Admin مدير المنتدى


عدد المساهمات : 18745 التقييم : 34763 تاريخ التسجيل : 01/07/2009 الدولة : مصر العمل : مدير منتدى هندسة الإنتاج والتصميم الميكانيكى
 | موضوع: كتاب Enhanced Aircraft Platform Availability Through Advanced Maintenance Concepts and Technologies الإثنين 10 أكتوبر 2022, 12:07 am | |
| 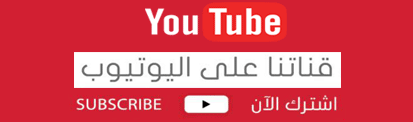
أخواني في الله أحضرت لكم كتاب Enhanced Aircraft Platform Availability Through Advanced Maintenance Concepts and Technologies (Amélioration de la disponibilité des plateformes d’aéronefs par l’utilisation des technologies et des concepts évolués de maintenance) The Report of an investigation by the AVT-144 Technical Team, which includes information contributed during the Workshop documented in RTO-MP-AVT-144
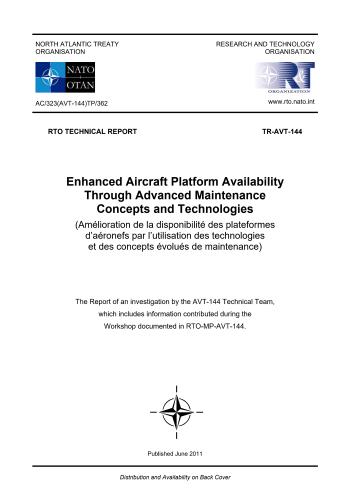 و المحتوى كما يلي :
Table of Contents Page List of Figures xiii List of Tables xx Acknowledgements xxi Programme Committee xxii Authors xxiv Executive Summary and Synthèse ES-1 Chapter 1 – Introduction 1-1 1.1 Objective and Scope 1-1 1.2 Approach Used by Technical Team 1-1 1.3 Other Relevant NATO RTO AVT Panel Investigations 1-2 1.4 Terminology 1-2 Chapter 2 – The Importance of Aircraft Platform Availability 2-1 2.1 Introduction 2-1 2.2 The Contribution of Availability to Military Capability 2-1 2.2.1 Military Capability 2-1 2.2.2 Force Effectiveness and Readiness 2-1 2.2.3 Aircraft Availability – A Key Measure of Force Effectiveness and Readiness 2-2 2.2.4 Relationship of Capability, Effectiveness and Availability in Systems Modelling 2-2 2.2.5 Availability and Mission Reliability 2-3 2.2.6 Maintenance-Free Operating Period (MFOP) 2-4 2.2.7 Availability Targets 2-5 2.2.8 Efficiency and Availability 2-6 2.3 Aircraft Availability in Some NATO Air Forces 2-6 2.3.1 Aircraft Availability in France 2-7 2.3.2 Aircraft Availability in the UK 2-8 2.3.3 Aircraft Availability in the USA 2-12 2.4 Goals and Strategies for Improving Aircraft Platform Availability Including Mission 2-19 Reliability 2.4.1 Availability Depends on the Need for Maintenance and the Associated Downtime 2-19 2.4.2 Through Life Goals for Optimizing Aircraft Availability 2-20 2.4.2.1 Goals for Aircraft Design and Development 2-20 2.4.2.2 Goals for the Maintenance/Support System 2-21 2.4.3 Joint Goals and Strategies for Minimising the Need for Maintenance 2-22 2.4.3.1 Maximise the Inherent (Design) Reliability and Mission Reliability 2-22iv RTO-TR-AVT-144 2.4.3.2 Achieve the Inherent (Design) Reliability and Mission Reliability in 2-24 Service 2.4.3.3 Limit Maintenance to Essential Tasks 2-25 2.4.4 Joint Goals and Strategies for Minimising Downtime for Required Maintenance 2-26 2.4.4.1 Design the Aircraft for Maintainability (Ease of Maintenance) 2-26 2.4.4.2 Reduce Downtime for Servicing 2-28 2.4.4.3 Reduce Downtime for Replacement/Restoration of Lifed Components 2-29 2.4.4.3.1 Focussed Design for Maintainability 2-29 2.4.4.3.2 Extend Remaining Useful Life 2-29 2.4.4.3.3 Improve the Scope and Accuracy of Usage Monitoring 2-29 2.4.4.3.4 Use On-Condition Inspections Instead of Component 2-29 Replacement/Restoration (Condition-Based Maintenance – CBM) 2.4.4.4 Reduce Downtime for Inspections (On-Condition and Failure Finding 2-31 Tasks) 2.4.4.5 Reduce Downtime for Age Exploration 2-32 2.4.4.6 Reduce Downtime for Diagnostics 2-32 2.4.4.7 Reduce Downtime for Failures that Cannot be Duplicated (CND) 2-33 2.4.4.8 Reducing Downtime for Repair 2-34 2.4.5 Health Monitoring and Management (HUMS/SHM/PHM/DPHM/IVHM) 2-35 Chapter 3 – Some National Perspectives on Aircraft Maintenance/Support 3-1 3.1 Poland 3-1 3.1.1 Effect of Political Change on Aircraft Maintenance 3-1 3.1.2 Reverse Engineering 3-1 3.1.3 Collection and Analysis of Maintenance and Operational Data 3-1 3.1.4 Monitoring of Aircraft Loads and Usage 3-2 3.1.5 Diagnostic and Non-Destructive Inspection Systems 3-3 3.1.6 Changes in Maintenance Systems 3-5 3.2 France 3-6 3.2.1 Change Motivated by Poor Availability and High Costs 3-6 3.2.2 Evolution in Design and In-Service Support to Achieve Deployability and 3-7 Repairability 3.2.2.1 French Air Force and Navy Experience with Deployed Operations 3-7 3.2.2.2 The Use of Integrated Logistics Support (ILS) to Achieve Deployability 3-7 and Repairability 3.2.3 Structure Intégrée de Maintien en condition opérationnelle des Matériels Aéronautiques 3-8 du ministère de la Défense (SIMMAD) 3.2.3.1 SIMMAD’s Genesis 3-8 3.2.3.2 SIMMAD’s Position in its Institutional Environment 3-9 3.2.4 Innovative Maintenance Concepts 3-11 3.2.4.1 The Case for Outsourcing 3-11 3.2.4.2 Maintaining the Rafale 3-11 3.3 Czech Republic 3-13 3.3.1 Historical Events 3-13 3.3.2 The Development of the Maintenance Concept for the L-159 Light Combat Aircraft 3-14 3.3.3 Engine 3-16RTO-TR-AVT-144 v 3.3.4 Avionics 3-16 3.3.5 AMOS Flight Data Recording System 3-16 3.3.6 Reliability and Availability 3-20 3.4 Netherlands 3-20 3.4.1 Availability as a Global Performance Indicator 3-20 3.4.2 Integrated Weapon System Management 3-21 3.4.3 Measures to Improve the Availability of the F-16 Fleet 3-21 3.4.4 Prognostic Health Monitoring 3-23 3.5 Sweden 3-24 3.5.1 Introduction 3-24 3.5.2 Description of the Swedish Defence Materiel Administration (FMV) 3-24 3.5.3 Life-Cycle Management at FMV 3-26 3.5.4 Integrated Operations and Maintenance System 3-28 3.5.5 The Availability Performance Program (APP) 3-31 