Admin مدير المنتدى


عدد المساهمات : 18745 التقييم : 34763 تاريخ التسجيل : 01/07/2009 الدولة : مصر العمل : مدير منتدى هندسة الإنتاج والتصميم الميكانيكى
 | موضوع: كتاب Momentum, Heat, and Mass Transfer Fundamentals الجمعة 10 يوليو 2020, 1:54 am | |
| 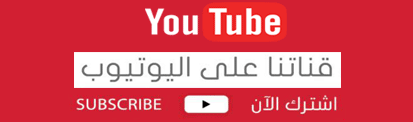
HDF أخوانى فى الله أحضرت لكم كتاب Momentum, Heat, and Mass Transfer Fundamentals David P Kessler Robert A. Greenkorn Purdue University West Lafayette, Indiana M A R C E L H MARCEL DEKKER , INC . NEW YORK * BASEL D E K K E RTHUMB INDEX
 و المحتوى كما يلي :
CONTENTS XI 1 ESSENTIALS 1 1.6.2 Types of derivatives 63 2 THE MASS BALANCES 73 2.1.1 The macroscopic total mass balance 74 2.1.2 The macroscopic species mass balance 2.2.1 The microscopic total mass balance (continuity equation ) 2.2.2 The microscopic species mass balance 3 THE ENERGY BALANCES 113 3.1.2 The macroscopic total energy balance 114 3.1.3 The macroscopic mechanical energy balance 3.1.4 The macroscopic thermal energy balance 3.2.1 The microscopic total energy balance 3.2.2 The microscopic mechanical energy balance 3.2.3 The microscopic thermal energy balance 4 THE MOMENTUM BALANCES 169 4.1 The Macroscopic Momentum Balance 4.2 The Microscopic Momentum Balance 4.3 Summary of Balance Equations and Constitutive Relationships 5 APPLICATION OF DIMENSIONAL ANALYSIS 211 6 MOMENTUM TRANSFER IN FLUIDS Table 6.3-1 Elementary plane flows 6.7 Drag Coefficients Table 6.7.2-1 Properties of pipe Figure 6.7.2-3 Moody friction factor chart vnThumb Index a 7 HEAT TRANSFER MODELS 517 Table 7.2.1-1 Components of Fourier Equation 530 7.2.4 One-dimensional steady-state conduction in rectangular coordinates 7.2.5 One-dimensional steady-state conduction in cylindrical coordinates 72.6 One-dimensional steady-state conduction in spherical coordinates 7.2.8 One-dimensional unsteady-state conduction Semi-infinite slab Finite slab Infinite cylinder and sphere 7.2.9 Multi-dimensional unsteady-state conduction 7.3.2 Heat transfer coefficients 7.4 Conduction and Convection in Series Heisler charts 7.5 Radiation Heat Transfer Models Reciprocity relation Summation rule 7.7.3 NTU method for design of heat exchangers 7.7.4 F-factor method for design of heat exchangers 822 8 MASS TRANSFER MODELS 843 Table 8.2.3-1 Equivalent forms of Fick’s Law 8.3 Convective Mass Transfer Models Height of transfer unit models 8.7 Design of Mass Transfer Columns 8.8 Mass Transfer with Chemical Reaction APPENDIX A: VECTOR AND TENSOR OPERATIONS APPENDIX C: NOMENCLATURE INDEX 1009TABLE OF CONTENTS Preface Thumb Index 1 ESSENTIALS 1 1.1 Models 1 Figure 1.1-1 Modeling the weather 1 Figure 1.1-2 A poor model of the weather 1.1.1 Mathematical models and the real world 1.1.2 Scale of the model 1.2 The Entity Balance Example 1.2-1 An entity balance 1.2.1 Conserved quantities 1.2.2 Steady-state processes 1.3 The Continuum Assumption Figure 1.3-1 Breakdown of continuum assumption 1.4 Fluid Behavior 1.4.1 Laminar and turbulent flow Figure 1.4.1-1 Injection of dye in pipe flow 1.4.2 Newtonian fluids Figure 1 ,4.2-1 Shear between layers of fluid Figure 1.4.2-2 Momentum transfer between layers of fluid Figure 1.4.2-3 Sign convention for momentum flux between layers of fluid Figure 1.4.2-4 Sign convention for shear stress on surface layers of fluid Table 1.4.2-1 Summary of sign convention for stress/momentum flux tensor Figure 1.4.2-5 Migration of momentum by molecular motion Figure 1.4.2-6 Viscosity of common fluids Example 1.4.2-1 Flow of fluids between fixed parallel plates 1.4.3 Complex fluids Figure 1.4,3-1 Complex fluids Figure 1.4.3-2 Mechanical analog of viscoelasticity xixu Table of Contents 1,4.4 Compressible vs. incompressible flows 1.5 Averages 1.5.1 General conce Example /. Figure 1.5.1-1 Time-average speed for travel between two points Figure 1.5.1-2 Distance-average speed for travel between two points 1.5.2 Velocity averages Area-averaged velocity Example 1.5.2-1 Area-averaged velocity for laminar pipe flow Figure 1.5.2-1 Velocity profile Time-averaged velocity Example 1.5.2-2 Time-averaged velocity for turbulent flow Example /.5.2-3 Area-average of time-averaged velocity for turbulent pipe flow 1.5.3 Tern perature averages Example 1.5.3-1 Area-average temperature vs. bulk temperature Example 