Admin مدير المنتدى


عدد المساهمات : 18745 التقييم : 34763 تاريخ التسجيل : 01/07/2009 الدولة : مصر العمل : مدير منتدى هندسة الإنتاج والتصميم الميكانيكى
 | موضوع: كتاب Precision CNC Machining for High-Performance Gears - Theory and Technology الإثنين 01 أبريل 2024, 7:30 pm | |
| 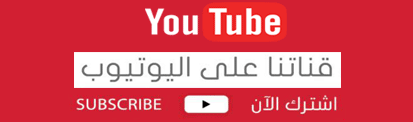
أخواني في الله أحضرت لكم كتاب Precision CNC Machining for High-Performance Gears - Theory and Technology SHILONG WANG Chongqing University, Chongqing, China GUOLONG LI Chongqing University, Chongqing, China CHI MA Chongqing University, Chongqing, China
 و المحتوى كما يلي :
Contents Preface vii Acknowledgments ix 1. Introduction 1 1.1 Overview of high-performance gear 1 1.2 High-performance gear CNC machining technology 4 1.3 Status and development trend of CNC machining technology of high-performance gear 23 1.4 Current situation and development trends of typical gear making machines 38 1.5 Opportunities and challenges 40 References 41 2. Computational theory for precision machining of high-performance gear 49 2.1 Modeling the modified tooth surface of high-performance gear 50 2.2 Envelope principle of point-vector family 56 2.3 First envelope calculation of point-vector family for a modified tooth profile 63 2.4 Calculation of the second envelope modification of point-vector family 74 References 86 3. Method to reduce the principle errors in high-performance gear machining 87 3.1 Method for reducing the tooth surface twist during forming machining for a modified gear 88 3.2 Method for modified gear to reduce errors during generating machining 105 3.3 Principle error of hob-relief grinding and its reduction method 118 3.4 Method of error reduction for the gear shaper cutter grinding principle 128 References 141 4. Modeling methods and compensation techniques for multisource errors of the CNC gear machine tool 143 4.1 Modeling and sensitivity analysis of the geometric error 144 4.2 Tool error modeling of the CNC gear machine tool 161 4.3 Modeling the force-induced geometric error in CNC gearing machines 176 v4.4 Establishment of the thermal error model of the CNC gear machine tool 186 4.5 Multisource errors compensation for the CNC gear machine tool 206 References 239 5. Design and optimization of the precision CNC gear machine tool 241 5.1 Design of core functional components for precision CNC gear machine tool 242 5.2 Thermal characteristics analysis and optimization of the precision CNC gear machine tool 258 5.3 Design of high-speed dry cutting hob 290 5.4 Gear manufacturing function software 294 5.5 Application case 300 References 303 6. Optimization method of the grinding process parameters 305 6.1 Process parameter optimization for tooth-surface precision 306 6.2 Grinding parameter optimization for residual stress 315 6.3 Process parameter optimization for energy consumption 326 6.4 Process parameter optimization of gear-tooth machining considering precision and quality 337 References 345 7. High-speed dry-cutting process and automatic production line of gear 347 7.1 High-speed dry cutting process of gear and key technology of automatic production line 349 7.2 Automatic production line integration of high-speed dry cutting of gears 360 7.3 Energy efficiency monitoring and process management system for high-speed dry cutting automatic production line for gears 363 7.4 Demonstration of the high-speed dry cutting automation production line of gears 369 References 371 Index 373 Index Note: Page numbers followed by f indicate figures and t indicate tables. A Adaptive neural fuzzy inference system (ANFIS) method, 13 AISI 52100 steel, 16–17 Automatic production line, 348–350f, 349 chamfering process, 358–360, 359f characteristics, 349–350 chip control technology, 349 dry turning tool, new, 351t, 352f energy efficiency monitoring, 363–369 heat accumulation, 349 hobbing process and equipment, 351–358 integration of high-speed dry cutting of gears linear layout truss-type, 361–363, 362f pin-type robot, 360–361, 361t, 361f parameters, 350, 351t process management system, 363–369 spindle structure, 350, 351f Automobile gears, 348 Auxiliary function module, 37 Axial modification end-face profile, 55 helix modifications, 54–56, 55f model, 352–354, 353f position, 54–55, 55f profile, 54, 56 tooth repair shape, 54, 55f Axis compensation method EGB working principle, 209, 210f error compensation, 209–210 grinding motion trajectory, 209–210, 210f motion axes, 207 path planning measurement, 208 point-vector quadratic