Admin مدير المنتدى


عدد المساهمات : 18726 التقييم : 34712 تاريخ التسجيل : 01/07/2009 الدولة : مصر العمل : مدير منتدى هندسة الإنتاج والتصميم الميكانيكى
 | موضوع: كتاب Shigley’s Mechanical Engineering Design - Tenth Edition الخميس 03 أغسطس 2023, 1:51 am | |
| 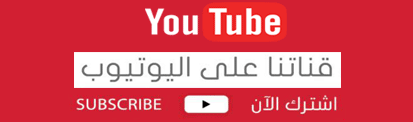
أخواني في الله أحضرت لكم كتاب Shigley’s Mechanical Engineering Design Tenth Edition Richard G. Budynas Professor Emeritus, Kate Gleason College of Engineering, Rochester Institute of Technology J. Keith Nisbett Associate Professor of Mechanical Engineering, Missouri University of Science and Technology
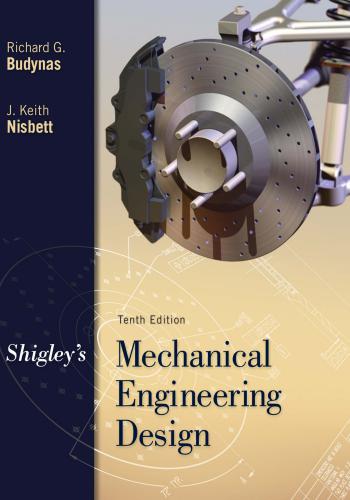 و المحتوى كما يلي :
Brief Contents Preface xv Part 1 Basics 2 1 Introduction to Mechanical Engineering Design 3 2 Materials 41 3 Load and Stress Analysis 85 4 Deflection and Stiffness 161 Part 2 Failure Prevention 226 5 Failures Resulting from Static Loading 227 6 Fatigue Failure Resulting from Variable Loading 273 Part 3 Design of Mechanical Elements 350 7 Shafts and Shaft Components 351 8 Screws, Fasteners, and the Design of Nonpermanent Joints 401 9 Welding, Bonding, and the Design of Permanent Joints 467 10 Mechanical Springs 509 11 Rolling-Contact Bearings 561 12 Lubrication and Journal Bearings 609 13 Gears—General 665 14 Spur and Helical Gears 725 15 Bevel and Worm Gears 777 16 Clutches, Brakes, Couplings, and Flywheels 817 17 Flexible Mechanical Elements 871 18 Power Transmission Case Study 925Brief Contents ix Part 4 Special Topics 944 19 Finite-Element Analysis 945 20 Geometric Dimensioning and Tolerancing 969 Appendixes A Useful Tables 1011 B Answers to Selected Problems 1067 Index 1073x Contents Preface xv Part 1 Basics 2 1 Introduction to Mechanical Engineering Design 3 1–1 Design 4 1–2 Mechanical Engineering Design 5 1–3 Phases and Interactions of the Design Process 5 1–4 Design Tools and Resources 8 1–5 The Design Engineer’s Professional Responsibilities 10 1–6 Standards and Codes 12 1–7 Economics 13 1–8 Safety and Product Liability 15 1–9 Stress and Strength 16 1–10 Uncertainty 16 1–11 Design Factor and Factor of Safety 18 1–12 Reliability and Probability of Failure 20 1–13 Relating the Design Factor to Reliability 24 1–14 Dimensions and Tolerances 27 1–15 Units 31 1–16 Calculations and Significant Figures 32 1–17 Design Topic Interdependencies 33 1–18 Power Transmission Case Study Specifications 34 Problems 36 2 Materials 41 2–1 Material Strength and Stiffness 42 2–2 The Statistical Significance of Material Properties 46 2–3 Strength and Cold Work 49 2–4 Hardness 52 2–5 Impact Properties 53 2–6 Temperature Effects 54 2–7 Numbering Systems 56 2–8 Sand Casting 57 2–9 Shell Molding 57 2–10 Investment Casting 58 2–11 Powder-Metallurgy Process 58 2–12 Hot-Working Processes 58 2–13 Cold-Working Processes 59 2–14 The Heat Treatment of Steel 60 2–15 Alloy Steels 62 2–16 Corrosion-Resistant Steels 64 2–17 Casting Materials 65 2–18 Nonferrous Metals 67 2–19 Plastics 70 2–20 Composite Materials 71 2–21 Materials Selection 72 Problems 79 3 Load and Stress Analysis 85 3–1 Equilibrium and Free-Body Diagrams 86 3–2 Shear Force and Bending Moments in Beams 89 3–3 Singularity Functions 91 3–4 Stress 93 3–5 Cartesian Stress Components 93 3–6 Mohr’s Circle for Plane Stress 94 3–7 General Three-Dimensional Stress 100 3–8 Elastic Strain 101 3–9 Uniformly Distributed Stresses 102 3–10 Normal Stresses for Beams in Bending 103 3–11 Shear Stresses for Beams in Bending 108 3–12 Torsion 115 3–13 Stress Concentration 124Contents xi 3–14 Stresses in Pressurized Cylinders 127 3–15 Stresses in Rotating Rings 129 3–16 Press and Shrink Fits 130 3–17 Temperature Effects 131 3–18 Curved Beams in Bending 132 3–19 Contact Stresses 136 3–20 Summary 140 Problems 141 4 Deflection and Stiffness 161 4–1 Spring Rates 162 4–2 Tension, Compression, and Torsion 163 4–3 Deflection Due to Bending 164 4–4 Beam Deflection Methods 166 4–5 Beam Deflections by Superposition 167 4–6 Beam Deflections by Singularity Functions 170 4–7 Strain Energy 176 4–8 Castigliano’s Theorem 178 4–9 Deflection of Curved Members 183 4–10 Statically Indeterminate Problems 189 4–11 Compression Members—General 195 4–12 Long Columns with Central Loading 198 4–13 Intermediate-Length Columns with Central Loading 198 4–14 Columns with Eccentric Loading 198 4–15 Struts or Short Compression Members 202 4–16 Elastic Stability 204 4–17 Shock and Impact 205 Problems 206 Part 2 Failure Prevention 226 5 Failures Resulting from Static Loading 227 5–1 Static Strength 230 5–2 Stress Concentration 231 5–3 Failure Theories 233 5–4 Maximum-Shear-Stress Theory for Ductile Materials 233 5–5 Distortion-Energy Theory for Ductile Materials 235 5–6 Coulomb-Mohr Theory for Ductile Materials 242 5–7 Failure of Ductile Materials Summary 245 5–8 Maximum-Normal-Stress Theory for Brittle Materials 249 5–9 Modifications of the Mohr Theory for Brittle Materials 249 5–10 Failure of Brittle Materials Summary 252 5–11 Selection of Failure Criteria 252 5–12 Introduction to Fracture Mechanics 253 5–13 Important Design Equations 262 Problems 264 6 Fatigue Failure Resulting from Variable Loading 273 6–1 Introduction to Fatigue in Metals 274 6–2 Approach to Fatigue Failure in Analysis and Design 280 6–3 Fatigue-Life Methods 281 6–4 The Stress-Life Method 281 6–5 The Strain-Life Method 284 6–6 The Linear-Elastic Fracture Mechanics Method 286 6–7 The Endurance Limit 290 6–8 Fatigue Strength 291 6–9 Endurance Limit Modifying Factors 294 6–10 Stress Concentration and Notch Sensitivity 303 6–11 Characterizing Fluctuating Stresses 308 6–12 Fatigue Failure Criteria for Fluctuating Stress 311 6–13 Torsional Fatigue Strength under Fluctuating Stresses 325 6–14 Combinations of Loading Modes 325 6–15 Varying, Fluctuating Stresses; Cumulative Fatigue Damage 329 6–16 Surface Fatigue Strength 335 6–17 Road Maps and Important Design Equations for the Stress-Life Method 338 Problems 341xii Mechanical Engineering Design Part 3 Design of Mechanical Elements 350 7 Shafts and Shaft Components 351 7–1 Introduction 352 7–2 Shaft Materials 352 7–3 Shaft Layout 353 7–4 Shaft Design for Stress 358 7–5 Deflection Considerations 371 7–6 Critical Speeds for Shafts 375 7–7 Miscellaneous Shaft Components 380 7–8 Limits and Fits 387 Problems 392 8 Screws, Fasteners, and the Design of Nonpermanent Joints 401 8–1 Thread Standards and Definitions 402 8–2 The Mechanics of Power Screws 406 8–3 Threaded Fasteners 414 8–4 Joints—Fastener Stiffness 416 8–5 Joints—Member Stiffness 419 8–6 Bolt Strength 424 8–7 Tension Joints—The External Load 427 8–8 Relating Bolt Torque to Bolt Tension 429 8–9 Statically Loaded Tension Joint with Preload 432 8–10 Gasketed Joints 436 8–11 Fatigue Loading of Tension Joints 436 8–12 Bolted and Riveted Joints Loaded in