1.5.3-2 Bulk temperature for quadratic temperature profile, laminar pipe flow 1.5.4 Concentration averages Example 1.5.4-1 Bulk concentration 1.5.5 Arithmetic, logarithmic, and geometric means Example 1.5.5-1 Case examples of logarithmic mean Example 1.5.5-2 Approximation of logarithmic mean by arithmetic mean 1.6 Scalars, Vectors, Tensors and Coordinate Systems 1.6.1 The viscous stress tensor Components of the viscous stress tensor Figure 1.6.1-1 (a) Vectors associated by a particular viscous stress tensor with the direction of the rectangular Cartesian axes Figure 1.6.1-1 (b) Vector associated with the 3-direction decomposed into its components 1.6.2 Types of derivatives Partial derivative jnt of average 33 5.1-1 Time-average vr distance-average speed Total derivative 64 Substantial derivative, material derivative, derivative following the motion 64 Example 1.6.2-1 Rate of change of pollen density 1.6.3 Transport theorem 66Table of Contents xm Figure 1.6.3-1 Motion of continuum 67 Chapter 1 Problems 69 2 THE MASS BALANCES 7 3 2.1 The Macroscopic Mass Balances Figure 2.1-1 System for mass balances 2.1.1 The macroscopic total mass balance Accumulation of mass Input and output of mass Simplified forms of the macroscopic total mass balance Example 2.1.1-l Mass balance on a surge tank Figure 2.1.1-1 Surge tank Example 2././-2 Volumetric flow rate offluid in laminar flow in circular pipe Example 2.1.1-5 Air storage tank Example 2./.1-4 Water manifold 2.1.2 The macroscopic species mass balance Generation of mass of a species Accumulation of mass of a species Input and output of mass of a species Example 2.1.2-1 Macroscopic species mass balance with zero-order irreversible reaction Example 2.1.2-2 Macroscopic species mass balance with first-order irreversible reaction Figure 2.1.2-1 Perfectly mixed tank with reaction 2.2 The Microscopic Mass Balances 2.2.1 The microscopic total mass balance (continuity equation) Special cases of the continuity equation Continuity equation in different coordinate systems Table 2.2.1-1 Continuity equation (microscopic total mass balance) in rectangular, cylindrical, and spherical coordinate frames Example 2.2.1-/ Velocity components in two-dimensional steady incompressible flow, rectangular coordinates Example 2.2.1-2 Velocity components in two-dimensional steady incompressible flow, cylindrical coordinates Example 2.2./-3 Compression of air Figure 2.2.1-1 Air compression by piston 2.2.2 The microscopic species mass balance Diffusion Chapter 2 Problems 3 THE ENERGY BALANCES 3.1 The Macroscopic Energy Balances 113 113xiv Table of Contents 3.1.1 Forms of energy 3.1.2 The macroscopic total energy balance Rate of accumulation of energy Rates of input and output of energy Figure 3.1.2-1 Flow work Simplified forms of the macroscopic total energy balance The potential energy term Figure 3.1.2-2 Gravitational field of earth The kinetic energy term The enthalpy term Averages and the macroscopic energy equations Energy balance approximation - turbulent flow Energy balance approximation - laminar flow Steady-state cases of the macroscopic total energy balance Table 3.1.2-1 Qualitative comparison of ranges of enthalpy changes (kcal/mol) for processes involving organic compounds Example 3.1.2-1 Relative magnitudes of mechanical and thermal energy terms with phase change Figure 3.1.2-3 Mechanical energy and thermal energy terms compared for a boiler (I) Example 3.1,2-2 Steam production in a boiler Figure 3.1.2-4 Mechanical and thermal energy terms compared for a boiler (II) Example 3,1.2-3 Temperature rise from conversion of mechanical to thermal energy Figure 3.1.2-5 Water supply system Example 3.1.2-4 Heated tank, steady state in mass and unsteady state in energy Figure 3.1.2-6 Heated tank 3.1.3 The macroscopic mechanical energy balance Example 3.1.3-1 Mechanical energy and pole vaulting Example 3.I.3-2 Calculation of lost work in pipe Figure 3.1.3-1 Pipe system 3.1.4 The macroscopic thermal energy balance 3.2 The Microscopic Energy Balances 3.2.1 The microscopic total energy balance Eulerian forms of the microscopic total energy balance Lagrangian forms of the microscopic total energy balance 3.2.2 The microscopic mechanical energy balance 3.2.3 The microscopic