3.5.5.1 Purpose and Content of the APP 3-31 3.5.5.2 The Importance of Understanding Operational and Support Requirements 3-33 3.5.5.3 Integration of the Design of the Aircraft and the Support System 3-34 3.5.5.4 Optimising the Support System with Respect to Availability and Cost 3-35 3.5.6 The Application of FMV’s APP to Recent Aircraft Programs 3-36 3.5.6.1 The Jas 39 Gripen 3-36 3.5.6.2 Nordic Standard Helicopter Program (NSHP) 3-42 3.6 United Kingdom 3-47 3.6.1 Introduction 3-47 3.6.2 Historical Context 3-47 3.6.2.1 The Defence Logistics Organisation’s Change Programme 3-47 3.6.2.2 The End-to-End (E2E) Programme 3-47 3.6.2.3 E2E Study Recommendations for Logistics Support 3-47 3.6.2.4 The Defence Logistics Transformation Programme 3-48 3.6.3 The Evolution of Aircraft Support Concepts 3-49 3.6.3.1 The Three-Attribute Model of Equipment Support 3-49 3.6.3.1.1 Equipment Support Tasks 3-49 3.6.4 Transformation Activities 3-50 3.6.4.1 Implementing the Forward/Depth Construct and Rationalising UK 3-50 Military Aircraft Support 3.6.4.1.1 From Four Lines to Two Levels 3-50 3.6.4.1.2 Rationalising to the Forward/Depth Construct 3-51 3.6.4.1.3 Examples of Rationalisation under the Forward/Depth 3-51 Construct 3.6.4.2 The Application of Lean Techniques 3-52 3.6.4.3 Partnering with Industry 3-52 3.6.4.4 Contracting for Availability 3-53 3.6.4.4.1 The DLO’s Transformation Staircase 3-53 3.6.5 Aircraft Support Transformation Examples 3-54 3.6.5.1 Examples of Lean Transformation 3-54 3.6.5.1.1 Tornado Depth Support 3-54 3.6.5.1.2 Tornado Forward Support 3-54 3.6.5.1.3 Harrier Depth Support 3-54vi RTO-TR-AVT-144 3.6.6 Next Steps 3-54 3.6.6.1 The Defence Industrial Strategy 3-54 3.6.6.2 Through Life Capability Management 3-55 3.6.6.3 Enabling Acquisition Change 3-55 3.7 Canada 3-55 3.8 United States of America 3-56 Chapter 4 – Metrics, Modelling, and Key Performance Indicators of Aircraft 4-1 Availability 4.1 Introduction 4-1 4.2 Metrics of Aircraft Availability/Readiness 4-1 4.3 Drivers of Aircraft Downtime 4-4 4.3.1 Boeing Analysis of the Downtime of a Long Range Transport Aircraft 4-4 4.3.2 USAF Analysis of Key Drivers of Availability 4-6 4.4 Modelling of Aircraft Availability/Unavailability 4-11 4.4.1 Simple Parametric Model 4-11 4.4.2 Discrete Event Simulation (DES) Modelling 4-14 4.4.3 System Health Operational Analysis Model (SHOAM) by the Boeing IVHM Center 4-15 4.4.4 UK Ministry of Defence Model for Evaluating Prognostic Health Management 4-17 Systems 4.4.5 Other Modelling and Forecasting of Aircraft Availability 4-25 4.4.5.1 Modelling Reliability and Availability Improvements Due to Modifications 4-25 (USAF – Institute for Defense Analysis and HQ Air Force Materiel Command) 4.4.5.2 Modelling for a Parametric Study to Reduce Downtime (Helsinki University 4-25 of Technology – BAE Systems Hawk) 4.4.5.3 Model for Forecasting Availability and Long-Term Planning of Interrelated 4-26 Factors (USAF – Air Force Logistics Management Agency and Air Force Institute of Technology) 4.5 The Use of Availability Metrics and Models in Performance-Based Contracting – A Case Study 4-26 4.5.1 The Availability Model and Process of Attributing Responsibility for Downtime for 4-26 the New Canadian Maritime Helicopter Program (MHP) 4.5.2 Contractual Accountability for Aircraft Unavailability in the Canadian MHP 4-34 4.5.3 Summary of Case Study in Performance-Based Contracting 4-34 4.6 Discussion and Conclusions 4-35 Chapter 5 – Maintenance/Support Management Concepts and Technologies for 5-1 Improving Aircraft Availability and Mission Reliability 5.1 Introduction 5-1 5.2 Systems Engineering and Project Management 5-2 5.3 Integrated Logistics Support 5-5 5.4 Availability-Based Contracting – Also Known as Performance-Based Logistics (PBL) 5-10 5.5 A Case Study in Systems Engineering and Availability-Based Contracting Strategies 5-12 5.5.1 Optimized Weapon System Support 5-12 5.5.2 The Division of Responsibilities Between the Air Force and Industry 5-13 5.5.3 Seeing Aircraft Availability in Context 5-15RTO-TR-AVT-144 vii 5.5.4 Measuring the Causes of Aircraft Unavailability and Attributing Responsibility 5-17 5.5.5 Factors Critical to the Success of Availability-Based Contracting 5-17 5.5.6 Implementation Status and Schedule of the Maritime Helicopter Programme (MHP) 5-18 5.6 Reliability and Maintainability (R&M) Management 5-18 5.7 Aircraft/Engine Structural Integrity Program (ASIP and ENSIP) 5-22 5.8 Total Life-Cycle Systems Management (TLCSM) and Through-Life Capability Management 5-25 (TLCM) 5.9 Integrated Project Teams (IPT) 5-27 5.10 Technology Insertion 5-28 5.11 Manufacturing Management 5-28 5.12 Reliability-Centred Maintenance (RCM) to Determine Essential Maintenance and Optimum 5-29 Failure Management Strategies 5.12.1 Evolution of RCM for the Design of Preventive Maintenance 5-29 5.12.2 RCM Failure Management Strategies 5-32 5.12.3 Choosing the Best Failure Management Strategy 5-34 5.12.4 RCM and “Condition-Based Maintenance (CBM)” 5-36 5.13 Lean and Other Enterprise Management Concepts 5-38 5.14 Maintenance Management Decision Support – Eurofighter Example 5-43 5.14.1 General 5-43 5.14.2 Decision Support at the Tactical Level 5-45 5.14.3 Decision Support at the Strategic Level 5-46 5.15 Integrating the Maintenance/Support System for a Major International Program – The A400M 5-48 Transport 5.15.1 Introduction 5-48 5.15.2 The Joint Organisation for Armaments Cooperation (OCCAR) 5-48 5.15.3 The A400M Programme 5-50 5.15.3.1 The Programme and the Aircraft 5-50 5.15.3.2 Key Performance Indicators and Modelling for A400M 5-52 5.15.3.3 Operational Availability and/or Operational Reliability? 