Shear 443 Problems 451 9 Welding, Bonding, and the Design of Permanent Joints 467 9–1 Welding Symbols 468 9–2 Butt and Fillet Welds 470 9–3 Stresses in Welded Joints in Torsion 474 9–4 Stresses in Welded Joints in Bending 479 9–5 The Strength of Welded Joints 481 9–6 Static Loading 484 9–7 Fatigue Loading 488 9–8 Resistance Welding 490 9–9 Adhesive Bonding 490 Problems 499 10 Mechanical Springs 509 10–1 Stresses in Helical Springs 510 10–2 The Curvature Effect 511 10–3 Deflection of Helical Springs 512 10–4 Compression Springs 512 10–5 Stability 514 10–6 Spring Materials 515 10–7 Helical Compression Spring Design for Static Service 520 10–8 Critical Frequency of Helical Springs 526 10–9 Fatigue Loading of Helical Compression Springs 528 10–10 Helical Compression Spring Design for Fatigue Loading 531 10–11 Extension Springs 534 10–12 Helical Coil Torsion Springs 542 10–13 Belleville Springs 549 10–14 Miscellaneous Springs 550 10–15 Summary 552 Problems 552 11 Rolling-Contact Bearings 561 11–1 Bearing Types 562 11–2 Bearing Life 565 11–3 Bearing Load Life at Rated Reliability 566 11–4 Reliability versus Life—The Weibull Distribution 568 11–5 Relating Load, Life, and Reliability 569 11–6 Combined Radial and Thrust Loading 571 11–7 Variable Loading 577 11–8 Selection of Ball and Cylindrical Roller Bearings 580 11–9 Selection of Tapered Roller Bearings 583 11–10 Design Assessment for Selected RollingContact Bearings 592Contents xiii 11–11 Lubrication 596 11–12 Mounting and Enclosure 597 Problems 601 12 Lubrication and Journal Bearings 609 12–1 Types of Lubrication 610 12–2 Viscosity 611 12–3 Petroff’s Equation 613 12–4 Stable Lubrication 615 12–5 Thick-Film Lubrication 616 12–6 Hydrodynamic Theory 617 12–7 Design Considerations 621 12–8 The Relations of the Variables 623 12–9 Steady-State Conditions in Self-Contained Bearings 637 12–10 Clearance 640 12–11 Pressure-Fed Bearings 642 12–12 Loads and Materials 648 12–13 Bearing Types 650 12–14 Thrust Bearings 651 12–15 Boundary-Lubricated Bearings 652 Problems 660 13 Gears—General 665 13–1 Types of Gears 666 13–2 Nomenclature 667 13–3 Conjugate Action 669 13–4 Involute Properties 670 13–5 Fundamentals 670 13–6 Contact Ratio 676 13–7 Interference 677 13–8 The Forming of Gear Teeth 679 13–9 Straight Bevel Gears 682 13–10 Parallel Helical Gears 683 13–11 Worm Gears 687 13–12 Tooth Systems 688 13–13 Gear Trains 690 13–14 Force Analysis—Spur Gearing 697 13–15 Force Analysis—Bevel Gearing 701 13–16 Force Analysis—Helical Gearing 704 13–17 Force Analysis—Worm Gearing 706 Problems 712 14 Spur and Helical Gears 725 14–1 The Lewis Bending Equation 726 14–2 Surface Durability 735 14–3 AGMA Stress Equations 737 14–4 AGMA Strength Equations 739 14–5 Geometry Factors I and J (ZI and YJ) 743 14–6 The Elastic Coefficient C p (ZE) 748 14–7 Dynamic Factor Kv 748 14–8 Overload Factor K o 750 14–9 Surface Condition Factor C f (ZR) 750 14–10 Size Factor K s 751 14–11 Load-Distribution Factor K m (KH) 751 14–12 Hardness-Ratio Factor CH (ZW) 753 14–13 Stress-Cycle Factors YN and ZN 754 14–14 Reliability Factor KR (YZ) 755 14–15 Temperature Factor KT (Yu) 756 14–16 Rim-Thickness Factor KB 756 14–17 Safety Factors SF and SH 757 14–18 Analysis 757 14–19 Design of a Gear Mesh 767 Problems 772 15 Bevel and Worm Gears 777 15–1 Bevel Gearing—General 778 15–2 Bevel-Gear Stresses and Strengths 780 15–3 AGMA Equation Factors 783 15–4 Straight-Bevel Gear Analysis 795 15–5 Design of a Straight-Bevel Gear Mesh 798 15–6 Worm Gearing—AGMA Equation 801 15–7 Worm-Gear Analysis 805 15–8 Designing a Worm-Gear Mesh 809 15–9 Buckingham Wear Load 812 Problems 813 16 Clutches, Brakes, Couplings, and Flywheels 817 16–1 Static Analysis of Clutches and Brakes 819 16–2 Internal Expanding Rim Clutches and Brakes 824xiv Mechanical Engineering Design 16–3 External Contracting Rim Clutches and Brakes 832 16–4 Band-Type Clutches and Brakes 836 16–5 Frictional-Contact Axial Clutches 837 16–6 Disk Brakes 841 16–7 Cone Clutches and Brakes 845 16–8 Energy Considerations 848 16–9 Temperature Rise 849 16–10 Friction Materials 853 16–11 Miscellaneous Clutches and Couplings 856 16–12 Flywheels 858 Problems 863 17 Flexible Mechanical Elements 871 17–1 Belts 872 17–2 Flat- and Round-Belt Drives 875 17–3 V Belts 890 17–4 Timing Belts 898 17–5 Roller Chain 899 17–6 Wire Rope 908 17–7 Flexible Shafts 916 Problems 917 18 Power Transmission Case Study 925 18–1 Design Sequence for Power Transmission 927 18–2 Power and Torque Requirements 928 18–3 Gear Specification 928 18–4 Shaft Layout 935 18–5 Force Analysis 937 18–6 Shaft Material Selection 937 18–7 Shaft Design for Stress 938 18–8 Shaft Design for Deflection 938 18–9 Bearing Selection 939 18–10 Key and Retaining Ring Selection 940 18–11 Final Analysis 943 Problems 943 Part 4 Special Topics 944 19 Finite-Element Analysis 945 19–1 The Finite-Element Method 947 19–2 Element Geometries 949 19–3 The Finite-Element Solution Process 951 19–4 Mesh Generation 954 19–5 Load Application 956 19–6 Boundary Conditions 957 19–7 Modeling Techniques 958 19–8 Thermal Stresses 961 19–9 Critical Buckling Load 961 19–10 Vibration Analysis 963 19–11 Summary 964 Problems 966 20 Geometric Dimensioning and Tolerancing 969 20–1 Dimensioning and Tolerancing Systems 970 20–2 Definition of Geometric Dimensioning and Tolerancing 971 20–3 Datums 976 20–4 Controlling Geometric Tolerances 981 20–5 Geometric Characteristic Definitions 985 20–6 Material Condition Modifiers 994 20–7 Practical Implementation 996 20–8 GD&T in CAD Models 1001 20–9 Glossary of GD&T Terms 1002 Problems 1005 Appendixes A Useful Tables 1011 B Answers to Selected Problems 1067 Index 1073 Axis, defined, 1003 Axle, defined, 352 BB 10 life, 566 Backlash, 668 Bainite, 61 Bairstow, L., 284 Ball bearings, 562–563 Ball bushings, 565 Band-type clutches and brakes, 836–837 Barth, Carl G., 731 Barth equation, 731 Base circle, 670–675 Base pitch, 674 Basic dimension, 975, 983, 1003 Basic Dynamic Load Rating, 566 Basic size (limits and fits), 387–389 Basic static load rating, 572–573 Bauschinger’s theory, 284 Beach marks, 274–275, 278 Beams with asymmetrical sections, 107–108 in bending, normal stresses for, 103–108 in bending, shear stresses for, 108–114 curved beams in bending, 132–136 deflection due to bending, 164–166 deflection methods, 166–167 deflections by singularity functions, 170–176 deflections by superposition, 167–170 shear-force and bending moments in, 89–90 shear stress in rectangular, 109 two-plane bending, 106–107 Bearing characteristic, 615 Bearing characteristic number, See Sommerfeld number Bearing fatigue failure criteria. 