrode flux 13 equipment 13 gas-shielded (FCAW-G) 13 metal transfer 78 self-shielded (FCAW-S) 13 Focused heat sources 62 electron beam welding, for 63 laser beam welding, for 62Index Terms Links This page has been reformatted by Knovel to provide easier navigation. Forge welding (FOW) 22 537 Forming of parts 167 FOW. See Forge welding. Fracture mechanics 164 262 572 574 Fracture mechanics evaluation of discontinuities 575 fitness for service 575 published standard 575 Fracture toughness 163 261 Fracture toughness testing 261 See also Fracture toughness tests, plainstrain; Charpy V-notch impact test. ASTM specifications for 263 266 Charpy-V-notch tests 263 crack arrest tests 263 crack tip opening displacement (CTOD) 267 definition of 261 drop-weight-nil-ductility temperature 263 268 ductile-to-brittle transition temperature (DBTT) 263 dynamic tear tests 266 270 elastic-plastic fracture mechanic (EPFM) toughness 267 268 fracture toughness tests 266 fundamentals 262 linear-elastic fracture mechanics (LEFM) 266 special problems 270 test methods for 262 263 test sequence 266 test specimens 268 Fracture toughness tests, plain-strain 266 definition of 261 special problems 270 specimen dimensions 263 266 temperature effects 265 test method 266Index Terms Links This page has been reformatted by Knovel to provide easier navigation. Friction welding (FRW) 22 direct drive 24 discontinuities associated with 537 energy sources, mechanical 23 63 equipment 23 inertia 24 monitoring and control of 445 process variations 24 safe practices 749 stir welding 24 stud welding 24 FRW. See Friction welding. Fumes and gases 724 See also Safe practices; Ventilation. arc voltage (length), effects of 726 arc welding 725 brazing and soldering 750 consumables, effects of 727 electron beam welding (EBW) 748 exposure factors 724 fume removal equipment, gun-mounted 279 gases generated 725 gases in confined spaces 730 generation rate factors 726 laser beam operations 749 low-allowable-limit materials 731 metal transfer effects 726 overexposure to 724 oxyfuel gas processes 727 protection against 724 resistance welding (RW) 727 respiratory protective equipment 724 shielding gas(es), effects of 724Index Terms Links This page has been reformatted by Knovel to provide easier navigation. Fumes and gases (Cont.) sources of 725 sources, arc welding 725 sources of, metal transfer mode 726 thermal spraying 752 ventilation 724 727 water table 728 welding current, effects of 726 welding process, effects of 727 Furnace brazing, applications 37 Fusion welding 52 discontinuities associated with 538 Fusion welds 52 FW. See Flash welding. G Gas metal arc welding (GMAW) 10 buried arc 13 deposition rate 12 description of 10 discontinuities associated with 537 equipment 10 electrode extension 10 electrodes for 10 globular transfer 11 melting rates 79 metal transfer modes 11 pulsed spray 12 short circuiting transfer 11 shielding gases 10 spray transfer 11 Gas standards, welding 697 Gas tungsten arc welding (GTAW) 8 arc efficiency 90Index Terms Links This page has been reformatted by Knovel to provide easier navigation. Gas tungsten arc welding (GTAW) (Cont.) description of 8 disadvantages 9 discontinuities associated with 537 electrodes 9 equipment 9 power sources 9 shielding gases 8 skill requirements 10 welding current, polarity of 9 GMAW. See Gas metal arc welding. Groove-fillet weld combustion 194 Groove welds 189 complete joint penetration 190 partial joint penetration 190 GTAW. See Gas tungsten arc welding. H Hafnium 146 Hardenability 128 Hardness testing 256 ASTM test methods for 256 257 Brinell hardness test (HB) 256 257 conversion among scales 257 description of 256 Knoop hardness indenter 257 microhardness tests 256 257 portable Brinell test equipment 257 Rockwell hardness test (HR) 257 Vickers indenter 257 HAZ. See Heat-affected zone. Heat-affected zone (HAZ) 135 cracking 549 description of 130 135Index Terms Links This page has been reformatted by Knovel to provide easier navigation. Heat-affected zone (HAZ) (Cont.) evaluation