thermal energy balance Chapter 3 Problems 4 THE MOMENTUM BALANCES 169Table of Contents xv 4.1 The Macroscopic Momentum Balance 169 Example 4.I-1 Momentum flux of fluid in laminar flow in circular pipe 173 4.1.1 Types of forces 174 4.1.2 Influence of uniform pressure over entire surface of irregular objects 175 Figure 4.1.2-1 Approximation of solid by prisms Figure 4.1.2-2 Detail of prism 4.1.3 Averages and the momentum equation Momentum balance approximation - turbulent flow Momentum balance approximation - laminar flow Example 4,1.3-1 Force on a nozzle Example 4.1.3-2 Thrust of aircraft engine Example 4.1.3-3 Piping support Example 4.1.3-4 Jet boat Example 4.1.3-5 Horizontal force on tank 4.2 The Microscopic Momentum Balance 4.3 Summary of Balance Equations and Constitutive Relationships Table 4.3-1 Tabulation of balance equations Table 4.3-2 Tabulation of common constitutive relationships 4.4 The Momentum Equation in Non-Inertial Reference Frames Chapter 4 Problems 5 APPLICATION OF DIMENSIONAL ANALYSIS 5.1 Systems of Measurement Example 5./-/ Weight vs. mass; g vs. gc Table 5.1-la Systems of Units Table 5.1-1b Systems of Units Table 5.1-2 SI Prefixes 5.2 Buckingham's Theorem Example 5.2-1 Dimensionless variables for pipe flow 5.2.1 Friction factors and drag coefficients 5.2.2 Shape factors Example 5.2.2-1 Drag force on ship hull Example 5.2.2-2 Deceleration of compressible fluid 5.3 Systematic Analysis of Variables Example 5.3-1 Drag force on a sphere Example 5J -2 Dimensionless groups for flow over a flat plate Example 5.3-3 Consistency of dimensionless groups across system of dimensions Example 5.3-4 Capillary interface height via dimensional analysis 243xvi Table of Contents 5.4 Dimensionless groups and differential models Example 5.4-1 Pipe flow of incompressible fluid with constant viscosity Example 5.4-2 One-dimensional energy transport Example 5.4-3 Mass transport in a binary mixture Example 5.4-4 Extrapolating model results from one category of momentum, heat, or mass transport to another Table 5.4-1 Dimensionless variables Table 5.4-2 Dedimensionalized balance equations Table 5.4-3 Dimensionless numbers 5.5 Similarity, Models and Scaling Example 5.5-1 Drag on immersed body Example 5.5-2 Scale effects Chapter 5 Problems 6 MOMENTUM TRANSFER IN FLUIDS 281 6.1 Fluid Statics 6.1.1 Manometers Example 6.1.1-l Pressure difference using a manometer Figure 6.1.1-1 Measurement of pressure difference with manometer Example 6./. I -2 Pressure difference between tanks Figure 6.1.1-2 Pressure difference between tanks Example 6.1.1-3 Differential manometer Figure 6.1.1-3 Differential manometer 6.2 Description of Flow Fields Figure 6.2-1 Paths between streamlines 6.2.1 Irrotational flow 6.3 Potential Flow 295 Table 6.3-1 Elementary plane flows Table 6.3-2 Superposition of elementary plane flows Example 6.3-1 Flow around a circular cylinder Figure 6.3-1 Flow around circular cylinder Example 6.3-2 Flow of an ideal fluid through a corner Figure 6.3-2 Flow through a comer Example 6.3-3 Flow around a rotating cylinder 6.4 Laminar Flow 314 6.4.1 Laminar flow between infinite parallel plates 315 Figure 6.4.1-1 Steady flow between infinite stationary parallel plates Example 6.4.1-1 Steady flow between infinite parallel plates Figure 6.4.1-2 Flow between infinite parallel plates, top plate moving at VQ 319Table of Contents xvn Figure 6.4.1-3 Velocity profiles for laminar flow of Newtonian fluid between parallel plates with imposed pressure drop, top plate moving at steady velocity Example 6.4.1-2 Flow between infinite rotating concentric cylinders 6.4.2 Laminar flow in a circular pipe Figure 6.4.2-1 Control volume for force balance on fluid in pipe 322 Figure 6.4.2-2 Velocity profile for laminar flow of a Newtonian fluid in a pipe or duct of circular cross-section Figure 6.4.2-3 Shear stress profile for laminar flow of a Newtonian fluid in a pipe or duct of circular cross-section Example 6.42-1 Flow in a capillary viscometer Example 6.42-2 Flow between two concentric cylinders Figure 6.4.2-4 Viscometric flow between cylinders Example 6.42-3 Film flow down a wall Figure 6.4.2-5 Film flow down wall Example 6.42-4 Flow adjacent to a flat plate instantaneously set in motion Figure 6.4.2-6 Flow adjacent