565 Bearing film pressure, 616–618, 624, 628, 633–634 Bearing pressure (rope), 911 Bearing housing heat dissipation, 637 Bearing life life measure, 565, 568 rating life, 566 recommendations for various classes of machinery, 575 reliability versus life, 568 Bearing load life at rated reliability, 566–567 Bearings, journal alloy characteristics, 649 boundary-lubricated, 652–660 material choice for, 648–650 thrust bearings, 651–652 types of, 650–651 A Abrasion, 735 Absolute system of units, 31 Absolute tolerance system, 31 Absolute viscosity, 612–613, 625–627 Acme threads, 404–406, 409 Actual mating envelope, 979–980, 1002–1003 Addendum, 668, 688–690, 801, 803 Adhesive bonding, 490–499 joint design, 496–499 stress distributions, 493–496 types of adhesive, 491–492 Admiralty metal, 69 AGMA equation factors allowable bending stress numbers, 739–741, 791–793 allowable contact stress, 742–743, 790–792 bending strength geometry factor, 738, 744–746, 785–786 crowning factor for pitting, 785 dynamic factor, 730, 738, 748, 750, 783–784 elastic coefficient, 736, 738, 748, 749, 790 geometry factors, 743–748, 785–786 hardness-ratio factor, 753–754, 788–789 lengthwise curvature factor for bending strength, 785 load-distribution factor, 738, 751–753, 785 overload factor, 738, 750, 758–759, 783 pitting resistance geometry factor, 738, 743, 746–748, 785–786 reliability factor, 755–756, 789–790 reversed loading, 792 rim-thickness factor, 738, 756–757 safety factors, 757, 783 size factor, 738, 751, 785 stress-cycle factor, 741–742, 754–755, 787–788 surface condition factor, 738, 750 surface-strength geometry factor, 746–748 temperature factor, 756, 788 AGMA gear method bevel gears, 780, 783–794 helical gears, 737–759 spur gears, 737–759 worm gears, 801–806 AGMA quality numbers, 748 AGMA transmission accuracy-level number, 748 Alignment (bearings), 600 Allowable stress numbers (spur gears), 739 Allowance, 28 Alloy cast irons, 66 Alloy steels, 63–64 Alternating and midrange von Mises stresses, 326, 359 Alternating stresses, 274, 308, 311 equivalent reversing stress (Ex. 6–12), 322 Aluminum, 56–57, 67 Aluminum brass, 69 Aluminum bronze, 69 American Bearing Manufacturers Association (ABMA), 11, 565 American Chain Association (ACA), 903 American Gear Manufacturers Association (AGMA), 12, 337, 688, 726, 778 nomenclature, 727–728, 781–782 strength equations, 739–743, 783 stress equations, 737–739, 780, 783 American Institute of Steel Construction (AISC), 12, 481–483 American Iron and Steel Institute (AISI), 12, 56 American National (Unified) thread standard, 402 American Society for Testing and Materials (ASTM), 12, 52, 57, 259 American Society of Mechanical Engineers (ASME), 10, 11–12, 19, 612 American Welding Society (AWS), 12, 468–470 Amplitude ratio (stress), 310 Anaerobic adhesives, 492 Analysis and optimization, 7 Angle of action, 674 Angle of approach, 674 Angle of articulation, 900 Angle of recess, 674 Angle of twist, 115–116, 121 Angularity control, 973–974, 987 Angular-velocity ratio, 669, 872, 898 Annealing, 60–61 Anodizing, 67 Antifriction bearing. See Rolling-contact bearings Arc of action, 676 Arc of approach, 676 Arc of recess, 676 Area principal axes, 107 Arrow side (weld symbol), 469 Ashby, M. F., 73 ASME-elliptic line, 313–314, 316, 318, 325, 340, 361, 439 Associated Spring, 546 Austenitic chromium-nickel steels, 64, 65 Automotive valve-spring surge, 526, 527 Average life (bearings), 566 Axial clutches, 837–840 Axial layout, for shaft components, 355 Axial pitch, 684, 687 1073 Index1074 Mechanical Engineering Design Catalog load rating, rolling-contactbearings, 566 Catastrophic failure, buckling, 204 Centrifugal castings, 58, 679 Centrifugal clutch, 824 Centrifugal force, belts, 876 Centroidal axis columns, 195, 198, 202 curved beams, 132–133 straight beams, 104, 164 Ceramics, 73, 79 Cermet pads, 855 CES Edupack software, 73 Chain dimensioning, 30 Chain drives, 899–907 Chain velocity, 901 Charpy notched-bar test, 53–54 Chordal speed variation, 902 Choudury, M., 421 Chrome-silicon wire, 516, 517 Chrome-vanadium wire, 516, 517 Chromium, 63, 66 Chromium-nickel steels, 64, 65 Circular pad caliper brake, 844–845 Circular runout control, 974, 993–994 Circularity control, 973–974, 985–986 Circular pitch, 667–668, 674, 683–684, 687 Clamshell marks, 274 Clearance, 27 journal bearings, 614, 640–642 preferred fits, 389 spur gears, 668 straight bevel gears, 682, 689 Clearance circle, 668 Close running fit, 389 Closed ends, springs, 512–513 Close-wound extension springs, 536 Clough, R. W., 947, 948 Clutches band-type, 836–837 cone clutches, 845–847 energy considerations, 848–849 external contracting rim, 832–836 friction, 818 frictional-contact axial, 837–840 friction materials, 853–856 internal expanding rim, 824–832 miscellaneous clutches and couplings, 856–857 static analysis of, 819–823 temperature rise, 849–853 torque capacity, 839, 848 uniform pressure, 820, 839–840 uniform wear, 838–839 Codes, 12–13 Coefficient of friction clutches and brakes, 818, 819, 821, 853, 855 flat- and round-belt drives, 876 interference fits, 392 threaded fasteners, 430 journal bearings, 613–615, 630–631, 652 power screws, 407, 413-414 V belt, 892 worm and worm-gears, 707, 709, 802–803 Coefficient of speed fluctuation, 859–860 static analysis of, 819–823 symmetrical pivoted shoe, 834–836 temperature rise, 849–853 wear, 834–835, 838–840 Brass, 68–69 Breakeven points, 14–15 Brinell hardness, 52, 62, 753 Brittle-Coulomb-Mohr (BCM) theory, 249–250 Brittle materials Brittle-Coulomb-Mohr (BCM) theory, 249–250 failure summary, 252 fatigue failure criteria, 322–323 fracture criteria, 233 maximum-normal-stress theory for, 249 modified Mohr (MM) theory, 249, 250–251, 263 Smith-Dolan fatigue criteria, 322–323 stress-concentration factor, static loading, 125–126 Bronze, 68–70 B10 life, 566 Bubble chart, 74, 76, 78–79 Buckingham, E., 335–337 Buckingham (pi) method, 840 Buckingham wear load, 812–813 Burnishing, of gears, 682 Bushing, 610, 650, wear, 655–658 Button pad caliper brake, 844–845 Butt welds, 469, 470–471 C CAD software, 8–9, 946 Calculations and significant figures, 32–33 Caliper brakes, 841–845 Cap screws, 380, 415 Carbon content, 43, 56, 61–65 Cartesian stress components, 93–94 Cartridge brass, 68–69 Case hardening, 62 Case study (power transmission) bearing selection, 939–940 deflection check, 938–939 design for stress, 938 final shaft design, 942–943 gear specification, 931–935 key design, 940–941 problem specification, 34–36, 926–927 shaft layout, 936 speed, torque, and gear ratios, 929–930 Castigliano’s theorem, 178–183 curved beam deflections, 183–189 flat triangular spring deflection, 551 helical spring deflection, 512, 545 statically indeterminate problems, 191–192 Casting alloys, 67 Casting materials, 65–67 Cast irons, 65–67 endurance limits, 291 fatigue test data, 252 minimum strength, 52 numbering system for, 57 stress