envelope, 209 thermal error compensation, 233–239 three-dimensional (3D) model diagram, 206, 207f tooth surface creation coupling model, 208, 208f generation model, 208, 208f B Boundary constraints contact pair between hobbing machine table and platen, 253, 253f spindle transmission structure, 252, 252f table surface and body of hobbing machine, 253, 253f worm gear, 252, 252f C Chamfering technology, 358–360, 359f Chinese gear industry, 1–2 Chip-free machining method, 4 CNC gear machine tool boundary constraints, 252–253, 252–253f error modeling, 161–176 finite element mesh model, 251, 251f simulation, 253–257 geometric error, 144–161 high efficiency and precision multifunction, 303 high-precision and high-speed rotary table, 244–246, 246f high-speed precision hobbing spindle system, 242–244 large-scale hydrostatic rotary table, 247–251, 247–248f multisource errors, 241 structural optimization, 258 CNC machining technology high-performance gear, 4–23 status and development trend, 23–37 Conical worm grinding wheel grinding motion model, 137–138 grinding position and attitude, 135–137, 136–137f parameters, 132–135, 133f, 138, 139t proposal, 130–132, 132f Coordinate systems, 123–124, 124f Coordinate transformation, 64, 71, 77–79 Cubic boron nitride (CBN) modified honing process, 39–40 Cutting force, geometric error, 176–177 comparative analysis of M-value, 231–233, 232f compensation model, 228–230, 229t, 229f experimental principle of radial error, M value, 230–231, 230–232f 373Cutting force, geometric error (Continued) experimental scheme, 230 gear M-value, 231, 232f Cutting heat, high-speed cutting, 14–18 Cyclic grinding module, 37 D Deflection diamond roller, 113–116, 114–115f rotor core, 263 Diamond roller, 113–116, 114–115f DLL. See Dynamic link library (DLL) Double degree-of-freedom meshing analysis, 178–182, 179–181f Drum modification, 91, 110 Drum-shape modification, 82, 84f Dry cutting. See High-speed dry cutting process Dynamic link library (DLL), 299 E Electric spindle tool post, 354–355, 355f Energy consumption model gear-machining machine, 326–335 machine power, 326–327 toothing process parameters, 335–337 Energy efficiency monitoring, 363–369, 364f automatic NC programming, 368 drawing process and production tasks, dynamic issue, 365 dynamic monitoring system, 366–367 equipment and production line, 366 equipment running status monitoring and fault alarm management, 366 optimization decision of process parameters, 368 production schedule information collection, 365 remote diagnosis and management, 368–369 task monitoring, 365 tool changes, 367, 367f Enveloping process, 59–60, 60f Error compensation geometric, 224–228 measurement and identification, transmission chain, 213–216, 213–214f, 214t thermal model (see Thermal errors) transmission chain errors, 210–213, 211f Error modeling grinding wheel error, 168–170, 168–169f hob error end-tooth profile, 161–164, 166, 166f error helicoid, 167–168, 167f gear hob, 161–164 helicoid, 166, 166f parametric expression, 166 tooth surface, 167 worm grinding wheel (see Worm grinding wheel error) Error sensitivity analysis error model simplification, 148–149 Morris method, 150–157, 153–156f, 156t Sobol method, 157–161, 160f F Finite element analysis (FEA) method, 177–178, 177f, 273–274 cloud chart for modal vibration column, large, 254, 254f column structure, 254, 257f hob box, large column and left body assembly, 254, 256f left body, 254, 255f outer support structure, 254, 257f right body structure, 254, 258f sliding plate on hob box, 254, 254f table shell, 254, 257f table surface, 254, 256f tool holder of hob box and cover plate, 254, 255f transmission mechanism, 254, 255f x-axis screw and screw chuck holder, 254, 256f hobbing machine, 253–254 First envelope process comparative analysis, 72–73, 72t, 73–74f coordinate systems, 63–64, 64f of point vector, 66–69, 66–68f profile calculation of forming tools, 69–72, 69–70f projection, 64–66, 65f Flywheel, 19 Force-induced geometric error, 10–12 cutting, 176–177, 176f finite element analysis (FEA) method, 177–178, 177f mapping relationship double degree-of-freedom meshing analysis, 178–182, 179–181f machining simulation, 182–186, 183t, 184–185f 374 IndexG Gear grinding processes, 32–34 auxiliary function module, 37 CNC machine, 303 contact line, 89–90 contact trace, 106 cyclic grinding module, 37 finite element model, large plane wheel, 287–290, 287–290f five-axis linkage, 35, 35f gear making process, 22–23 gear shaper cutter, 