to flat plate instantaneously set in motion 6.5 Turbulent Flow Figure 6,5-1 Local velocity in turbulent flow as a function of time Figure 6.5-2 Laminar and time-smoothed turbulent (1/7 power model) velocity profiles in steady pipe flow 6.5.1 Time averaging the equations of change Example 6.5-2 Time averaging of velocity product 6.5.2 The mixing length model Figure 6.5.2-1 Mixing length model Figure 6.5.2-2 Universal velocity distribution Example 6.52-1 Size of sublayer and buffer zone in turbulent flow 6.6 The Boundary Layer Model Figure 6.6-\ Boundary layer development on flat plate Example 6.6-1 Displacement thickness 6.6.1 Momentum balance - integral equations Figure 6.6.1-1 Element in boundary layer Figure 6.6.1-2 Velocity profile development in the entrance region to a pipe 6.6.2 De-dimensionalization of the boundary layer equations 6.6.3 Exact solution of the momentum boundary layer equations via similarity variables 362xvm Table of Contents Example 6.6.3-1 Similarity variable developed from dimensional analysis Figure 6.63-1 Solution to Blasius boundary layer equation Example 6.6.3-2 Runge-Kutta solution of Blasius problem 6,7 Drag Coefficients Figure 6.7-1 Flow around an airfoil (a) without and (b) with separation 6.7. 1 Drag on immersed bodies (external flow) Figure 6.7.1-1 Drag coefficient for smooth flat plate oriented parallel to flow stream Example 6.7.I-I Drag on a flat plate Figure 6.7.1-2 Flow past circular cylinder Figure 6.7.1-3 Drag coefficient for circular cylinder Example 6.7.1-2 Wind force on a distillation column Figure 6.7.1-4 Drag coefficient for sphere Example 6.7.1-3 Terminal velocity of a polymer sphere in water 6.7.2 Drag in conduits - pipes (internal flow) Table 6.7.2-1 Properties of pipe Figure 6.7.2-1 Momentum balance on cylindrical fluid element in horizontal pipe Figure 6.7.2-2 Momentum balance on cylindrical fluid element in non-horizontal pipe Figure 6.7.2-3 Moody friction factor chart Figure 6.7.2-4 Relative roughness for clean new pipes Example 6.7.2-1 Expansion losses Figure 6.7.2-5 Equivalent lengths for losses in pipes Example 6.7.2-2 Direction of flow between tanks at differing pressures and heights Example 6.7.2-3 Friction loss in a piping system Friction factor calculations - serial paths Case 1: Pressure drop unknown Example 6.7.2-4 Pressure loss for flow between tanks Case 2: Diameter unknown Example 6.7.2-5 Transfer line from tank to column Example 6.7.2-6 Minimum pipe diameter Case 3: Length unknown Example 6.7.2-7 Air supply through hose Case 4: Flow rate unknown Example 6.7.2-8 Flow rate unknown Figure 6.7.2-6 Friction factor vs. Karman number Example 6.7.2-9 Calculation of flow rate via Karman number when pressure drop is known Non-circular conduits 424Table of Contents xix Example 6.7.2-10 Flow in a smooth annulus Example 6.7.2-11 Pressure drop in a pipe annulus Friction factor calculations - parallel paths Example 6.7.2-12 Pipe network with imposed pressure drop Table 6.7,2-2 Convergence of Newton’s Method Example 6.72- /3 Flow in a parallel piping system Example 6.7.2-14 Input of additional fluid to an existing pipe network 6.8 Non-Newtonian Flow 6.8.1 Bingham plastics Figure 6.8.1-1 Tube flow of Bingham plastic 6,8.2 Power-law fluids Example 6.8-1 Flow of polymer melt 6.9 Flow in Porous Media 6.9.1 Darcy’s law Figure 6,9.1-1 Permeability as a function of porosity for a bed of spheres Table 6.9.1-1 Porosities (void fractions) for dumped packings Table 6.9.1-2 Porosity and permeability for typical materials Example 6.9.1- I Flow of water in sandstone 6.9.2 Packed beds Example 6.92-1 Pressure drop for air flowing though bed of spheres Example 6.92-2 Pressure drop for water flowing though bed of cylinders 6.9.3 Filters 462 Example 6.9.3-1 Production scale fdter performance prediction from pilot plant data Example 6.9.3-2 Filter performance from data Example 6.9.3-3 Adapting existing filter to new product 6.10 Row Measurement 6.10.1 Pitot tube Figure 6.10.1-1 Pitot tube schematic Figure 6.10.1-2 Flow at mouth of pitot tube Example 6.10.1-1 Pitot tube traverse 6.10.2 Venturi meter Figure 6.10.2-1 Venturi schematic Figure 6.10.2-2 Venturi meter coefficient Example 6.10.2-1 Flow measurement with venturi meter 6.10.3 Orifice meter and