concentration and, 232 Cast steels, 66–67 Bearings, rolling-contact bearing life, 565–566 boundary dimensions for, 573–574 combined radial and thrust loading, 571–573 lubrication, 596–597 mounting and enclosure, 597–601 parts of, 563 relating load and life at rated reliability, 566–567 relating load and life at other than rated reliability, 568–571 reliability, 593–596 tapered roller bearings. See Tapered roller bearings types of, 562–565 variable loading, 577–580 Bearing stress, 383, 410, 444 Belleville springs, 549–550 Belt drives Flat and round belts, 875–887 Flat metal belts, 887 Timing belts, 898–899 V belts, 890–898 Belts, 872–875 Bending moments in beams, 89–90 Bergsträsser factor, 511 Beryllium bronze, 70 Bevel gears, 666, 701–704 AGMA equation factors, 783–795 AGMA symbols for bevel gear rating equations, 781–782 bevel gearing, general, 778–780 bevel-gear stresses and strengths, 780–783 design of a straight-bevel gear mesh, 798–800 straight-bevel gear analysis, 795–797 Bilateral tolerance, 27 Blake, J. C., 430 Bolt preload, 417, 427, 433–434 Bolts, 414–415, 417. See also Joints relating bolt torque to bolt tension, 429–432 strength, 424–427 Bonus tolerance, 994–995, 1003 Bottom land, 668 Boundary conditions, 957–958 Boundary elements, 958 Boundary-lubricated bearings, 652–660 bushing wear, 655–658 linear sliding wear, 653–655 temperature rise, 658–660 Boundary lubrication, 611, 615, 652–653 Boundary representation (B-rep), 955 Bowman Distribution, 430, 434 Boyd, John, 623–624 Brakes band-type, 836–837 cone, 845–847 disk brakes, 841–845 energy considerations, 848–849 external contracting, 832–836 friction materials, 853–856 internal expanding, 824–832 properties of brake linings, 855 self-energizing/deenergizing, 819Index 1075 Derived median line, 985–986, 1003 Derived median plane, 986, 1003 Derived unit, 31 Design Assessment for Selected RollingContact Bearings, 592–596 Design basics calculations and significant figures, 32–33 case study specifications, 34–36 categories, 230 considerations, 8 design factor/factor of safety, 18–20 dimensions and tolerances, 27–31 economics, 13–15 in general, 4–5 information sources, 9–10 phases and interactions of, 5–8 relating design factor to reliability, 24–27 reliability and probability of failure, 20–23 safety/product liability, 15 standards and codes, 12–13 stress and strength, 16 tools and resources, 8–10 topic interdependencies, 33 uncertainty in, 16–17 units, 31–32 Design engineer communication and, 5, 10–11 professional responsibilities of, 10–12 Design factor, 4, 17–18 Deviation (limits and fits), 387 Diametral pitch, 668 Die castings, 58, 679 Dimensions and tolerances. See also Geometric Dimensioning and Tolerancing choice of, 28–29 terminology of, 27–28 systems of, 31, 970–971 Dimension-series code (ABMA), 574 Direct load, 448 Direct mounting of bearings, 584–585 Direct shear, 103, 176, 510–512 Discrete distributions, 23 Discrete mean, 23 Discrete standard deviation, 23 Discretization errors, 948–949 Disk brakes, 841–846 circular pad caliper, 844–845 uniform pressure, 843–844 uniform wear, 842–843 Disk clutch, 837–838 Displacement, Castigliano’s theorem, 179 Distortion-energy (DE) failure theory, 235–241, 263 Distribution Gaussian (normal), 21 Weibull, 568–569 Double-enveloping worm gearsets, 667 Double-row bearings, 564 Double-threaded screw, 402 Dowel pin, 383 Dowling, M. E., 310 Drawing (tempering), 61–62 Drive pin, 383 Drum brake, 824 Ductile-brittle transition, 53 Ductile (nodular) cast iron, 65–66 Courant, R., 947 Crack growth, 253–255, 287–290 Crack modes and stress intensity factor, 255–259 Creep, 54–55 Critical buckling load, 961–963 Critical frequency of helical springs, 526–528 Critical load, 195 Critical speeds for shafts, 375–380 Critical stress intensity factor, 259–261 Critical unit load, 196 Crowned pulleys, 872, 887 C10 load rating, 566–567, 569–570, 573, 575 Cumulative fatigue damage, 329–335 Curvature effect, 511–512 Curved beams in bending deflections, 183–189 stresses, 132–136 Cylindrical contact, 138–140 Cylindrical roller bearings, 575, 580–583 Cylindrical worm gear. See Singleenveloping worm gearset Cylindricity control, 973–974, 985, 987 D Datsko, Joseph, 50 Datum, 976–981, 1003 Datum axis, 979–980, 993, 1003 Datum feature, 976–980, 996–997, 1003 Datum feature symbol, 980–981 Datum feature simulator, 976–977, 980, 993, 1003 Datum of size, 1003 Datum reference frame, 976–977, 1003 Decision-making, 4–5 Dedendum, 668 Deflection beam deflection methods, 166–167 beam deflections by singularity functions, 170–176 beam deflections by superposition, 167–170 Castigliano’s theorem, 178–189,191–192, 512, 545, 551 columns with eccentric loading, 198–202 compression members, general, 195 deflection due to bending, theory, 164–166 deflection of curved members, 183–189 elastic stability, 204 intermediate-length columns with central loading, 198 long columns with central loading, 195–198 shock and impact, 205–206 spring rates, 162–163 statically indeterminate problems, 189–195 strain energy, 176–178 struts or short compression members, 202–203 tension, compression, and torsion, 163 Deflection considerations, shafts, 371–375 DE-ASME elliptic equation, 361 DE-Gerber equation,361 DE-Goodman equation, 360 DE-Soderberg equation,361 Degrees of freedom (dof’s), 947 Coefficients of variance, 26 Cold forming, 679 Cold rolling, 679 Cold working, 49–51 Cold-working processes, 59–60 Collins, J. A., 335 Columns critical load, 195 with eccentric loading, 198–202 Euler column formula, 195 intermediate-length with central loading, 198 long columns with central loading, 195–198 parabolic formula, 198 secant column formula, 199–200 slenderness ratio, 196 unstable bending, 195 Commercial bronze, 68 Commercial seal, 600 Communication of design (presentation), 7–8 skills, 5, 10–11 Completely reversed stress, 283, 293, 340, 529, 1055 Composite materials, 71–72 Compound gear train, 691–692 Compound reverted gear train, 693 Compression members, 195 struts or short compression members, 202–203 Compression springs. See Helical coil compression springs Compression tests, 44–45 Compressive stress, 93 Computational errors, 948 Computational tools, 8–9 Computer-aided design (CAD) software, 8–9, 946 Computer-aided engineering (CAE), 9 Concentricity control, 974, 990, 993 Concept design, 6–7 Cone angle, 420, 845–846 Cone clutch, 845–847 uniform pressure, 847 uniform wear, 846–847 Conical spring, 551, (Prob. 10–29) 556 Conjugate action, 669 Constant-force spring, 550 Constructive solid geometry (CSG), 955 Contact adhesives, 492 Contact fatigue strength, 336, 742 Contact ratio, 676–677 Contact stresses, 136–140 cylindrical contact, 138–140 spherical contact, 137–138 Continuing education, 11 Continuous probability