131–132, 132f, 138–141 and hobbing, 22–23 interface, 37 machine tool status module, 37 mapping relationship, 88, 89f numerical simulation, 140–141, 140–141f optimization, 21–23 production process module, 37 project management module, 36–37 simulation process, 90–91, 90–91f temperature rise calculation, large plane wheel, 283–287, 284f, 286f thermal characteristics, large plane wheel coordinate system, 281, 281f grinding wheel and tooth surface, 281–282, 282f mirror heat source, 282–283, 282f schematic diagram, 280, 280f working principle, 279–280, 279f thermal deformation, 12 three-dimensional model diagram, 35–36, 36f worm wheel, 5–6, 6f Gear hobbing machine, 4–5, 5f, 20, 28f, 243, 356, 358f, 362 and gear grinding processes, 22–23 gear making machine tools, 18–19 machining accuracy optimization algorithm flow, 309–310, 310f cumulative pitch errors, 309–310, 312f, 313–315, 314f gear errors, 313, 314t helix errors, 309–310, 311f, 313–315, 313f hobbing parameters, 309 optimal process parameters, 313–315, 315t prediction, 309–310, 312t process parameters and gear errors, 309, 311t single pitch errors, 309–310, 312f, 313–315, 314f tooth profile errors, 309–310, 311f, 313–315, 313f machining precision, 306 power measurement, 333f process parameters, 21–23 status and development CNC gear, intelligent, 24–25 high-precision, high-stiffness, and high-reliability, 25 high-speed and high-efficiency, 25–26 large-scale CNC, 27–28 wet and dry cutting, 26–27 structure and function module, 28–32, 28f numerical control (NC) code template, 29, 29t Siemens SINUMERIK 840Dsl, 30–31, 31f thermal error, 186–196 compensation model, 195–196 temperature variable, 192–196, 192–193f, 194t Gear machine. See also CNC gear machine tool large-scale gear machine tool, 301 thermal error, 3 tool transmission system, 2, 34 Gear-machining machine, 347, 351–352, 360 coordinate system, 330 cutting edge trajectory, 330–332 cutting power, 327, 329, 332 cutting stage energy, 329, 329f energy consumption model, 326–335 error modeling compensation technology, 7–8 force-induced, 10–12 machine tool geometric, 9–10 thermal-induced, 12–14 tool modeling, 7–8 fitting curve of machine tool, 327, 328f gear hobbing machine power measurement, 333, 333f gear workpiece, 331 hobbing force, 332 hobbing machine processing power, 327, 328f parameters, 333, 333t power measurements and prediction values, 333–335, 334t precision, 306 single tooth cutting simulation diagram, 331, 331f spindle speed, 327, 328t tooth-profile equation, 330 Index 375Gear-making errors, 148–149 Gear-making machine tool, 38–40 compensation method, 9–10 error modeling, 9–10 rotary table, 19–21 spindle system, 18–19 thermal errors, 12–13 Gear-making zero-programming system deformation error compensation, 234–235 hobbing machine, 234–235, 237 online temperature sensor arrangement, 235–236, 236f principle, 234 thermal error compensation, 236–237, 237f, 237t working gear and hob parameters, 236, 236t Y31200CNC6 hobbing machine, 236, 237f Gear manufacturing function software arbitrary modification module tooth direction, 297 tooth profile, 296–297 auxiliary function module, 296 circulating grinding module, 296 grinding wheel arbitrary modification module, 297, 298f machine tool status module, 295 production flow module, 295–296 project management module, 294–297 secondary development dynamic link library (DLL), 299 installation, 300 NC programming, 300 visual interface design, 298–299 tooth surface distortion control module, 297 Gear profile, 100 Gear shaper cutter conical worm grinding wheel, 130–135 gear grinding, 128–129 kinematic analysis, 135–138 parameters, 138, 139t principle, 129–130, 129f, 131f simulation verification, 138–141 Gear shaping machines, 38 Gear-tooth machining, 3, 35–36, 40, 337–345, 338f multiobjective parameter optimization algorithm competitive selection and cross variation, 340–341 elite strategy and population merging, 342–343, 342f nondominated sorting and congestion calculation, 340 population initialization, 339–340, 340–341t processing parameter characteristic quantities, 344 correlation coefficient matrix calculation, 343–344 principal component score, 344–345, 345t standardized data processing in optimal frontier, 343 Geometric error CNC gear machine tool motion chain, 144, 145f, 146 compensation CNC worm wheel gear grinding machine, 224 cutting force, 228–233 replacement value, 227 spatial attitude error component, 225 spatial error model, 224–225 ternary linear equation system, 