5-54 5.15.4 Maintenance/Support Concepts to Improve A400M Availability 5-55 5.15.4.1 Commercial Approach 5-55 5.15.4.2 Optimised Scheduled Maintenance Programme 5-56 5.15.4.3 Extensive Use of On-Condition Maintenance and Automated Condition 5-57 Monitoring 5.15.4.4 Maintenance-Free Operating Period (MFOP) 5-58 5.15.4.5 Common Support Solutions 5-59 5.15.4.6 Pragmatic Support Concepts and Innovative Contracting 5-60 5.15.5 Technological Measures to Improve A400M Availability 5-63 5.15.5.1 Computer-Aided Design 5-63 5.15.5.2 Damage Tolerant Design 5-66 5.15.5.3 On-Board Systems Diagnostic Integration 5-68 5.15.5.4 Increased Components Reliability and Systems Redundancy 5-69 5.15.6 Conclusions 5-70 Chapter 6 – Aircraft and Support Equipment Concepts and Technologies for 6-1 Improving Aircraft Availability 6.1 Introduction 6-1viii RTO-TR-AVT-144 6.2 Usage Monitoring 6-3 6.2.1 Introduction 6-3 6.2.2 An Improved Approach to Usage Monitoring – The Fleet Usage Management System 6-3 (FUMS) 6.2.2.1 The Need to Improve Usage Monitoring 6-3 6.2.2.2 Methods of Usage Monitoring Used in FUMS 6-4 6.2.2.2.1 Comparison of Actual and Design Usage Spectra 6-4 6.2.2.2.2 Usage Index 6-5 6.2.2.3 Usage Spectrum 6-6 6.2.2.4 Fatigue Synthesis 6-7 6.2.2.5 Other Usage Factors 6-8 6.3 Failure Modelling for Prognostics (Life Estimation) 6-8 6.3.1 Introduction 6-8 6.3.2 Turbine Blade Case Study 6-10 6.3.2.1 Mechanical Structural Analysis Requirements 6-12 6.3.2.2 Engine Modelling and Thermal Boundary Conditions 6-14 6.3.2.3 Thermal Mechanical Stress Analysis 6-15 6.3.2.4 Probabilistic Creep Damage Analysis 6-16 6.3.2.5 Conclusions 6-21 6.4 Inspection Using Non-Destructive Evaluation (NDE) 6-22 6.4.1 The Role of NDE 6-22 6.4.2 NDE and Aircraft Life Management 6-22 6.4.3 NDE Related Costs and Cost Savings 6-23 6.4.4 Improvements to NDE Methods 6-23 6.4.5 Incorporation of NDE into System Level Life Management 6-25 6.4.6 NDE/I Applications Case Studies 6-26 6.4.6.1 AWACS E3A – Detection of Corrosion in Wing Skin 6-26 6.4.6.2 AWACS E3A – Detection of Debonds in ROTODOME Structure 6-27 6.4.6.3 F4-F Phantom – Detection of Fatigue Cracks in Stiffener at Upper and 6-28 Lower Wing Skin 6.4.6.4 Tornado – Detection of Corrosion at the Wing Diffusion Joint 6-30 6.4.6.5 Breguet Atlantic – Detection of Debonds in Honeycomb Structure 6-31 6.5 Sensors for On-Board Maintenance Systems 6-32 6.5.1 Introduction 6-32 6.5.2 General Sensor Technologies 6-32 6.5.2.1 The Roles of Sensors 6-32 6.5.2.2 Smart and MEMS-Based Sensors 6-34 6.5.2.3 Piezoelectric-Based Sensors 6-37 6.5.2.4 Fibre Optic Based Sensors 6-41 6.5.2.5 Comparative Vacuum Monitoring (CVM) Sensors 6-44 6.5.2.6 General Status of Sensor Technology 6-47 6.5.3 Corrosion Sensors 6-47 6.5.3.1 The Need for Corrosion Sensors 6-47 6.5.3.2 The Process of Environmental Degradation 6-47 6.5.3.3 General Approaches to Corrosion Sensing 6-49 6.5.3.4 Direct Measurement of Corrosion Effects 6-49 6.5.3.5 Measurement of Corrosivity of Environment 6-49RTO-TR-AVT-144 ix 6.5.3.6 Measurement of Climate (or Microclimate) to Input into a Predictive 6-49 Model 6.5.3.7 Measurement of Corrosion Products 6-49 6.5.3.8 Types of Sensor 6-50 6.6 Diagnostics for Electronic and Electrical Systems 6-55 6.6.1 Introduction 6-55 6.6.2 Advances in Ground-Based Automatic Test Equipment 6-55 6.6.2.1 Background 6-56 6.6.2.2 ATS Architecture Framework 6-57 6.6.2.3 Test Technology Development 6-57 6.6.2.3.1 Advanced Synthetic Instruments 6-58 6.6.2.3.2 Programmable Serial Bus Test 6-58 6.6.2.3.3 Reusing Diagnostic Data 6-59 6.6.2.3.4 Multi-Analog Capability (MAC) 6-59 6.6.2.3.5 High Density Analog Instrument 6-60 6.6.2.3.6 Common Tester Interface (CIT) 6-60 6.6.2.4 System-Level Demonstration 6-60 6.6.2.5 An Example: The US Navy Story 6-60 6.6.2.6 Impact of the Test Technology Developments on Weapon System 6-61 Readiness 6.7 Automated Inspection and Diagnostics for Mechanical Systems, Structure, and Engines 6-62 6.7.1 Introduction 6-62 6.7.2 Overview of Automated Inspection and Diagnostics for Mechanical Systems and 6-62 Structure 6.7.2.1 Introduction 6-62 6.7.2.2 Data Fusion 6-62 6.7.2.3 Retrofitable Troubleshooting Systems 6-63 6.7.2.4 Fully Integrated Sensor Suites 6-65 6.7.3 The Application of Advanced Diagnostics in the Engine of the Rafale Fighter 6-65 6.7.4 The Insertion of Advanced Diagnostic Technologies in an Ageing Fleet of Engines 6-71 6.7.4.1 Introduction 6-71 6.7.4.2 Background 6-71 6.7.4.3 The Early History of F-111 and DSTO Involvement 6-71 6.7.4.4 RAAF F-111 Fleet Sustainment 6-72 6.7.4.5 Introduction of On-Condition Maintenance in Place of Hard-Time 6-72 Overhaul 6.7.4.6 Diagnostic Requirement 6-73 6.7.4.7 Engine Acceptance Testing Using EDAS 6-74 6.7.4.8 Modular Diagnostics Using Gas Path Analysis 6-75 6.7.4.8.1 Performance “Stack” of Fault Signatures 6-76 6.7.4.8.2 Probabilistic Neural Network with Case Studies of RAAF 6-77 Repairs 6.7.4.8.3 Adaptive Model Approach 6-79 6.7.4.9 Flight Line Troubleshooting Using Expert Systems 6-82 6.7.4.10 Conclusions 6-84 6.8 Information Analysis 6-84 6.8.1 Introduction 6-84x RTO-TR-AVT-144 