distributions, 21 Copper-base alloys, 68–70 Corrosion, 302 Corrosion-resistant steels, 64–65 Cost considerations. See Economics Coulomb-Mohr theory for ductile materials, 242–244, 246, 252, 263 Coulomb-Mohr theory for brittle materials. See Brittle-Coulomb-Mohr (BCM) theory Couplings, 856–8571076 Mechanical Engineering Design for threaded elements, 436 for welds, 482 Fazekas, G. A., 844 Feature, GD&T definition of, 973, 1004 Feature control frame, 983–985, 1004 Feature of size, 973, 979–982, 990, 1004 Feature-relating tolerance zone framework (FRTZF), 991–992, 1004 Felt seals, 600 Ferritic chromium steels, 64–65 Field, J., 63 Filler, 71 Fillet welds, 469–470. See also Welds Filling notch, 564 Film pressure, 633–634 Finite element, 948 Finite-element analysis (FEA), 232, 945–965 about, 946–947 boundary conditions, 957–958 critical buckling load, 961–963 element geometries, 949–951 element library, 949 finite-element method, 947–949 finite-element solution process, 951–954 load application, 956–957 mesh generation, 954–956 modeling techniques, 958–961 thermal stresses, 961 types of errors in, 948–949 vibration analysis, 963–964 Finite-element analysis (FEA) programs, 9, 189, 946 Finite-element method, 947–949 Finite-element solution process, 951–954 Finite life, 305 Finite-life region, 282–283 Firbank, T. C., 875 Fit, 28 Fits interference fits, 390–392 preferred limits and fits, 387–390 types of, 389 Fitted bearing, 617 Flat belts, 872–875 Flat-belt drives, 873–890 Flatness control, 973–974, 985–986 Flexible mechanical elements belts, 872–875 flat-and round-belt drives, 873–890 flat metal belts, 887–890 flexible shafts, 916–917 roller chain, 899–907 timing belts, 898–899 V belts, 890–898 wire rope, 908–916 Flexible shafts, 916–917 Flexural endurance limit, 335 Floating caliper brake, 841 Fluctuating simple loading, 339–340 Fluctuating stresses, 274 characterization of, 308–310 combinations of loading modes, 325–329 fatigue failure criteria for, 311–324 torsional fatigue strength under, 325 varying, cumulative fatigue damage, 329–335 Fluid lubrication, 610 Equivalent radial load, 571 Equivalent vonMises stress, 236 Euler column formula, 195, 197 Eutectoid steel, 61 Evaluation, 7 Expanding-ring clutch, 824 Extension springs. See Helical coil extension springs External contracting rim clutches and brakes, 832–836 Extreme-pressures (EP) lubricants, 652 Extrusion, 59, 679 F Face-contact ratio, 687, 743–744 Face-to-face mounting (DF), 599 Face width, 690 Factor of safety, 18 Failure, probability of, 20–23 Failure theories, static loading, 233 brittle materials, 249–252 ductile materials, 233–248 fracture mechanics, 253–262 selection of failure criteria, 252–253 Fasteners, 424–427 stiffness, 416–419 threaded, 414–416 Fatigue failure, defined, 274 Fatigue failure from variable loading characterizing fluctuating stresses, 308–310 combinations of loading modes, 325–329 crack formation and propagation, 275–279 cumulative damage, 329–335 endurance limit, 290–291 endurance limit modifying factors, 294–302 fatigue failure criteria for fluctuating stress, 311–324 fatigue-life methods, 281 fatigue strength, 291–294 fluctuating stresses, 308–324, 325 introduction to fatigue in metals, 274–280 linear-elastic fracture mechanics method, 286–290 road maps and important design equations, 338–341 stages of, 274–277 strain-life method, 284–286 stress concentration and notch sensitivity, 303–308 stress-life method, 281–284 surface fatigue strength, 335–338 torsional fatigue strength under fluctuating stresses, 325 Fatigue limit, 283. See also Endurance limit Fatigue loading of helical compression springs, 528–534 of tension joints, 436–443 of welded joints, 488–489 of wire rope, 912–913 Fatigue problem categories, 325 Fatigue strength, 282, 291–294 Fatigue stress-concentration factor. See also Stress concentration defined, 303–304 application to fluctuating stresses, 310 for gear teeth, 735, 744 Ductile materials Coulomb-Mohr theory for, 242–244, 263 distortion-energy theory for, 235–241, 263 Dowling method for, 310 failure summary, 245–249 maximum-shear-stress theory for, 233–235, 263 selection of failure criteria, 252–253 stress-concentration factor, 125–126, 232 yield criteria, 233 Ductility, 50 Dunkerley’s equation, 378 Duplexing (bearings), 599 Durability (life) correlations, 896 Dynamic loading, stress concentration effect, 126, 303–308 Dynamic viscosity, 612 Dyne, 612 E Eccentricity ratio, 199, 617, 628–630 Economics, 13–15 breakeven points, 14–15 cost estimates, 15 large tolerances, 13–14 standard sizes, 13 Effective arc, 876 Effective slenderness ratio, 514 Effective stress, 236 Efficiency belt drives, 875 screw thread, 408–409 wormgearing, 708, 804, 805 Eigenvalues, 963 Eigenvectors, 963 Elastic coefficient, 736, 738, 748, 749, 790–791 Elastic creep, 875 Elastic instability, 204, 946 Elasticity, modulus of, 43 Elastic limit, 43, 46 Elastic strain, 101–102 Elastohydrodynamic lubrication, 597, 611 Elastomers, 74, 79 Electrolytic plating, 302 Elimination approach, 953 Enclosures (bearings), 600–601 End-condition constant, 196, 514 Endurance limit, 280, 283, 290–291 Endurance limit modifying factors, 294–302 loading factor, 298–299 miscellaneous-effects factor, 301–302 reliability factor, 300–301 size factor, 296–298 surface factor, 295–296 temperature factor, 299–300 Engineering stress and strength, 45 Engineering stress-strain diagrams, 44 Engineers’ Creed (NSPE), 12 Engraver’s brass, 69 Envelope principle, 982, 1004 Epicyclic gear trains, 695 Equilibrium, 86 Equilibrium and free-body diagrams, 86–89 Equivalent bending load, 909, 914 Equivalent diameter, 297Index 1077 extension springs, 534–542 fatigue loading of, 528–531 materials used for, 515–518 maximum allowable torsional stresses for, 518 stability (buckling), 514–515 for static service, 520–526 stresses in. See Helical springs set-removal, 513 Helical coil extension springs, 534–542 ends for, 535 fatigue analysis, 539–542 load-deflection relation, 536–537 maximum allowable stresses for, 537 maximum tensile stress, 535–536 static applications, 537–539 Helical coil torsion springs, 542–549 bending stress, 544 deflection and spring rate, 544–546 end location description, 543–544 fatigue strength, 546–547 static strength, 546 Helical gears, 666, 683–687, 704–706. See also Spur and helical gears, AGMA Helical springs. See also Helical coil extension, compression, or torsion springs critical frequency of, 526–528 the curvature effect, 511–512 deflection of, 512 spring rate, 512 stresses in, 510–511 Helix angle, 407, 683–685 Hertz, H., 136, 139 Hertzian endurance strength, 336–338 Hertzian stresses, 136, 335, 736. See also Contact stresses Hertz theory, 735 Hexagon-head bolt, 415 Hexagon-head screw, 416 Hexagon nuts, 415–416 