of 285 hardenable alloys 138 precipitation hardening alloys 137 strength and toughness of 136 transformation of 136 Heat, conduction of, during fusion welding 97 cooling curves, weld metal 102 cooling rates 99 cooling rates, critical 101 heat-affected-zone width 105 heat conduction equations 98 peak temperature 102 preheat temperature in 102 solidification rate 205 Heat flow 88 See also Heat transfer. arc efficiency 90 91 arc welding, absorption efficiency 89 bibliography 112 Bremsstrahlung absorption, calculation of 94 energy absorption 89 fundamentals 88 general overview 88 heat input 84 laser and electron beam welding, absorption efficiency 93 weld pool 107 Heat transfer 88 See also Heat flow. arc welding, heat deposition in 95 96 boundary conditions 95 96 buoyancy 78 107Index Terms Links This page has been reformatted by Knovel to provide easier navigation. Heat transfer (Cont.) convective heat transfer 95 convective heat transfer, weld pool 105 driving forces 106 electromagnetic forces 107 emerging applications of 111 fundamentals 88 governing equations 95 heat deposition 96 Marangoni force 106 quantitative calculation of 95 111 thermal cycle 88 weld pool, convective heat transfer in 88 107 High-frequency upset welding (UW-HF) 21 See also Electric resistance welding. description of 21 electrodes 21 induction coil 22 High-frequency welding, safe practices 747 Highway bridge specifications 686 High-power-density processes 28 I IB. See Induction brazing. IEC. See International Electrotechnical Commission. IIW. See International Institute for Welding. Inclusions 550 causes and remedies 551 flux 551 indications of 599 oxide 552 slag 552 tungsten 550 Incomplete fusion 539 540 552 600 Incomplete joint penetration 539 540 553 600 624Index Terms Links This page has been reformatted by Knovel to provide easier navigation. Inertia friction welding 24 Induction brazing (IB) 37 Induction soldering (IS) 41 Induction welding (IW) 537 Infrared brazing 39 Inspection 580 activities, inspection 582 587 definition of 580 plan 583 584 terms, quality assurance 580 Inspection, brazed and soldered joint 634 Inspection plan, the 583 sampling methods 583 selection of a plan 584 statistical sampling 583 Inspection symbols 385 all-around-symbol examination 391 area of examination 389 arrow significance 388 elements of 385 extent of examination 389 field examination 391 length, section 389 letter designations, NDE 388 location, NDE symbol 389 number of examinations 389 radiation, direction of 391 reference line 388 specification and codes 391 supplementary symbols 391 symbols, combination 393 tail 388 INS. See iron soldering. Insufficient upset 567Index Terms Links This page has been reformatted by Knovel to provide easier navigation. International Electrotechnical Commission (IEC) 700 International Institute for Welding 697 700 708 International Organization for Standardization (ISO) 581 700 publications 701 IQI. See Radiography, image quality indicators. Iron soldering (INS) 41 IS. See induction soldering. ISO. See International Organization for Standardization. IW. See induction welding. J Jigs. See Fixtures. Joining process(es) 2 See also Individual processes. overview of 2 selection of 3 K Keyhole weld 29 L Lamellar tear(s) 547 559 Lamellar tearing 169 195 539 See also Lamellar tear. Laminations 540 558 618 Laser beam cutting (LBC) 45 See also Laser beam welding (LBW). advantages 46 applications 45 drilling 46 equipment 46 hazards 748 safe practices 748Index Terms Links This page has been reformatted by Knovel to provide easier navigation. Laser beam welding (LBW) 32 See also Laser beam cutting (LBC). description of 32 equipment 32 hazards 748 monitoring and control of 441 physics of 32 safe practices 32 748 LBC. See Laser beam cutting. LBW. See Laser beam welding. LEFM. See Linear-elastic fracture mechanics. Lever law 120 Line, treating a weld as 209 Load and resistance factor design (LRFD) 173 196 201 211 Low temperature(s), effects of 164 Liquid penetrant examination 619 applications 619 