6.8.2 The Use of Integrated Reasoning with Flight and Historical Maintenance Data to 6-84 Diagnose Faults and Improve Prognosis 6.8.2.1 Introduction 6-84 6.8.2.2 Research Environment and Data 6-85 6.8.2.3 Use of Artificial Intelligence to Improve Diagnostics 6-86 6.8.2.4 Use of Data Mining to Improve Prognostics 6-88 6.8.2.5 PHM Software Architecture 6-90 6.8.2.6 Conclusions 6-92 6.8.3 Integrating Experience with BIT to Improve First-Time-Fix Performance 6-92 (An Application of Case-Based Reasoning) 6.8.3.1 Introduction 6-92 6.8.3.2 The Problem 6-92 6.8.3.3 The Solution 6-95 6.8.3.3.1 Knowledge Capture 6-95 6.8.3.3.2 Integration with Diagnostic Resources 6-96 6.8.3.3.3 Guided Diagnostics 6-97 6.8.3.3.4 Performance 6-97 6.8.3.4 Conclusions 6-98 6.9 Integrated Maintenance (Health Management) Systems for Usage Monitoring, Inspection, 6-98 Diagnostics, and Prognostics 6.9.1 General 6-98 6.9.2 The TATEM and AEPHM Programs 6-99 6.9.2.1 Background to TATEM and AEPHM 6-99 6.9.2.2 Basic Concepts 6-101 6.9.2.3 Problems of System by System PHM Approach 6-102 6.9.2.4 Modern Aircraft Systems 6-103 6.9.2.5 Concept of IVHM 6-104 6.9.2.6 Advanced Electrical Power Prognostics and Health Management 6-105 (AEPHM) Programme 6.9.2.6.1 Introduction 6-105 6.9.2.6.2 System Integration and Demonstration 6-110 6.9.2.6.3 Reasoning with Design Data 6-111 6.9.2.7 Where Next for IVHM? 6-113 6.10 Maintenance Concepts and Technologies for Achieving a Maintenance-Free Operating 6-114 Period (MFOP) 6.10.1 Challenging Traditional Reliability Thinking 6-114 6.10.2 What are the Real Customer Needs? 6-114 6.10.3 New Ways 6-114 6.10.3.1 Design Approach 6-115 6.10.3.2 Using Health Management Systems to Enhance MFOP Capability 6-116 6.10.4 Industry and Contractual Perspectives on the MFOP Concept 6-118 6.10.5 Conclusions 6-118 6.11 Rapid Repair of Aircraft Damaged in Action 6-119 6.11.1 Introduction 6-119 6.11.2 The Need for a Global Vision of Aircraft Repair 6-119 6.11.3 The French Air Force and Navy Operational Feedback on Deployability 6-122 and RepairabilityRTO-TR-AVT-144 xi 6.11.4 The Lessons Learnt About Battle Damage Repair 6-123 6.11.5 The Rafale Repair Vision 6-125 6.11.5.1 Short Description of Rafale 6-125 6.11.5.2 Principles of the Structure Maintenance Study 6-125 6.11.5.3 The Battle Damage Assessment and Repair (BDAR) Concept 6-126 Evolution 6.11.5.4 Damage Assessment of the Aircraft 6-127 6.11.5.4.1 Structural Assessment of the Airframe 6-127 6.11.5.4.2 Systems Assessment 6-128 6.11.5.4.3 Operational Assessment and Limitations 6-129 6.11.5.5 Repair of the Damaged Aircraft 6-130 6.11.5.5.1 Example of Structural Repairs 6-130 6.11.5.5.2 Engine Repairs 6-130 6.11.5.5.3 Examples of System Repairs 6-131 6.11.5.6 Strong Points of Rafale Maintenance and Documentation 6-131 6.11.6 Future Foreseen Improvements: Assistance to the Aircraft Assessment and 6-132 Repair Decision 6.11.7 Conclusions 6-135 6.12 Corrosion Prevention and Repair 6-135 6.12.1 Introduction 6-135 6.12.2 Types (Forms) of Corrosion Identified – Applies to All Aircraft Platforms 6-136 (Types) 6.12.3 Current Practice 6-137 6.12.4 How are Corrosion Repairs Done Now? 6-137 6.12.5 What is Not Done? 6-138 6.12.6 Some Advanced Technologies for Corrosion Management 6-138 6.12.6.1 Corrosion Preventive/Inhibiting Compounds 6-138 6.12.6.2 Trivalent Chromium Pre-treatment (TCP) 6-139 6.12.6.3 Demonstration of Trivalent Chromium Pre-treatment (TCP) H-46 6-140 Helicopters 6.12.6.4 Advanced Organic Coatings 6-141 6.12.6.5 Photostrip – Photochemical Stripping of Aircraft Coatings 6-141 6.12.6.6 Advanced Sealants and Adhesives 6-143 6.12.6.7 Emerging Sealant Technologies 6-145 6.12.6.8 Fleet Outreach Program for Corrosion Management Technologies 6-146 6.12.6.9 Aircraft Inspection – NDE of Corrosion 6-147 6.12.6.10 Corrosion and Environmental Sensors 6-150 6.12.7 Our Challenge 6-150 6.12.8 Dehumidification to Reduce Preventive and Corrective Maintenance for 6-151 Corrosion 6.12.8.1 Swedish Air Force Experience with Dehumidification of Aircraft 6-151 6.12.8.2 Investigation on Material in Mobilization Storage 6-152 6.12.8.3 Experience from the Storage Test Project 6-152 6.12.8.4 Dehumidification of Aircraft in Service 6-153 Chapter 7 – Summary and Conclusions 7-1 7.1 Achievement of Objective 7-1xii RTO-TR-AVT-144 7.2 The Importance of Aircraft Platform Availability 7-1 7.3 Goals for Improving Availability 7-2 7.4 Management Concepts and Technologies 7-3 7.4.1 Categories of Management Concepts and Technologies 7-3 7.4.2 Systems Engineering and Project Management 7-4 7.4.3 Modelling and Simulation of the Maintenance/Support System 7-4 7.4.4 Integrated Logistics Support (ILS) 7-4 7.4.5 Availability-Based Contracting and Performance-Based Logistics (PBL) 7-5 7.4.6 Reliability and Maintainability (R&M) Management 7-5 7.4.7 Aircraft and Engine Structural Integrity Programs (ASIP and ENSIP) 7-5 7.4.8 Total Life-Cycle Systems Management (TLCSM) and Through-Life Capability 7-6 Management (TLCM) 7.4.9 Integrated Project Teams (IPT) 7-6 7.4.10 Technology Insertion (TI) 7-7 7.4.11 Manufacturing Management 7-7 7.4.12 Reliability-Centred Maintenance (RCM) to Determine Essential Maintenance and 7-7 Optimum Failure Management Strategies 7.4.13 Lean and Other Enterprise Management Concepts 7-8 7.4.14 Maintenance Management Decision Support 7-9 7.4.15 Integrating the Maintenance/Support