flow nozzle Figure 6.10.3-1 Orifice meter, flow nozzle Figure 6.10.3-2 Orifice coefficient 483xx. Table of Contents Example 6.103- / Metering of crude oil with orifice Chapter 6 Problems 7 HEAT TRANSFER MODELS 7.1 The Nature of Heat 7.1.1 Forced convection heat transfer 7.1.2 Free convection heat transfer Table 7.1.2-1 Dimensionless Forms: Mass, Energy, and Momentum Equations for Natural and Forced Convection 7.2 Conduction Heat Transfer Models 7.2.1 Three-dimensional conduction in isotropic media Table 7.2.1-1 Components of Fourier Equation in Various Coordinate Systems 7.2.2 Boundary conditions at solid surfaces 7.2.3 Thermal conductivity Table 7.2.3-1 Relative Values of Thermal Conductivity 7.2.4 One-dimensional steady-state conduction in rectangular coordinates Analytical solution Figure 7.2.4-1 Homogeneous solid Figure 1.2.4-2 Temperature profile in 1-D heat transfer by conduction, rectangular coordinates Interface condition between solids - series conduction Figure 7.2.4-3 Conduction with two solids in contact assuming no temperature drop at interface Figure 7.2.4-4 Temperature profile with interfacial resistance Figure 7.2.4-5 Contact resistance treated as an intermediate solid Equivalent thermal resistance - series conduction Figure 7.2.4-6 Development of equivalent conductance for series conduction Equivalent thermal resistance - parallel conduction Figure 1.2.4-1 Development of equivalent conductance for parallel conduction Figure 7.2.4-8 Equivalent circuit for parallel conduction Example 7.2.4-1 Series conduction through layers - constant temperature at external surfaces Figure 7.2.4-9 Series conduction through layers with constant temperature at external surfaces Example 7.2.4-2 Series conduction through layers - constant convective heat transfer coefficient at external surfaces 549Table of Contents XXi Figure 7.2.4-10 Series conduction through layers with constant convective heat transfer coefficient at external surfaces Example 7.2.4-3 Conduction with variable thermal conductivity Figure 7.2.4-11 Conduction through firebrick with variable thermal conductivity Figure 7.2.4-12 Temperature profile Example 7.2.4-4 One-dimensional steady-state conduction with parallel path Figure 7.2.4-13 Conduction with parallel paths Figure 7.2.4-14 Analogous circuit Numerical solution The finite element method Figure 7.2.4-14 Examples of 1-D and 2-D finite elements Figure 7.2.4-15 Interpolation functions, Shape function Example 7.2.4-5 Solution by finite elements of steady-state conduction with generation Figure 7.2,4-16 Bar with thermal energy source Table 7.2.4-1 Global node numbering scheme Figure 7.2,4-17 Comparison of finite element and analytic solution Finite element method in higher dimensions 7.2.5 One-dimensional steady-state conduction in cylindrical coordinates Figure 7.2.5-1 Conduction through the wall of a composite cylinder Example 7.2.5-1 Conduction in a fuel rod Example 7.2.5-2 Conduction through an insulated pipe 7.2.6 One-dimensional steady-state conduction in spherical coordinates Figure 7,2,6-1 Radial conduction in spherical geometry Example 7.2.6-1 Conduction through shielding 7.2.7 Two-dimensional steady-state conduction Taylor series Analytical solution Orthogonal functions Example 72.7-2 Convergence of steady-state rectangular coordinate solution Numerical solution Finite difference method Forward difference approximation to the first derivative Backward difference approximation to the first derivative Central difference approximation to the first derivative 608xxu Table of Contents Approximation of second derivative Finite difference approximation to the Laplace equation Example 7.2.7-1 Determination of steady-state temperature distribution in a rectangular slab Irregular boundaries, Dirichlet boundary conditions Normal derivative (Neumann) boundary condition at nodal point Generation terms Example 7.2.7 -2 Finite difference solution of 2-D steadystate conduction 7.2.8 One-dimensional unsteady-state conduction Analytical methods for one-dimensional unsteady-state conduction Semi-infinite slab Figure 7.2.8-1 Semi-infinite slab with constant face temperature Example 7.2.8-1 Semi-infinite slab: conduction in a brick wall Finite slab Figure 7.2.8-2 Finite slab with