cracks, surface 624 developers 621 developers, aqueous 621 623 developers, dry powder 623 developers, nonaqueous 623 drying after cleaning 621 drying of workpiece 623 emulsifiers 620 equipment 620 examination of parts 624 indications, developing 623 interpretation of indications 624 materials, required 620 methods 619 penetrant, application of 621 penetrant, removal of excess 621Index Terms Links This page has been reformatted by Knovel to provide easier navigation. Liquid penetrant examination (Cont.) penetrant types 619 620 precleaning 621 postcleaning 624 procedures 621 procedures, ASTM standards for 621 M Machine welding. See Mechanized welding. Magnesium alloys 144 Magnetic fields, influence on arcs 71 See also Arc characteristics. arc blow 71 arc deflection 71 eddy current, effect on 73 Fleming's left-hand rule 71 Lorentz force 71 magnetic flux 71 magnetic materials, effect on 73 Magnetic particle examination 609 applications 611 banding 619 cold working 619 cracks, subsurface 618 cracks, surface 618 demagnetization 618 dry method 616 examination procedures 615 general process overview 609 incomplete fusion 618 incomplete joint penetration 618 indications, nonrelevant 618 indications, relevant discontinuity 618 laminations 618Index Terms Links This page has been reformatted by Knovel to provide easier navigation. Magnetic particle examination (Cont.) limitations 611 magnetic characteristics 619 magnetic field orientation 612 magnetization, circular 612 magnetization, indirect 615 magnetization, localized 612 magnetization, longitudinal 612 magnetization, prod 612 magnetization, residual 617 619 magnetizing current amount 616 magnetizing current types 615 porosity 618 recording results 617 seams 618 selection, inspection and methods 616 sequencing operations 616 slag inclusions 618 surface condition effects 619 undercut 618 wet method 616 617 yoke method 615 Manual welding 452 Material safety data sheet, sample 715 Marine welding standards 694 Martensite 124 Mechanical properties 159 See also Properties of metals; Corrosion properties. crack growth 162 creep 165 creep rupture 165 ductile-to-brittle transition 164 ductility 162Index Terms Links This page has been reformatted by Knovel to provide easier navigation. Mechanical properties (Cont.) elastic limit 160 elevated-temperature properties 165 endurance limit 162 fatigue life 162 fatigue limit 162 fatigue strength 162 fatigue stress range 203 fracture safe analysis 163 fracture toughness 164 low temperature 164 modulus of elasticity 160 notch-bar impact-test(s) 164 plastic deformation 163 stress-strain diagram 161 tensile strength 161 toughness testing 164 ultimate tensile strength (UTS) 161 yield strength 161 Young's modulus 160 See also Modulus of elasticity. Mechanized, automated, and robotic welding 451 See also Automated welding; Mechanized welding; Robotic welding. automated welding 458 bibliography 482 general description 452 mechanized welding 453 planning for 467 robotic welding 467 Mechanized welding 453 See also Automated welding; Robotic welding. definition of 452Index Terms Links This page has been reformatted by Knovel to provide easier navigation. Mechanized welding (Cont.) general description 453 feeding mechanisms 454 power source 454 specialized welding machines 457 system components 454 travel devices 454 variables, controlled 453 welding carriages 454 welding head manipulators 457 welding positioners 457 Melting rates 78 See also Metal transfer. cold cathode 79 definition 78 general control variables 79 gas metal arc welding 79 resistance heating, contribution to 79 shielded metal arc welding 81 submerged arc welding 81 thermionic compounds, effect on 79 welding current, effect on 79 Melt-through 544 See also Burn-through. Metallurgy, physical 116 age hardening 130 allotropic transformation 119 alloys 117 austenite 122 austenite decomposition 124 127 austenite grain size 128 austenite to ferrite, transformation of 123 austenization by welding process, steel 126Index Terms Links This page has been