High-cycle fatigue, 281–283 High-leaded brass, 69 Hobbing, 681 Holding power, 380 Hole basis (limits and fits), 387 Hooke’s law, 43, 65, 101–102 Hoop stress, 128 Hot-working processes, 58–59 Hrennikoff, A., 947 Hydraulic clutches, 824 Hydrodynamic lubrication, 610, 615–617, 651 Hydrostatic lubrication, 611 Hypoid gears, 666, 779 I Idle arc, 876 Impact, 205–206 Impact load, 53 Impact properties, 53–54 Impact value, 53 Inch-pound-second system (ips), 31 Indirect mounting, 584–585 Infinite-life region, 282–283 Influence coefficients, 376 Injection molding, 680 milling, 680 shaping, 680–681 Gear tooth bending, 762, 765, 768, 771 Gear tooth wear, 762, 765, 768, 771 Gear train value, 691 Gear trains, 690–697 Gear wear, 759, 768, 792–793 General three-dimensional stress, 100–101 Generating line, 671 Geometric attributes, 973–974, 1004 Geometric characteristics, 985–994, 1004 Geometric Dimensioning and Tolerancing (GD&T), 28, 970–1005 basic dimension, 975, 983, 1003 definition of, 28, 971 datum, 976–981, 1003 feature control frame, 983–985, 1004 geometric characteristics, 985–994, 1004 glossary of terms, 1002–1005 material condition modifiers, 994–996, 1004 standards, 972 symbolic language, 974–975 tolerance zone, 981–982, 1005 Geometric stress-concentration factor, 125. See also Stress concentration factor Geometry factors, 743–748 Gerber fatigue-failure criterion, 313–315, 326, 340, 360–361, 439, 488, 542, 546 Gerber failure line, 313–314 Gib-head key, 384 Gilding brass, 68 Global instabilities, 204 Goodman fatigue failure criterion, 311, 313–315, 326, 340, 360, 437–439, 488, 531 Goodman failure line, 313–315 Government information sources, 10 Gravitational system of units, 31 Gravity loading, 957 Gray cast iron, 65 Green, I., 421 Griffith, A. A., 254–255 Grip, 417 Grooved pulleys, 872 Grossman, M. A., 63 Guest theory, 233 H Hagen-Poiseuille law, 612 Ham, C. W., 413 Hard-drawn steel spring wire, 515–518 Hardness, 52–53 Hardness-ratio factor, 742, 753–754, 788–789 Harmonic frequencies, 527 Harmonics, 375 Haringx, J. A., 514 Heading, 60 Heat transfer analysis (FEA), 961 Heat treatment of steel, 60–63 Helical coil compression springs, 512–534 critical frequency of, 526–528 deflection of. See Helical springs design for fatigue loading, 531–534 design for static service, 520–526 end-condition constants for, 514 ends, types of, 512–513 Flywheels, 818, 858–863 Foot-pound-second system (fps), 31 Force analysis bevel gearing, 701–704 case study, 937 helical gearing, 704–706 method, 87–89 spur gearing, 697–701 worm gearing, 706–712 Force fit, 389 Forging, 59 Form, in GD&T, 973–974, 983, 985, 1004 Form controls, 985–987 Form cutters, 679 Fracture mechanics, 253–262, 264 crack modes and stress intensity factor, 255–259 fracture toughness, 259–262 quasi-static fracture, 254–255 Fracture toughness, 259–262 Free-body diagrams, 87–88 Free-cutting brass, 69 Free running fit, 389 Frettage corrosion, and flywheels, 302 Frictional-contact axial clutches, 837–840 Friction materials, for brakes and clutches, 853–856 Friction variable, 630 Full bearing, 617 Full-film lubrication, 610, 651 Fundamental contact stress equation, 780 Fundamental deviation (limits and fits), 387 G Gamma function, 568 Gasketed joints, 436 Gaussian (normal) distribution, 21 GD&T. See Geometric Dimensioning and Tolerancing Gear bending strength, 739–741 Gear mesh design, 767–772 Gears, general, 665–712 AGMA factors. See AGMA equation factors conjugate action, 669 contact ratio, 676–677 force analysis, bevel gearing, 701–704 force analysis, helical gearing, 704–706 force analysis, spur gearing, 697–701 force analysis, worm gearing, 706–712 fundamentals, 670–676 gear teeth formation, 679–682 gear trains, 690–697 interference, 677–679 involute properties, 670 nomenclature, 667–668 parallel helical gears, 683–687 straight bevel gears, 682–683 tooth systems, 688–690 types of gears, 666–667 Gear strength spur and helical gears, 739–743 bevel gears, 780, 783, 785, 787–788 Gear teeth formation, 679–682 finishing, 682 hobbing, 6811078 Mechanical Engineering Design lubricant flow, 631–633 lubricant temperature rise, 634–636 Petroff’s equation, 613–615 pressure-fed bearings, 642–648 relations of the variables, 623–637 stable lubrication, 615 steady-state conditions in self-contained bearings, 637–640 thick-film lubrication, 616–617 thrust bearings, 651–652 types of lubrication, 610–611 viscosity, 611–613 Lubrication failure, 735 Lüder lines, 233–234 Lundberg, 139 M Macaulay functions, 86, 90 Machine-screw head styles, 415–416 Magnesium, 68 Magnetic clutches, 824 Major diameter, 402 Malleable cast iron, 66 Manganese, 63–64 Manson, S. S., 333 Manson-Coffin equation, 286, 292 Manson’s method, 333–334 Margin of safety, 25 Marin factors, 295–302 Marin, Joseph, 245 Martensite, 61–62 Martensitic stainless steels, 64 Martin, H. C., 947 Material condition modifiers, 994–996, 1004 Material efficiency coefficient, 76 Material index, 77 Materials. See also specific materials alloy steels, 63–64 casting materials, 65–67 cold-working processes, 59–60 composite materials, 71–72 corrosion-resistant steels, 64–65 families and classes of, 73–74 hardness, 52–53 heat treatment of steel, 60–63 hot-working processes, 58–59 impact properties, 53–54 investment casting, 58 nonferrous metals, 67–70 numbering systems, 56–57 plastics, 70–71 powder-metallurgy process, 58 sand casting, 57 selection of, 72–79 shell molding, 57–58 statistical significance of properties of, 46–49 strength and cold work, 49–51 strength and stiffness, 42–46 temperature effects, 54–55 Materials selection charts, 73–79 Mathematical models, 7 Matrix, 71 Maximum material boundary, 996, 1004 Maximum material condition (MMC), 975, 982, 994–995, 1005 Lewis form factor, 729 Limits, 27, 387–392 Linear damage hypothesis, 577, 579 Linear elastic fracture mechanics (LEFM), 253 Linear-elastic fracture mechanics method, 281, 286–290 Linear sliding wear, 653–655 Linear spring, 162 Line elements, 949 Line of action, 669, 671, 674 Line of contact, 139 Little, R. E., 420 Load and stress analysis Cartesian stress components, 93–94 contact stresses, 136–140 curved beams in bending, 132–136 elastic strain, 101–102 equilibrium and free-body diagrams, 86–89 general three-dimensional stress, 100–101 Mohr’s circle for plane stress, 94–100 normal stresses for beams in bending, 103–108 press and shrink fits, 130–131 shear force and bending moments in beams, 89–90 shear stresses for beams in bending, 108–115 singularity functions, 91–93 stress, 95 stress concentration, 124–127 stresses in pressurized cylinders, 127–129 stresses in rotating rings, 129–130 temperature effects, 131 torsion, 115–124 uniformly distributed stresses, 102–103 Load application, 956–957 Load application factors, 