constant face temperatures Figure 7.2.8-3 Unsteady-state heat transfer in a finite slab with uniform initial temperature and constant, equal surface temperatures Example 7.2.8-2 Finite slab model vs. semi-infinite slab model for one-dimensional unsteady-state conductive heat transfer Infinite cylinder and sphere Figure 7.2.8-4 Unsteady-state heat transfer in an infinite cylinder with uniform initial temperature and constant surface temperature Figure 7.2.8-5 Unsteady-state heat transfer in a sphere with uniform initial temperature and constant surface temperature Numerical Methods for One-Dimensional Unsteady-State Conduction Finite difference method Finite difference explicit form Figure 7.2.8-6 Finite difference grid for ID unsteady-state conduction Example 7.2.8-3 Unsteady-state heat transfer by explicit finite differences Finite difference implicit form Example 7.2.8-4 Finite slab unsteady-state heat transfer by finite differences 7.2.9 Multi-dimensional unsteady-state conduction Analytical solution for regular geometries 667Table of Contents xxin Figure 7.2.9-1 Multidimensional unsteady-state temperature profiles for conduction in regular geometries expressed as product of one-dimensional solutions Numerical solution of two-dimensional unsteady-slate conduction Finite difference method Figure 12.9-2 Alternating direction implicit method Finite element method 7.3 Convection Heat Transfer Models 7.3.1 The thermal boundary layer Figure 7.3.1-1 Solution of Equation (7.3.1-1) 7.3.2 Heat transfer coefficients Single-phase heat transfer coefficients Figure 7.3.2-1 Single-phase heat transfer coefficients Correlations for prediction of heat transfer Average heat transfer coefficients Example 7.3.2-1 Average heat transfer coefficients for pipe flow Design equations for convective heat transfer Forced convection in laminar flow Table 7.3.2-1 Nusselt number limit for laminar flow in ducts with various cross-sections Forced convection in turbulent flow Example 7.3.2-2 Comparison of the Dittus-Boelter, Colburn, and Sieder-Tate equations Heat transfer in non-circular conduits and annular flow External flows, natural and forced convection Table 7.3.2-2 Values of b and n for Equation (7.3.2-104) Table 7.3.2-3 Values of a and m for use with Equation (7.3.2- 105) Example 7.3.2-3 Heat transfer with flow normal to pipes Heat transfer with phase change Boiling - mechanism Figure 7.3.2-2 Boiling Curve Condensation - mechanism Boiling coefficients Table 7.3.2-3 Values of C for nucleate boiling model Condensing coefficients 7.4 Conduction and Convection in Series 7.4.1 Lumped capacitance models Figure 7.4.1-1 RC circuit analog of unsteady-state lumpedcapacitance heat transfer Criteria for use of lumped capacitance models Figure 7.4.1-2 Steady-state conduction through solid with convection at interface 727xxiv Table of Contents Figure 7.4.1-3 Steady-state conduction through solid with convection at interface, small vs. large Biot number Figure 7.4.1-4 Unsteady-state conduction through solid with convection at interface, small vs. large Biot number Example 7.4.1-1 Lumped capacitance models 7.4.2 Distributed capacitance models Figure 7.4.2-1 Mid-plane temperature for unsteady-state heat transfer in a slab of finite thickness 2L with uniform initial temperature and convective resistance at surfaces Figure 7.4.2-2 Temperature profile for unsteady-state heat transfer in a slab of finite thickness with uniform initial temperature and convective resistance at surfaces Figure 7.4.2-3 Centerline temperature for unsteady-state heat transfer in an infinite cylinder of radius r0 with uniform initial temperature and convective resistance at surfaces Figure 7.4.2-4 Temperature profile for unsteady-state heat transfer in an infinite cylinder of radius r0 with uniform initial temperature and convective resistance at surfaces Figure 7.4.2-5 Center temperature for unsteady-state heat transfer in a sphere of radius r0 with uniform initial temperature and convective resistance at surfaces Figure 7.4.2-6 Temperature profile for unsteady-state heat transfer in a sphere of radius r0 with uniform initial temperature and convective resistance at surfaces Example 7.4.2-1 Convective and conductive resistances in series 7.5 