System for a Major Program 7-9 7.4.16 Other Maintenance/Support Management Concepts and Technologies 7-10 7.5 Aircraft and Equipment Concepts and Technologies 7-10 7.5.1 Categories of Aircraft and Equipment Concepts and Technologies 7-10 7.5.2 Usage Monitoring 7-10 7.5.3 Failure Modelling for Prognostics (Life Estimation) 7-11 7.5.4 Inspection Using Non-Destructive Evaluation (NDE) 7-11 7.5.5 Sensors for On-Board Usage Monitoring and Inspection Systems 7-12 7.5.6 Diagnostics for Electrical and Electronic Systems 7-13 7.5.7 Automated Inspection and Diagnostics for Mechanical Systems, Structure, and 7-14 Engines 7.5.8 Information Analysis 7-16 7.5.9 Integrated Systems for Usage Monitoring, Inspection, Diagnostics, and Prognostics 7-17 7.5.10 Using Advanced Maintenance Concepts and Technologies to Achieve a 7-19 Maintenance-Free Operating Period (MFOP) 7.5.11 Rapid Repair of Aircraft Damaged in Action 7-19 7.5.12 Corrosion Prevention and Repair 7-20 7.5.13 Other Aircraft and Equipment Concepts and Technologies 7-20 Chapter 8 – References 8-1 Annex A – List of Workshop Participants A-1 Annex B – Workshop Program with Authors B-1 Annex C – List of Definitions C-1RTO-TR-AVT-144 xiii List of Figures Figure Page Figure 2-1 System Effectiveness Models Described in Mil-Hdbk-338B that have been Used in 2-3 the Past Figure 2-2 Operational Availability of UK Tornado GR4 Aircraft 2000 – 2006 2-9 Figure 2-3 Operational Availability of UK Harrier Aircraft 2000 – 2006 2-10 Figure 2-4 UK Joint Battlefield Support Helicopter Requirements 2-11 Figure 2-5 Average Availability of UK Helicopters Committed to Iraq Operations 2-12 Figure 2-6 US DoD Average Annual Mission Capable (MC) Rates of US Military Aircraft by 2-13 Service in Fiscal Years 1998 – 2002 Figure 2-7 US DoD Average Annual MC Rates by Aircraft Type in Fiscal Years 1998 – 2002 2-14 Figure 2-8 US DoD Average Annual Full Mission Capable (FMC) Rates by Aircraft Type in 2-15 Fiscal Years 1998 – 2002 Figure 2-9 Average Downtime per Flight Hour During the Period 1991 to 2004 of All USAF 2-18 Aircraft Assigned to Operational Units Figure 3-1 Distribution of Failures Among Sub-Systems in the Mi-14 Helicopter 3-2 Figure 3-2 Service Profiles of the Two Groups of MiG-29 Aircraft 3-3 Figure 3-3 The SD-KSA Diagnostic System in Operation 3-4 Figure 3-4 A Microwave Probe 3-4 Figure 3-5 The DAIS System in Operation 3-5 Figure 3-6 The Integrated Logistic Support Approach of the French Air Force and Dassault 3-8 Aviation Figure 3-7 DGA to SIMMAD – Support Responsibilities Shift 3-9 Figure 3-8 The Chain of Command for Joint Aircraft Maintenance/Support – From the Joint 3-10 Air Support Chain to the Operational Chain Figure 3-9 Innovative Maintenance Concepts 3-12 Figure 3-10 Aero Vochody L-159 Light Combat Aircraft (Czech Republic) 3-14 Figure 3-11 Aircraft Monitoring System (AMOS) on the Czech L-159 Aircraft 3-17 Figure 3-12 FRAME159 Structural Flight Data Recorder System 3-19 Figure 3-13 RNAF Chinook Helicopter with Underslung Loads 3-23 Figure 3-14 The Tools of PHM in the RNLAF 3-24 Figure 3-15 Typical Work Share Between FMV and Industry 3-26 Figure 3-16 Core Life-Cycle Management (LCM) Concept in the Swedish Armed Forces 3-28 Figure 3-17 The Three Main Functions of O&M 3-29 Figure 3-18 The Major Parts of the Operation and Maintenance System 3-29 Figure 3-19 Single Integrated O&M System Covering All Swedish Air Force Materiel 3-31 Figure 3-20 The Availability Performance Program (APP) 3-32 Figure 3-21 Operational Performance Breakdown with Examples of Parameters which Affect it 3-34xiv RTO-TR-AVT-144 Figure 3-22 The Process of Analysing the Availability Requirements 3-35 Figure 3-23 Part of the Iterative Process Involving the Optimization and Acquisition of 3-36 Maintenance Resources Figure 3-24 Jas 39 Gripen Aircraft – Replacement for the AJ 37 Viggen 3-37 Figure 3-25 Trends in Swedish Fighter Aircraft Development, Production and O&M Costs 3-37 Figure 3-26 Historical Trend in Maintenance Cost in Kronor (SEK) per Flight Hour of Swedish 3-40 Fighter Aircraft Figure 3-27 Historical Trend in Maintenance Cost in Man-Hours per Flight Hour of Swedish 3-40 Fighter Aircraft Figure 3-28 Ongoing Estimates of Life Support Cost (LSC) Compared with the Contracted Level 3-41 Figure 3-29 History of Achievement/Shortfall in Key Availability Related Metrics on the Jas 39 3-41 Gripen Program Compared to the Aircraft Specification Figure 3-30 Candidate Aircraft for the Nordic Standard Helicopter Program (NSHP) 3-42 Figure 3-31 Originally Proposed Variants of the Nordic Standard Helicopter 3-43 Figure 3-32 Schematic of the Aggregate Life-Cycle Cost (LCC) Model for the Nordic Standard 3-44 Helicopter Program (NSHP) Figure 3-33 For Evaluating Tenders for Spare Parts, the Life-Cycle Cost of the Aircraft was 3-45 Estimated for an Aircraft Availability of 80% Figure 3-34 Comparison of Estimated Life-Cycle Costs for Four of the NSHP Tenders 3-46 Figure 3-35 The DLO’s Transformation Staircase 3-53 Figure 4-1 Sub-Division of Aircraft Downtime Used in Boeing IVHM Center’s SHOAM Model 4-3 Figure 4-2 Long Range Transport Aircraft Downtime Distributions 4-5 Figure 4-3 Long Range Transport Aircraft Downtime Drivers 4-5 Figure 4-4 Relative Contributions of Scheduled and Unscheduled Maintenance Tasks and 4-6 Supply Delays to the Downtime of C-5 Aircraft at Operating Units Figure 4-5 Trends