576 Load factor, 432–433 Loading factor, 298 Load intensity, 89–90 Load-life-reliability relationship, 562, 570 Load line, 235 Load-sharing ratio, 744 Load-stress factor, 336 Load zone, 585 Location, in GD&T, 973–974, 983, 985, 1004 Location controls, 990–993 Locational clearance fit, 389 Locational interference fit, 389 Logarithmic strain, 44 Loose running fit, 389 Loose-side tension, 876 Low brass, 68–69 Low-contact-ratio (LCR) helical gears, 744 Low-cycle fatigue, 281, 283 Lower deviation (limits and fits), 387 Low-leaded brass, 69 L10 life, 566 Lubrication, of roller bearings, 596–597 Lubrication and journal bearings bearing types, 650–651 boundary-lubricated bearings, 652–660 clearance, 640–642 design considerations, 621–623 hydrodynamic theory, 617–621 loads and materials, 648–650 Interference fits, 27–28, 389–392 gear teeth, 677–679 of stress and strength, 25–26 Internal expanding rim clutches and brakes, 824–832 drum torque, 827 shoe forces, 826–829 shoe geometry, 824–825 shoe pressure distribution, 825–826 Internal friction theory, 242 Internal gear, 674 Internal-shoe brake, 824 International System of Units (SI), 32 International tolerance (IT) grade numbers (limits and fits), 387 Internet information sources, 10 Interpolation equation for lubrication charts, 636–637 Invention of the concept, 6–7 Investment casting, 58, 679 Involute helicoid, 683 Involute profile, 669 Involute properties, 670 Isotropic materials, 72 IT numbers (limits and fits), 387 Ito, Y., 419–420 Izod notched-bar test, 53–54 J J. B. Johnson formula, 198, 201, 410 Joerres, R. E., 517 Joints, bolted and riveted bolted and riveted joints loaded in shear, 443–451 fastener stiffness, 416–419 fatigue loading of tension joints, 436–443 gasketed, 436 member stiffness, 419–424 shear joints with eccentric loading, 447 statically loaded tension joint with preload, 432–435 tension joints with external loads, 427–429 Jominy test, 63 Journal bearing, 622–623 K Karelitz, G. B., 637–638 Keys and keyways, 365, 382–386 Kinematic viscosity, 612 Kips, 31 Kurtz, H. J., 430 L Labyrinth seal, 601 Laminates, 72 Landgraf, R. W., 284 Langer criterion, 314–315 Lang-lay ropes, 908 Lap joints, 493, 496, 497 Lead, 402 Least Material Boundary (LMB), 975, 996, 1004 Least Material Condition (LMC), 975, 982, 994–995, 1004 Leibensperger, R. L., 597 Lewis, Wilfred, 726 Lewis bending equation, 726–735Index 1079 Perpendicularity control, 973–974, 987–988 Peterson, R. E., 232 Petroff’s equation, 613–615 Phosphor bronze, 69 Phosphor-bronze wire, 517 Piecewise-continuous periodic loading cycle, 577–578 Pilkey, W. D., 384 Pillow-block bearings, 637 Pinion, 667 Pinion cutter, 680 Pinion tooth bending, 762, 764, 768, 770 Pinion tooth wear, 762, 765, 768, 771 Pins, 382–383 Pitch, 402, 404 Pitch circle, 667, 669, 673 Pitch diameter, 402, 667, 682, 687–688 Pitch length, 892 Pitch-line velocity, 699, 784 Pitch point, 669, 671 Pitch radius, 669 Pitting, 335, 735 Pitting resistance, AGMA stress equation, 737–738 Pitting-resistance geometry factor, 746–748 Plain end springs, 512 Plane of analysis, 234 Plane slider bearing, 618 Plane stress, 94–100, 234 Mohr’s circle shear convention, 96–100 transformation equations, 94 Planetary gear trains, 695, 696 Planet carrier (arm), 695, 696 Planet gears, 695 Plastics, 70–71 Pneumatic clutches, 824 Poise (P), 612 Poisson’s ratio, 72, 102 Polymers, 73–74, 79 Poritsky, 139 Position control, 974, 990–992 Positive-contact clutch, 856–857 Potential energy, 176–178, 206 Pound-force (lbf), 31 Powder-metallurgy process, 58, 650, 679 Power screws, 406–414 Power transmission case study about, 926 bearing selection, 928, 939–940 deflection check, 938 design for stress, 938 design sequence for power transmission, 927–928 final analysis, 928, 943 force analysis, 927, 937 gear specification, 927, 928–935 key and retaining ring selection, 928, 940–942 key design, 940 power and torque requirements, 927, 928 problem specification, 926–927 shaft design for deflection, 928, 938–939 shaft design for stress, 927, 938 shaft layout, 927, 935–937 shaft material selection, 927, 937 specifications, 926–927 speed, torque, and gear ratios, 929–930 Muntz metal, 69 Music wire, 515–518 N Natural frequency, 75, 527, 963 Naval brass, 69 Needle bearings, 564, 565 Neuber constant, 304 Neuber equation, 304 Neutral axis, 103–104, 132 Neutral plane, 104 Newmark, N. M., 947 Newtonian fluids, 612 Newton (N), 32 Nickel, 63, 66 Nodes, 947 Nodular cast iron, 65–66 Noise, vibration and harshness (NVH), 491 Nominal mean stress method, 310 Nominal size, 27 Nominal stresses and strengths, 45 Nonferrous metals, 67–70 Nonlinear softening spring, 163 Nonlinear stiffening spring, 162 Normal circular pitch, 684 Normal diametral pitch, 684 Normalizing, 60–61 Normal stress, 93 Norris, C. H., 472 Notched-bar tests, 53–54 Notch sensitivity, 303–304 Numbering systems, 56–57 Nuts, 415–416, 427 O Octahedral shear stresses, 238 Octahedral-shear-stress theory, 237–238 Offset method, 43 Oil flow, 635, 642 Oiliness agents, 652 Oil-tempered wire, 516 Opening crack propagation mode, 255 Orientation, in GD&T, 973–974, 985, 1004 Orientation controls, 987–988 Osgood, C. C., 420 Other side (weld symbol), 469 Overconstrained system, 189 Overload factors, 738, 750, 758–759, 783 Overload release clutch, 856–857 Overrunning clutch or coupling, 857 P Palmgren-Miner cycle-ratio summation rule, 330–333, 335 Parabolic formula, 198 Parallel-axis theorem, 105, 475 Parallel helical gears, 683–687 Paris equation, 288 Parallelism control, 973–974, 987 Partial bearing, 617 Partitioning approach, 953 Pattern-locating Tolerance Zone Framework (PLTZF), 991–992, 1005 Pearlite, 61 Pedestal bearings, 637 Peel stresses, 496, 498 Performance factors, 622 Permanent-mold casting, 679 Maximum-normal-stress theory for brittle materials, 249 Maximum-shear-stress theory (MSS), 233–235, 245, 252, 263 Maxwell’s reciprocity theorem, 376 McHenry, D., 947 McKee, S. A., 615 McKee, T. R., 615 McKee abscissa, 615 Mean coil diameter, 510 Mechanical efficiency, 805 Mechanical springs. See Springs Median life, 566 Medium drive fit, 389 Mesh, 954 Mesh density, 954 Mesh generation, 954–956 fully automatic, 955 manual, 954–955 semiautomatic, 955 Mesh refinement, 954 Metal-mold castings, 58 Metals, 73, 79 nonferrous, 67–70 Metals Handbook (ASM), 277 Metal spraying, 302 Metric fastener specifications, 403–404, 427 Milling, 680 Mindlin, 139 Miner’s rule, 330–333 Minimum film thickness, 616–617, 629 Minimum life, 566 Minor diameter, 402 Misalignment, 371, 564, 599, 600 Miscellaneous-effects factor, 301–302 Mises-Hencky theory, 237 Mises stresses, 325, 359–360 Mixed-film lubrication, 652–653 Modal analysis, 963–964 Mode I, plane strain fracture toughness, 259 Modeling techniques, 958–961 Modern