Radiation Heat Transfer Models Figure 7.5-1 The electromagnetic spectrum 7.5.1 Interaction of radiation and matter Geometric description of radiation Figure 7.5.1-1 Directions in space Intensity of radiation Figure 7.5.1-2 Radiation leaving A Lumping of quantities used in modeling radiation Incident radiation Figure 7.5.1-3 Extreme modes of reflection Absorptivity Reflectivity Transmittivity Emitted radiation Blackbodies Blackbody radiation Emissivity Radiosity 752Table of Contents XXIX Figure 8.8-2 Diffusion with instantaneous irreversible reaction in a membrane Example 8.8-1 Acidization of an oil well Figure 8.8-3 Mass transfer with slow or reversible chemical reaction Example 8.8-2 Mass transfer with heterogeneous reaction Example 8.8-3 Mass transfer with homogeneous reaction Chapter 8 Problems APPENDIX A: VECTOR AND TENSOR OPERATIONS A.1 Symbolic Notation Table A.l Operational properties of the del operator in different coordinate frames A.2 Index Notation A.2.1 The unit tensor A.2.2 The alternating tensor or permutation symbol APPENDIX B: ERROR FUNCTION Table B-l Gauss error function Figure B-l Error function APPENDIX C: NOMENCLATURE 997 INDEX 1009Table of Contents xxv 7.5.2 Radiant heat exchange between two opaque bodies with no intervening medium Table 7.5.2-1 History of radiation emitted 7.5.3 Kirchhoffs law Figure 7.5.3-1 Total emissivity of some surfaces 7.5.4 View factors Figure 7.5.4-1 Radiation between surfaces Reciprocity relation Summation rule Example 7.5.4-1 Integration to obtain view factor Table 7.5.4-1 View Factors Example 7.5.4-2 Use of reciprocity relation and summation rule to infer view factor for concentric spheres 7.5.5 Radiant heat exchange between blackbodies Example 7.5.5-1 Heat transfer by radiation - blackbody Example 7.5.5-2 Use of view factor tables with blackbody radiation exchange 7.5.6 Radiative exchange between gray bodies Figure 7.5.6-1 Electrical analog of net radiation from a gray surface Figure 7.5.6-2 Network analog of radiation exchange with gray surfaces in an enclosure Example 7.5.6-1 Two-gray-body exchange in enclosure Example 7.5.6-2 Heat transfer by radiation - gray body 7.6 Overall Heat Transfer Coefficients Figure 7.6-1 Insulated pipe Figure 7.6-1 Overall heat transfer coefficients Example 7.6-1 Controlling resistance for heat transfer resistances in series - spherical container of liquid oxygen Example 7.6-2 Controlling resistance in replacement of section of wall of distillation column Example 7.6-3 Overall heat transfer coefficient with fouling 7.7 Heat Exchangers 7.7.1 Average overall temperature difference 7.7.2 Countercurrent vs. concurrent operation Figure 7.7.2-1 T-H diagram for countercurrent flow of two streams Figure 7.7.2-2 T-H diagram for concurrent flow of two streams Figure 7.7.2-3 T-H diagram for countercurrent flow of two streams Figure 7.7.24 T-H diagram for concurrent flow of two streams 799xxvi Table of Contents Example 7.7.2-1 Concurrent vs. countercurrent flow in a concentric tube exchanger 7.7.3 NTU method for design of heat exchangers Figure 7.7.3-1 T-H diagram for two streams between which sensible heat is to be exchanged in countercurrent flow Figure 7.7.3-2 T-H diagram for two streams between which sensible heat is to be exchanged in concurrent flow Figure 7.7.3-3 Pinch with concurrent operation Figure 7.7.3-4 Pinch with countercurrent operation Table 7.7.3- la Effectiveness/NTU relationships Table 7.7.3-lb NTU/effectiveness relationships Example 7.7.3-1 Determination of effectiveness for a concurrent flow exchanger Example 7.7.3-2 Calculation of area using NTU and e for a concurrent flow exchanger Example 7.7.3-3 Calculation of exit temperatures using NTU and e for a heat exchanger of known area 7.7.4 F-factor method for design of heat exchangers Figure 7.7.4-1 Correction factor to log mean temperature difference - one shell pass, 2n tube passes Example 7.7.4-1 Use of F Factor compared to effectiveness/NTU method Chapter 7 Problems 828 8 MASS TRANSFER MODELS 8.1 The Nature of Mass Transfer 8.2 Diffusive Mass Transfer Models 8.2.1 Velocities of components in a mixture Figure 8.2.1-1 Diffusion of vapor from vessel Figure 8.2.1-2 Evolution of concentration profile Figure 8.2.1-3 Velocity of molecule Figure 8.2.1-4 