reformatted by Knovel to provide easier navigation. Metallurgy, physical (Cont.) bainite 124 cold working 121 constitution diagram 119 continuous cooling transformation diagrams 125 copper-nickel alloy system 119 120 cementite 123 critical temperatures 119 crystal lattice 116 crystalline structure of metals 116 decomposition products of austenite 122 deformation of metals, effects of 121 delta ferrite 122 delta ferrite to austenite, transformation of 123 equilibrium diagram 119 eutectic point 121 grain boundaries 227 grain structure, other changes in 129 hardenability 128 heat-affected zone (HAZ) 119 126 heat treatment of metals, effects of 121 interstitial alloying 117 interstitial solid solution 117 iron, alpha 122 iron and steel, phase transformations 122 iron-carbon system 122 isothermal transformation diagrams 124 127 lattice structure, body-centered-cubic 116 lattice structure, face-centered-cubic 116 lattice structure, hexagonal-close packed 116 liquidus 119 martensite 124 martensite transformation 125Index Terms Links This page has been reformatted by Knovel to provide easier navigation. Metallurgy, physical (Cont.) martensite start temperature (Ms) 128 martensite, tempering of 128 metallography 128 mechanical properties, alloy 119 microstructure, alloy 119 microstructure, deformed metal 121 multiphase alloys 118 pearlite 123 phase diagrams 119 phase diagrams, application of Lever Law to 120 phase diagrams, two component systems 119 phase transformations 119 phase transformations, iron and steel 122 precipitation hardening 130 quenched and tempered steels 129 recovery 121 recrystallization 121 silver-copper system 120 solidus 119 solutes 117 solvents 117 strain hardening 121 structure of metals 116 substitutional solid-solution alloy 117 121 tempered martensite 128 tempering, effects of 129 time-temperature-transformation (TTT) diagrams 124 transformation of austenite, factors affecting 127 Metallurgy of welding 141 weld interface diffusion 126 Metallographic examination 633 macroscopic examination 633 microscopic examination 634Index Terms Links This page has been reformatted by Knovel to provide easier navigation. Metal transfer 73 See also melting rate. active gases, effect on 76 argon, effect of polarity in 74 electrode negative 75 electrode positive 74 flux cored arc 78 gas metal arc 75 globular 73 other gases, effect of 76 physics of 74 pinch effect 74 pulsed current transfer 76 rotary arc 75 shielding gases, effect on 76 short circuiting 76 spray 73 74 spray, axial 74 submerged arc 77 transition current 74 Methods. See Standards. MIG welding. See Flux cored arc welding; Gas metal arc welding. Military specifications 699 Mine Safety and Health Association (MSHA). See U.S. Mine Safety and Health Administration. Modulus of elasticity 160 Molybdenum 148 Moment of inertia 172 Monitoring and control, principles of 422 423 distributing input variables 423 manipulated input variables 422 process response variables 423Index Terms Links This page has been reformatted by Knovel to provide easier navigation. Monitoring and control, process control systems 429 closed-loop control 430 definition, controller 429 definition, process control 429 open-loop control 429 Monitoring and control, process instrumentation 427 data displays 429 data recorders and loggers 429 Monitoring and control, process monitoring systems 427 Monitoring and control, sensing devices 423 acoustic pick-up transducer 427 capacitive sensors 427 definition of 423 design of 425 electric potentiometer 427 camera, thermal imaging 425 characteristics 424 electric current 426 electric potential 427 encoders 427 current shunt resistor 426 differential transformers, variable 427 flow meters, differential pressure 426 flow meters, mechanical 426 flow rate 426 force measurements 425 Hall-effect current sensor 426 inductive sensors 427 load cells 425 426 optical displacement sensors 427 optical pyrometers 425 photon detectors 425 physical properties sensed 424Index Terms Links This page has been reformatted by Knovel to