in the Contributions of Scheduled and Unscheduled Maintenance Tasks and 4-7 Supply Delays to the Downtime of C-5 Aircraft at Operating Units Figure 4-6 Relative Contributions of Airframe, Engines, and Systems to the Downtime of C-5 4-8 Aircraft at Operating Units Figure 4-7 Trends in the Contributions of Airframe, Engines, and Systems to the Downtime of 4-8 C-5 Aircraft at Operating Units Figure 4-8 Maintenance and Supply Downtime for Various Systems on USAF C-5 at Operating 4-10 Units Figure 4-9 Division of Time Used by the Canadian Air Force for Operational Availability 4-11 Measurements Figure 4-10 Illustrations of Sensitivity Studies Performed Using the SHOAM Model for a Long 4-17 Range Strike Aircraft Figure 4-11 Activity Cycle Diagram (ACD) for a Single-Deployment of Chinook Helicopters 4-19 Without HUMS Figure 4-12 Activity Cycle Diagram (ACD) for a Single-Deployment of Chinook Helicopters 4-20 With HUMS Figure 4-13 Prediction of Downtime Due to D States (Aircraft Grounded Awaiting Spares) – 4-23 All DeploymentsRTO-TR-AVT-144 xv Figure 4-14 Prediction of Loss to Corrective Maintenance (CM) – All Deployments 4-24 Figure 4-15 Model Prediction of the Variation of Predictive Maintenance Window (Prognostic 4-25 Interval) on Chinook Helicopter Average Availability During 6 Different Simulated Deployments Figure 4-16 Decomposition of Aircraft Operational Availability AO by Design Attribute to the 4-27 Organizational Level for the Canadian Maritime Helicopter Program (MHP) Figure 4-17 Data and Analysis Provided to Bidders by DND to Bidders for the Canadian MHP 4-30 as a Basis for Contractor Estimates of Aircraft Unavailability Figure 4-18 Systems Engineering Approach to the Provision of Availability Performance Targets 4-31 for Aircraft Sub-Systems and Contractor-Supplied Support for the Canadian MHP Figure 4-19 Tracking of the Active and Inactive Periods of Every Individual On-Aircraft 4-32 Maintenance Task, and the Causes of Any Inactive Periods for the Canadian MHP Figure 4-20 Use of a Book Value (BV) in Attributing Downtime to the Prime Contractor for 4-32 Active Maintenance by Canadian Forces Personnel on the MHP (Case 1 BV < Active Maintenance Time) Figure 4-21 Use of a Book Value (BV) in Attributing Downtime to the Prime Contractor for 4-33 Active Maintenance by Canadian Forces Personnel on the MHP (Case 2 BV > Active Maintenance Time) Figure 4-22 Summations and Normalisations of Downtime Attributed to the Prime Contractor 4-33 and DND, Respectively, for an Individual Downing Event Figure 5-1 Systems Engineering Process Flow 5-4 Figure 5-2 Current Cost Breakdown of Product Support in the Development Phase 5-6 Figure 5-3 Illustration of How Most of the Life-Cycle Cost is Determined by Decisions Made 5-6 Prior to Full Scale Development Figure 5-4 Illustration from a US GAO Report of the Percentage of Life-Cycle Costs 5-7 Determined at Various Points in a Typical Military Acquisition Process Figure 5-5 The Integration of Integrated Logistic Support (ILS) and Aircraft Design 5-7 Figure 5-6 Process Diagram for ILS in MOD UK Guide to Integrated Logistic Support 5-8 Figure 5-7 Illustration of ILS Activities Within MOD UK’s Defence Equipment Acquisition 5-9 and Materiel Support (DEAMS) Business Concept Figure 5-8 The Importance of Aircraft Operational Availability AO to a Military Force 5-16 Figure 5-9 Aircraft Structural Integrity Program – Tasks I and II 5-24 Figure 5-10 Aircraft Structural Integrity Program – Tasks III through V 5-25 Figure 5-11 Outline of US Navy RCM Process 5-31 Figure 5-12 ISO-13374 Data Processing and Information Flows 5-37 Figure 5-13 Depot Maintenance Production Line Before Lean Transformation 5-40 Figure 5-14 Depot Maintenance Production Line After Lean Transformation 5-40 Figure 5-15 Streamlined Access to Maintenance Tools and Resources After Lean 5-41 Transformation Figure 5-16 KC-135 Depot Maintenance Delivery Performance – Percentage of Aircraft on 5-42 Time Figure 5-17 Integrated Monitoring and Recording System (IMRS) on the Eurofighter 5-44 Figure 5-18 Information Provided by the Integrated Monitoring and Recording System (IMRS) 5-45 on the Eurofighter for Decision Support at the Tactical and Strategic Levelsxvi RTO-TR-AVT-144 Figure 5-19 Measuring the Effectiveness of Tactical Decision Support by the Effect on 5-46 Eurofighter Operational Availability Figure 5-20 Product Life-Cycle Management SW for Eurofighter Typhoon 5-47 Figure 5-21 OCCAR Programmes, Estimated Total Costs, and Participating States 5-49 Figure 5-22 A View of the A400M Military Transport Aircraft 5-51 Figure 5-23 A400M Life-Cycle Cost Toolsheet Spares Availability Calculation (Example) 5-53 Figure 5-24 Airbus Fleet Operational Reliability (Percentage of Flights Without Delay Greater 5-55 Than 15 min or Interruption for Technical Reasons) Figure 5-25 On-Condition Maintenance – Examples of Schedule Interval Definition 5-58 Figure 5-26 Estimated Occupation of Industry Maintenance Docks (Baseline Support Concept) 5-62 Figure 5-27 Portion of A400M Digital Mock-Up (DMU) – Forward Fuselage and Cockpit 5-63 Figure 5-28 The Airbus Supportability Engineering Process 5-64 Figure 5-29 Example of Qualitative Maintainability Analysis (QMA) Using the A400M Digital 5-65 Mock-Up Figure 5-30 Example of Operational Reliability Analyser (ORA) Main Interface Sheet 5-66 Figure 5-31 Airbus A340-600 Full-Scale