Steels and Their Properties Handbook, 63 Modified Goodman diagram, 311–312 Modified Goodman failure line, 313–315 Modified Goodman fatigue failure criterion. See Goodman fatigue failure criterion Modified Mohr (MM) theory, 249–252, 263 Module, 668 Modulus of elasticity, 43, 72, 74–76, 101, 1015, 1054 Modulus of elasticity of wire rope, 908 Modulus of resilience, 46 Modulus of rigidity, 45, 102, 1015 Modulus of rupture, 45 Modulus of toughness, 46 Mohr’s circle for plane stress, 94–100 Mohr theory of failure, 242, 249–250 Molded-asbestos linings and pads, 855 Molybdenum, 64, 66 Moment connection, 474 Moment load (secondary shear), 448 Monte Carlo computer simulations, 31 Multiple of rating life, 567 Multiple-threaded product, 402, 805 Multipoint constraint equations, 9581080 Mechanical Engineering Design supporting axial loads, 355 torque transmission provisions, 355–357 Shafts and shaft components about, 352 bearings, 571 couplings, 857 critical speeds for shafts, 375–380 defined, 352 deflection considerations, 371–375 flexible, 916–917 keys and pins, 382–385 layout, 353–358 limits and fits, 387–392 materials for, 352–353 retaining rings, 386 setscrews, 380–382 shaft design for stress, 358–371 Shaping, 680–681 Shear-energy theory, 237 Shear force in beams, 89–90 Shear-lag model, 493, 497 Shear loaded bolted and riveted joints, 443–451 Shear modulus, 45, 102 Shear stress-correction factor, 511 Shear yield strength, 234, 239, 515, 517 Sheaves, 872 Shell molding, 57–58, 679 Shock, 205–206 Shot peening, 301, 528, 762 Shoulders, 353–355, 364–365, 573–574, 596, 598 Shrink fits, 130–131 Significant figures, 32–33 Silicon, 64 Silicon bronze, 69 Sines failure criterion, 528, 531 Single-enveloping (cylindrical) worm gearset, 667, 801. See also Worm gears Single-row bearing, 563–564 Singularity functions, 86, 91–93, 170–176 Sintered-metal pads, 855 Size factor, 296–298, 751, 785 Slenderness ratio, 196, 203 Sliding fit, 388, 389 Sliding mode, 255 Sliding velocity, 708–709 Slug, 31 Smith-Dolan locus, 322–323 Smith, G. M., 527 Smith, James O., 325 Smith-Liu, 139 S-N diagram. See Strength-life diagram Snug-tight condition, 429 Society of Automotive Engineers (SAE), 11, 56 Society of Manufacturing Engineers (SME), 11 Socket setscrews, 381 Soderberg line, 313–314, 361 Software CAD, 8–9 CES Edupack, 73 engineering-based, 9 FEA programs, 189, 946, 965 non-engineering-specific, 9 Solid elements, 949 Residual stress method, 310 Resilience, 46 Resistance welding, 490 Retaining rings, 365, 386, 598, 941 Reynolds equation, 621, 623–624 Reynolds, Osborne, 617–618 Right-hand rule, threads, 402 Rigid elements, 958 Rim-thickness factor, 756–757 Ring gear, 674, 696 Rivet joint, 443–445 Roark’s Formulas for Stress and Strain, 167 Rockwell hardness, 52 Roller chain, 899–907 Rolling-contact bearings. See Bearings, rolling-contact Roll threading, 60 Rolovic, R. D., 232 Root diameter, 402 Rotary fatigue, 335 Rotating-beam test, 282, 290 Rotating rings, stresses in, 129–130 Rotation factor, 571, 573 Round-belt drives, 872, 875–882 Rule #1, 982, 1005 Runout control, 974, 993–994 Russell, Burdsall & Ward Inc., 433 Ryan, D. G., 413 S Safety, 12, 15, 18–20 Saint-Venant’s principle, 956 Salakian, A. G., 472 Samónov, C., 514 Sand casting, 57, 679 Saybolt Universal viscosity (SUV), 612 Scoring, 735 Screws machine screws, 415–416 power screws, 406–414 self-locking, 408 thread standards and definitions, 402–406 Sealants. See Adhesive bonding Seals for bearings, 600–601 Seam welding, 490 Secant column formula, 199–200 Secondary shear, 448, 474 Section modulus, 104 Self-acting (self-locking) phenomenon, 821 Self-adaptive mesh refinement, 955 Self-aligning bearings, 563, 564, 573, 600 Self-contained bearings, 637–638 Self-deenergizing brake shoe, 819 Self-energizing brake shoe, 819 Self-locking screw, 408 Series system, 24 Set removal, 513 Setscrews, 380–382 Shaft basis (limits and fits), 388 Shaft design for stress, 358–371 critical locations, 358–359 estimating stress concentrations, 364–365 shaft stresses, 359–364 Shaft layout, 353–358 assembly and disassembly, 357–358 axial, 355 Preload (bolts), 417, 427, 433–434 Preloading (bearings), 600 Presentation, 7–8 Presetting, 513 Press and shrink fits, 130–131, 357 Pressure angle, 671, 688, 690 Pressure-fed bearings, 642–648 Pressure line, 671 Pressure-sensitive adhesives, 492 Pressurized cylinders, stresses in, 127–129 Pretension, bolt preload, 417, 427, 433–434 Primary shear, 448, 474, 479 Principal directions, 95, 100 Principal second-area moments, 107 Principal stresses, 95, 100–101 Probability density function (PDF), 21 Probability of failure, 20–24 Problem definition, 6, 11 Problem-solving, 4–5, 11 Product liability, 15 Professional societies, 10, 11 Profile controls, 988–990 Profile of a line, 974, 988 Profile of a surface, 974, 988 Proof load, 424 Proof strength, 424, 433 Propagation of dispersion, 24 Propagation of error, 24 Propagation of uncertainty, 24 Proportional limit, 43 Puck pad caliper brake, 844–845 Pulley correction factor, 879–880, 882 Punch-press torque demand, 861–862 Pure compression, 102 Pure shear, 102 Pure tension, 102 Q Quality numbers (AGMA), 748, 750 Quasi-static fracture, 254–255 Quenching, 61 R R. R. Moore high-speed rotating-beam machine, 282 Rack, 674 Rack cutter, 680 Radial clearance, 27, 614, 616, 640 Radial clearance ratio, 614 Radius of gyration, 108 Raimondi, Albert A., 623–624 Raimondi-Boyd analysis, 623–624, 628–629, 632–634, 636, 637 Rain-flow counting technique, 330 Rate of shear, 612 Rating life, 566–567 Rayleigh’s model for lumped masses, 375 Red brass, 68–69 Redundant supports, 189 Regardless of feature size (RFS), 995, 1005 Regular lay, 908 Relatively brittle condition, 254 Reliability, 4, 20, 24–26 Reliability factors, 296, 300–301, 755–756, 789–790 Reliability method of design, 20, 24 Repeated stresses, 274, 309Index 1081 stress-concentration factor, 125 techniques for reducing, 364 Stress-concentration factor, 125, 231–232. See also Stress concentration Stress-correction factor, 745 Stress-cycle factor, 754–755, 787–788 Stresses, 16, 44, 93 Cartesian stress components, 93–94 contact stresses, 136–140 general three-dimensional, 100–101 normal stresses for beams in bending, 103–108 normal stresses for curved beams in bending, 132–136 in pressurized cylinders, 127–129 in rotating rings, 129–130 shear stresses for beams in bending, 108–115 shear stresses for torsion, 115–116 stress concentration, 124–127
كلمة سر فك الضغط : books-world.net The Unzip Password : books-world.net أتمنى أن تستفيدوا من محتوى الموضوع وأن ينال إعجابكم رابط من موقع عالم الكتب لتنزيل كتاب Shigley’s Mechanical Engineering Design - Tenth Edition رابط مباشر لتنزيل كتاب Shigley’s Mechanical Engineering Design - Tenth Edition 
|
|