provide easier navigation. Monitoring and control, sensing devices (Cont.) potentiometers, linear and rotary 427 pressure sensors, diaphragm type 425 pressure sensors, displacement 425 pressure sensors, piezoelectric type 426 process voltage 427 radiation sensors 427 resistive-temperature device (RTD) 425 synchros and resolvers 427 temperature measurement 424 thermistors 425 thermocouples 425 time measurement 424 toroid (Ragowski) coil 426 ultrasonic ranging sensors 427 units of measure 424 Monitoring and control, welding and joining processes 422 bibliography 448 general overview of 422 monitoring and control systems 431 principles of 422 process control systems 429 process monitoring systems 429 sensing devices 423 supplementary reading list 448 Monitoring and control systems, arc welding 431 See also Monitoring and control systems, brazing processes; Electron beam welding; Friction welding; Laser beam welding; resistance welding. arc elements, spectrographic analysis of 437 arc length and voltage control 432 436 basic process variables, control of 432Index Terms Links This page has been reformatted by Knovel to provide easier navigation. Monitoring and control systems, arc welding (Cont.) fill control, adaptive 434 joint finding 433 joint tracking 433 joint tracking, mechanical probe 433 435 joint tracking, through-arc-sensing 433 monitoring systems 431 other sensing devices 434 thermal cycle and cooling rate control 436 touch sensing 433 weld geometry, control of 436 Monitoring and control systems, brazing processes 447 See also Monitoring and control systems, arc welding; Electron beam welding; Friction welding; Laser beam welding; Resistance welding. atmosphere control in 448 general description 447 time-temperature control in 447 vacuum control in 448 Monitoring and control systems, electron beam welding 442 See also Monitoring and control systems: Arc welding; Brazing processes; Friction welding; Laser beam welding; resistance welding. beam deflection patterns 443 beam diagnostics devices 443 computer numeric control (CNC) 442 control systems for 442 graphs, beam density profile 443 monitoring systems for 442 power supplies, high-frequency (switch-mode style) 445 seam tracking, real time 443 secondary electron emission sensing (SEES) 445 tracking and misalignment, correction for 445Index Terms Links This page has been reformatted by Knovel to provide easier navigation. Monitoring and control systems, electron beam welding (Cont.) typical diagnostic systems 443 Monitoring and control systems, friction welding 445 See also Monitoring and control systems, arc welding; Electron beam welding; Laser beam welding; Resistance welding. process description 445 process monitors for 445 sensors, displacement 446 sensors used for 446 variables monitored 447 Monitoring and control systems, laser beam welding 441 See also Monitoring and control systems, arc welding; Brazing processes; Friction welding; Electron beam welding; Resistance welding. beam-material interaction 441 beam mode monitoring 441 focus position control 441 general description 441 joint finding 442 joint tracking 442 penetration control 442 thermal control 442 Monitoring and control systems, resistance welding 437 See also Monitoring and control systems, arc welding; Friction welding; Electron beam welding; Laser beam welding. electrode cooling, monitoring 440 electrode displacement, monitoring and measurement 440Index Terms Links This page has been reformatted by Knovel to provide easier navigation. Monitoring and control systems, resistance welding (Cont.) electrode force 439 impedance meters, commercially available 438 projection welding (PW) 439 resistance measurement, bridge-type 438 resistance to current flow 439 secondary loop current 437 secondary loop current, control of 438 secondary loop, resistance and impedance sensors 438 sensors, welding electrode 439 sensors, digital welding electrode 439 sensors, variable 437 439 sensors, welding force 439 voltage measurement 438 weld controllers, closed-loop 438 