Fatigue Test 5-67 Figure 5-32 Comparison of Fatigue Consumption in Wing Structure Significant Items (SSI) 5-68 Figure 5-33 A400M Maintenance Data System (MDS) External Interfaces and Main Functions 5-69 Figure 6-1 Comparison of Actual Usage Spectrum and the Design Usage Spectrum 6-5 Figure 6-2 Usage Index Summary View 6-6 Figure 6-3 Synthesis of Fatigue for an Engine Component Using a Neural Network and UIs 6-7 Figure 6-4 Results of Synthesised Fatigue 6-8 Figure 6-5 Engineering Flow Diagram for the Prognosis System Designed and Implemented 6-11 by Life Predictions Technology Inc. (Patent Pending) Figure 6-6 Typical Engine Profile in Terms of Turbine Inlet Temperature and Speed 6-12 Figure 6-7 Finite Element Model of the Blade with Some Life-Limiting Nodes Displayed 6-13 Figure 6-8 Computed Leading and Trailing Edge Temperature Distributions 6-14 Figure 6-9 Temperature Profile for RRA 501 KB 6-15 Figure 6-10 Von Mises Stress Profile of the Blade 6-16 Figure 6-11 Grain Size Variation in MAR M246 Blades 6-18 Figure 6-12 Grain Boundary Carbide Particle Radius Variation in MAR M246 Blades 6-18 Figure 6-13 Grain Boundary Carbide Inter-Particle Spacing Variation in MAR M246 Blades 6-19 Figure 6-14 Weibull Distributions of Creep Life for Node Number 10217 6-20 Figure 6-15 AWACS E3A Aircraft – Detection of Corrosion in Wing Skin 6-27 Figure 6-16 AWACS E3A Aircraft – Detection of Debonds in ROTODOME Structure 6-28 Figure 6-17 F4-F Phantom Aircraft – Detection of Fatigue Cracks in Stiffener at Upper and 6-29 Lower Wing Skin Figure 6-18 Tornado Aircraft – Detection of Corrosion at the Wing Diffusion Joint 6-30 Figure 6-19 Breguet Atlantic Aircraft – Detection of Debonding in Honeycomb Structure in the 6-31 Fuselage and WingRTO-TR-AVT-144 xvii Figure 6-20 An On-Board Health Management System Linked Through Advanced 6-33 Communications with the Broader Maintenance/Support System Figure 6-21 Smart Sensor Concept Defined by IEEE 1451 6-35 Figure 6-22 MEMS-Based Smart Sensor Node 6-36 Figure 6-23 MEMS-Based Pressure Sensor for Gas Turbine Engine Applications 6-36 Figure 6-24 A Typical Gas Turbine Engine with the MEMS Pressure Transducer, and a Typical 6-37 Frequency Response for a Full Thrust Condition Figure 6-25 Arrayed Piezoceramic Sensors Used for Damage (Crack) Detection and 6-38 Localization Figure 6-26 Exfoliated Test Article with Four Integrated Ultrasonic Transducers Arrays (UTA) 6-39 and a Typical UTA Response Figure 6-27 Passive and Active Sensing Mode Using Piezoelectric Materials 6-40 Figure 6-28 A SMART Technology-Based Structural Health Monitoring System 6-40 Figure 6-29 Fibre Bragg Gratings Principle of Operation 6-42 Figure 6-30 Bragg Grating-Based Sensing 6-43 Figure 6-31 Illustration of a Fighter Jet Health Monitoring System 6-43 Figure 6-32 Conceptual Illustration of a Micro-Arrayed Highly Multiplexed FBG Interrogation 6-44 System Figure 6-33 Conceptual Model and Principle of Operation of a Typical CVM System 6-45 Figure 6-34 Illustration of Crack Detection Using CVM Technology 6-45 Figure 6-35 Commercial CVM System – With and Without Crack 6-46 Figure 6-36 Progress of Degradation in a Protection Scheme 6-48 Figure 6-37 Structure of a Flaw in a Standard Protection Scheme Illustrating Environmental 6-48 Factors in Chromate Exhaustion and Metal Degradation Figure 6-38 The Various Stages of Corrosion and the Availability of Sensors to Detect the 6-51 Associated Physical and Chemical Phenomena Figure 6-39 Sentinel Coating Degradation Sensor by BAE Systems 6-53 Figure 6-40 Illustration of a Multi-Channel/Higher Performance COTS Datalogger System 6-54 Figure 6-41 Multi-Functional Sensor (MuFCS) by BAE Systems – Different Environmental 6-54 Sensors on a Single Chip Figure 6-42 US DoD Automatic Test System (ATS) Framework 6-57 Figure 6-43 Past and Future Development of ATS in the US Navy 6-61 Figure 6-44 Integrated Maintenance Concept for SNECMA M-88 Engine in the Rafale 6-66 Figure 6-45 I Level Ground Test Utilities for Trouble Shooting 6-67 Figure 6-46 On-Board Diagnosis – Specific Sensors and Indicators in Addition to Engine 6-67 Controls Figure 6-47 HARPAGON Ground Support Station 6-68 Figure 6-48 Example of Analytical Output from Dassault’s HARPAGON, Showing Imbalance 6-69 in the LP Rotor Figure 6-49 Downtime Reduction by Extending the Useful Lives of Engine Components 6-70 Figure 6-50 Reduction of Downtime and Improvement of Mission Reliability 6-70 Figure 6-51 Causes of Unscheduled Maintenance and Appropriate Diagnostic Techniques 6-74xviii RTO-TR-AVT-144 Figure 6-52 Gas-Path Diagnostic Methods and Process Developed by DSTO 6-76 Figure 6-53 Performance Stack Diagnosis of Engine P103-8841 6-77 Figure 6-54 Links Between Observed Performance and Mechanical Condition 6-78 Figure 6-55 Diagnostic Comparison of a Symptom to 4 Previous Repairs 6-79 Figure 6-56 Procedure to Calculate Scale Factors in Adaptive Modelling 6-80 Figure 6-57 Adaptive Model Approach for Test-Cell Data 6-81 Figure 6-58 Scale Factor Domains Between Efficiency and Mass-Flow for Compressor 6-82 Degradation Figure 6-59 Operational Environment Around the Line Technician 6-86 Figure 6-60 Deployment of the IDS Trial System 6-87 Figure 6-61 Data Mining Methodology to Build Prognostic Models 6-89 Figure 6-62 NRC PHM High Level Infrastructure 6-91 Figure 6-63 Anticipating and Recognizing Failures 6-93 Figure 6-64 The