Changing velocity and displacement of single molecule via collisions Example 8.2.1-1 Average velocity when individual particles have the same velocity Figure 8.2.1-5 Identical molecules, identical velocities Example 8.2.1-2 Average velocity when individual particles have different velocities Figure 8.2.1-6 Identical molecules, differing velocities Example 8.2.1-3 Number average velocity, velocities in two dimensions Figure 8.2.1-7 Number average velocity, velocities in two dimensions Table 8.2.1-1 Coordinate frame motion 857Table of Contents xxv/ / Table 8.2.1-2 Mass transfer relationships 858 8.2.2 Mechanisms of mass transfer 858 8.2.3 Fick’s law 858 Table 8.2.3-1 Equivalent forms of Fick's law referred to coordinate systems in various motions Figure 8.2.3-1 Flux of marbles without diffusion Figure 8.2.3-2 Flux of marbles with diffusion Figure 8.2.3-3 Fluxes compared 8.2.4 Binary diffusivities Figure 8.2.4-1 Diffusivities in solids Figure 8.2.4-2 Diffusivities in liquids Figure 8.2.4-3 Diffusivities in gases 8.2.5 Solutions of the diffusion equation One-dimensional equimolar counterdiffusion in rectangular coordinates Example 8.2.5-1 Equimolar counterdiffusion One-dimensional diffusion of A through stagnant B observed in rectangular coordinates Example 8.2.5-2 Diffusion of vapor through a stagnant gas Figure 8.2.5*1 Diffusion through stagnant gas layer One dimensional unsteady-state diffusion in a semi-infinite slab Figure 8.2.5-2 Semi-infinite slab with constant face concentration 8.2.6 Diffusion in porous solids 8.2.7 Dispersion Figure 8.2,7-1 Dispersion and diffusion as a function of Peclet number 8.3 Convective Mass Transfer Models 8.3.1 The concentration boundary layer Figure 8.3.1-1 Concentration boundary layer Figure 8.3.1-2 Boundary layer Figure 8.3.1-3 Boundary layer solution for a flat plate 8.3.2 Film theory and penetration-renewal theory 8.4 The Mass Transfer Coefficient for a Single Phase Example 8.4-1 Calculation offlux from a mass transfer coefficient Example 8.4-2 Mass transfer using partial pressure as a driving force Example 8.4-3 Mass transfer using species mass density as driving force 8.4,1 Design equations for single-phase mass transfer coefficients Flat plates Example 8.4.1-1 Average mass transfer coefficient from local coefficient 896xxvut Table of Contents Mass transfer in flow in pipes Mass transfer from spheres, drops, and bubbles Example 8.4.1-2 Comparison of mass transfer coefficient models Example 8.4.1-3 Mass transfer coefficient for dissolution of a sphere Packed beds Height of transfer unit models 8.4.2 Dimensional analysis of mass transfer by convection 8.5 Overall Mass Transfer Coefficients Figure 8.5-1 Mass transfer concentrations Figure 8.5-2 Interface conditions Example 8.5-1 Calculation of interface composition 8.5.1 Incorporation of overall mass transfer coefficient into height of transfer unit model Example 8.5.1-1 Overall transfer units 8.6 Relationship of Overall and Single-Phase Mass Transfer Coefficients Figure 8.6-1 Assumption necessary to utilize overall mass transfer coefficient Example 8.6-1 Controlling resistance for mass transfer 8.7 Design of Mass Transfer Columns Figure 8.7-1 Typical countercurrent gas absorber 8.7.1 Determination of liquid-to-gas ratio Figure 8.7.1-1 Gas absorption 8.7.2 Calculation of tower diameter Figure 8.7.2-1 Norton Chemical Process Products Corporation Intalox Figure 8.7.2-2 packing pressure drop Table 8.7.2-1 Values of coefficient F for packings 8.7.3 Calculation of packing height Table 8.7.3-1 n integrals 8.7.4 Applications Example 8.7.4-1 Analytical calculation of interfacial concentration Example 8.7.4-2 Analytical determination of number of transfer units: straight operating and equilibrium lines Example 8.7.4-3 Effect of change of L/G on outlet composition Example 8.7.4-4 Design of absorber Example 8.7.4-5 Economic optimization of an absorber 8.8 Mass Transfer with Chemical Reaction Figure 8.8-1 Diffusion in a membrane
كلمة سر فك الضغط : books-world.net The Unzip Password : books-world.net أتمنى أن تستفيدوا من محتوى الموضوع وأن ينال إعجابكم رابط من موقع عالم الكتب لتنزيل كتاب Momentum, Heat, and Mass Transfer Fundamentals رابط مباشر لتنزيل كتاب Momentum, Heat, and Mass Transfer Fundamentals 
|
|