welding current 437 welding force, measurement of 440 MSHA. See U.S. Mine Safety and Health Administration. N National Board of Boiler and Pressure Vessel Inspectors (NBBPVI) 638 703 publications 703 National Electric Manufacturers Association (NEMA) 708 739 National Fire Protection Association (NFPA) 703 739 745 698 publications 704 National Institute of Occupational Safety and Health (NIOSH) 723 NBBPVI. See National Board of Boiler and Pressure Vessel Inspectors. NRC. See Nuclear Regulatory Commission.Index Terms Links This page has been reformatted by Knovel to provide easier navigation. NEMA. See National Electric Manufacturers Association. NFPA. See National Fire Protection Association. Nickel alloys 144 Niobium 147 See also Columbium. NIOSH. See National Institute of Occupational Safety and Health. Nondestructive examination 584 See also Inspection symbols; Proof testing. definition of 584 acoustic emission testing 586 electromagnetic examination 586 624 general description 584 liquid penetrant examination 586 619 magnetic particle examination 586 609 metallographic examination 284 methods 584 proof testing 630 radiographic examination 586 589 ultrasonic examination 586 602 visual examination 586 584 Nondestructive inspection. See Nondestructive examination. Nondestructive testing. See Nondestructive examination. Nuclear Regulatory Commission (NRC) 676 698 O OAW. See Oxyacetylene welding. Occupational Safety and Health Administration (OSHA) 712 729 General Industry Standards 712 Hazard Communication Standard 713 management support 713Index Terms Links This page has been reformatted by Knovel to provide easier navigation. Occupational Safety and Health Administration (OSHA) (Cont.) Occupational Safety and Health Act 712 714 regulations, fumes and gases 724 requirements, personal protective equipment 719 training, safety program 714 OFW. See Oxyfuel gas welding. OHW. See Oxyhydrogen welding. OSHA. See Occupational Safety and Health Administration. Other welding and joining processes 28 adhesive bonding 34 description of 28 electron beam welding (EBW) 29 electroslag welding (ESW) 33 laser beam welding (LBW) 32 Outgassing 31 Overlap 539 540 554 Overwelding 522 Oxide film 539 555 Oxyacetylene welding (OAW) 61 537 Oxyfuel gas cutting (OFC) 43 See also Oxyfuel gas welding (OFW). applications 44 description of 43 safe practices 720 skill requirements 44 torches 44 Oxyfuel gas welding (OFW) 27 See also Oxyfuel gas cutting (OFC). acetylene combustion 28Index Terms Links This page has been reformatted by Knovel to provide easier navigation. Oxyfuel gas welding (OFW) (Cont.) applications 27 description of 28 equipment 28 flame temperatures 28 fuel gases 28 736 safe practices 720 736 types of flame 28 welding procedure specifications 651 654 Oxygen-enriched atmospheres 732 Oxyhydrogen welding (OHW) 537 P Part preparation 167 PAC. See Plasma arc cutting. PAW. See Plasma arc welding. Pearlite 123 Percussion welding (PEW) 537 Performance qualification 668 brazing positions for 667 limitation of variables 669 qualification requirements 669 Performance qualification, nondestructive examination (NDE) personnel 676 acceptance criteria 678 operator qualification, Level 1 676 operator qualification, Level 2 678 operator qualification, Level 3 678 welding inspectors 678 welding inspectors, AWS certified 678 Performance qualification, brazing and brazing operator 673 acceptance criteria 673 performance qualification test record 675Index Terms Links This page has been reformatted by Knovel to provide easier navigation. Performance qualification, brazing and brazing operator (Cont.) qualification by specimen test 673 qualification by visual examination 673 qualification variables 673 standards, brazing 673 Performance qualification, thermal spray operators 675
كلمة سر فك الضغط : books-world.net The Unzip Password : books-world.net أتمنى أن تستفيدوا من محتوى الموضوع وأن ينال إعجابكم رابط من موقع عالم الكتب لتنزيل كتاب Welding Handbook - Volume 1 رابط مباشر لتنزيل كتاب Welding Handbook - Volume 1 
|
|