Broad Distribution of Experience 6-94 Figure 6-65 Knowledge Capture 6-96 Figure 6-66 The Effect of IVHM on TAT 6-102 Figure 6-67 Smith’s Remote Interface Unit (RIU) 6-103 Figure 6-68 OSA-CBM 6-105 Figure 6-69 Advanced Electrical Power Prognostics and Health Management (AEPHM) 6-106 Programme – Overview Figure 6-70 GE Aviation Systems Power Distribution Unit (PDU) 6-106 Figure 6-71 AEPHM Actuator Test Rig 6-107 Figure 6-72 Load-Independent Motor Performance Algorithms – Results 6-108 Figure 6-73 AEPHM Fuel System Test Rig 6-109 Figure 6-74 AEPHM Fuel Pump Results – Pump Frequency Change Indicates Potential 6-109 Failure Figure 6-75 AEPHM System Integration 6-110 Figure 6-76 AEPHM Fuel System for Diagnostic Reasoning 6-112 Figure 6-77 Failure Life Characteristics 6-116 Figure 6-78 Reliability vs. Time and Probability of Maintenance-Free Operating Period 6-117 (MFOP) Completion Figure 6-79 The Aircraft Battle Damage Assessment and Repair (BDAR) Context 6-120 Figure 6-80 Global Vision Needed for Aircraft Repair 6-121 Figure 6-81 The Integrated Logistic Support (ILS) Approach 6-122 Figure 6-82 Example of Mirage 2000 Battle Damage Repair (BDR) Booklet Content 6-124 Figure 6-83 Rafale Basic Sub-Systems Definition and Integration 6-125 Figure 6-84 French BDAR Methodology as Applied to Rafale 6-127 Figure 6-85 Criticality of Structural Members 6-128 Figure 6-86 Example of System Analysis Used for Repair Decision Tables 6-129 Figure 6-87 Basic Structural Repair Examples 6-130RTO-TR-AVT-144 xix Figure 6-88 Example of Basic Pipe Repairs 6-131 Figure 6-89 Examples of Technologies Making Identification and Repair Easier 6-132 Figure 6-90 Use of CECILIA Workshop to Assess a Combined Damage (or Failure) Criticality 6-133 Figure 6-91 Bayesian Network Used as a Repair Decision Assistance Tool 6-134 Figure 6-92 F/A-18 Undergoing Repaint 6-139 Figure 6-93 H-46S Helicopter Masked for Painting 6-140 Figure 6-94 H-46S Helicopter After Painting 6-140 Figure 6-95 Photostripping of Paint 6-142 Figure 6-96 Photostripping of Rotor Blade Coating 6-143 Figure 6-97 Skyflex Aircraft Sealant – “Peel and Stick” Teflon Foam Tape Substitute for 6-145 2-Part Paste Sealants Figure 6-98 Bristle Discs and Rotary Cutters from 3M Simplify and Speed Sealant Removal 6-146 and Reduce Solvent Use Figure 6-99 Fleet Outreach Program 6-146 Figure 6-100 Alpha MCD Unit 6-147 Figure 6-101 H-60 Transmission Support Beam Cracks 6-148 Figure 6-102 Ultrasonic Guided Wave Inspection Developed for Detection of H-60 Cracks 6-149 Figure 6-103 Environmental (Moisture) Sensor for Use on Aircraft Structure 6-150 Figure 6-104 Our Challenge for Corrosion Control and Life Management 6-151 Figure 6-105 Effect of Dehumidification on the Number of Failures in 2,300 Flying Hours 6-154 Figure 6-106 Effect of Dehumidification on MTBF 6-154 Figure 6-107 A Dehumidifier for Aircraft 6-155 Figure 6-108 Dehumidification of the On-Board Oxygen Generator System (OBOGS) 6-156 Figure 6-109 Condensation Absorbed by Insulation Blankets on the Interior of an Aircraft Skin 6-157 List of Tables Table Page Table 2-1 Average Availability of French Military Aircraft Compared to Availability Targets 2-7 Table 2-2 Average Availability of French Military Aircraft from 1998 to 2006 2-8 Table 2-3 Key DoD Aircraft Models and 2002 MC (Suffix a) and FMC (Suffix b) Goals in 2-16 Percent Table 2-4 Comparison of the MC Rates and MC Goals of DoD Aircraft in 2002 2-17 Table 3-1 Means of Checking Individual Aircraft Systems 3-18 Table 3-2 Table of Reliability Parameters During Selected Exercises 3-20 Table 4-1 Illustrative Example of Prediction of Operational Availability from Historic Data 4-14 from a Maintenance Data System, Using Equations (7), (11), and (12) Table 4-2 Parameters and Metrics Used in Boeing’s System Health Operational Analysis 4-16 Model (SHOAM) Table 4-3 HUMS Elements in Single Deployment Mathematical Model 4-22 Table 4-4 Metrics in the Availability Model for the Canadian MHP 4-27 Table 5-1 Division of CH148 Support Service Responsibilities Between DND and the 5-14 Contractor Table 5-2 Common Reliability Program Elements 5-19 Table 5-3 Typical Distribution of Reliability Program Activities Among Life-Cycle Phases 5-20 Table 5-4 Typical Distribution of Maintainability Program Activities Among Life-Cycle 5-22 Phases Table 5-5 Scheduled Maintenance Gains Through the MSG-3 Process 5-56 Table 5-6 Expected Scheduled Maintenance Downtime 5-57 Table 5-7 Potential Whole Life Cost (WLC) Gains of A400M Common Support 5-60 Table 5-8 A400M Support Concepts 5-61 Table 6-1 Dynamic Modulus of Elasticity and Shear Modulus for Mar M246 Alloy 6-13 Table 6-2 Tensile Properties of Mar M246 Alloy 6-14 Table 6-3 Nodal Creep Life Prediction Results of Subject RRA 501KB Turbine Blade 6-17 Table 6-4 Probabilistic Distribution of Nodal Creep Life 6-21 Table 6-5 Several Types of Corrosion Sensor, Principally Aimed at Aircraft Structures 6-50 Table 6-6 Combinations of Environments and Materiel in Long-Term Storage Study 6-152
كلمة سر فك الضغط : books-world.net The Unzip Password : books-world.net أتمنى أن تستفيدوا من محتوى الموضوع وأن ينال إعجابكم رابط من موقع عالم الكتب لتنزيل كتاب Enhanced Aircraft Platform Availability Through Advanced Maintenance Concepts and Technologies رابط مباشر لتنزيل كتاب Enhanced Aircraft Platform Availability Through Advanced Maintenance Concepts and Technologies 
|
|