227 value, 226–227 elements, 146 gear machine tool, 144, 145f, 146 modeling, 9–10, 144–148, 145f motion axes, 144–146 multisource, 144–146 sensitivity analysis, 148–161 spatial position error, 147–148 transformation matrix, 147 Geometric structure design, 241–242, 293, 294f chip grooves, 292 coating, 292–293, 293f cutting edge length, 292 heat treatment procedure, 293 high-speed dry cutting hob, 293, 294f manufacturing procedure, 292 multihead hob, 292 shank mechanism, 291 small diameter, 291, 291f Green manufacturing environmental impact, 347 resource consumption, 347 Green production, 348 Grinding parameter and hobbing, 305 mathematical relationship, 322–324 residual stress, 315–326 Grinding process gear, 315 376 Indexhigh-performance gears, 305 optimization process, 338f parameters, 337–338 process parameter optimization, 306–315 Grinding simulation, 138–140 Grinding wheel arbitrary modification, 294, 297 automatic modification, 303 carborundum, 297 CNC gear machine tool, 241–242 and diamond roller, 295 error, 168–170, 168–169f profile contour calculation, 125–126 coordinate systems, 123–124, 124f relieving grinding wheel, 125–126 SIEMENS numerical control programming language, 300 tooth surface, 279–280, 282f H Heat accumulation, 349 Heat dissipation forced convection by cooling system, 269 heat transfer, 270–271 and heat generation, 276–277 natural convection, 270 Heat source model ball screw pair, 267–268 rolling bearing, 258–268, 260f rolling guide pair, 268 servo/built-in motor, 261–267, 264f, 266t Helical tooth surfaces, 50, 50f, 64f High-performance gears, 2–4 High-speed dry cutting process automatic production line, 349, 349–350f characteristics, 349–350 chip control technology, 349 heat accumulation, 349 new dry turning tool, 351t, 352f parameters, 350, 351t spindle structure, 350, 351f line of gears, 369–370, 370t High-speed dry hobbing machine, 291f, 301–303, 302f data acquisition flowchart, 196, 197f displacement data acquisition, 197–198, 198f environmental temperature, 198 geometric structure design, 293, 294f chip grooves, 292 coating, 292–293, 293f cutting edge length, 292 heat treatment procedure, 293 manufacturing procedure, 292 multihead hob, 292 shank mechanism, 291 small diameter, 291 recording device, 197–198, 198f sensors arrangement, 198, 199f temperature change curve, 198, 199f data acquisition, 197–198, 197f sensors, 198 temperature-thermal error, 197–198 thermal characteristics experiment, 196–199 thermal error curve, 199, 200f modeling, 199–202, 200–201t, 201f principle, 196–199, 197f Hobbing error, 242–244, 242–243f, 245f end-tooth profile, 161–164, 166, 166f helicoid, 166–168, 166–167f parametric expression, 166 tooth surface, 167 Hobbing process, 87–88 cutting edge, 330 and equipment, 351–358 gear (see Gear hobbing machine) and grinding machines, 305, 326–327 high-speed dry cutting precision, 352–354, 353f machine processing, 328f optimization design high-speed dry cutting workbench, 355–358, 357–358f modified hob, 354 spindle, 354–355, 355–356f parameters, 306, 368 precision prediction model, 306–309, 306–308f Hobbing tooth profile, 352–354, 353f Hobbing workbench damping mechanism, 356–358, 357f gear hobbing machine, 356 high-speed dry cutting precision gear, 357, 358f three-dimensional solid model, 356, 357f workbench design principle, 358 Human-machine interface (HMI), 30 Index 377I Improved particle swarm optimization (IPSO), 308–310, 308f, 312t, 315 K K-shape modification, 82, 84f L Large-scale precision CNC hobbing machine, 247, 301, 302f Linear layout truss-type automatic production line, 361–363, 362f M Machine tool geometric error modeling, 9–10 Machining error contact trace calculation, 106 tooth surface twist calculation model, 108–111, 108–109f in generating machining, 106–108, 107f Machining simulation, 182–186, 183t, 184–185f Material removal rate (MRR), 327 Modified gear contact line, 89–90 machining error analysis, 105–111 modeling, 105–111 tooth surface errors, 111–118 twist, 88–104 Modified tooth surface, 50–56 axial modification, 54–56, 55f first envelope calculation, 63–73, 64f spiral, 50–52 tooth profile modification, 52–54, 53f Morris method analysis steps, 150–151 cyclic sampling number, 152 error identification, 156–157 error reduction rate, 156–157, 157t geometric error tooth surface, 150 input and output parameters, 150 sensitivity analysis process, 152 sensitivity index plot, 152–153, 153–156f tooth-surface error component, 153–156, 156t model, 150 value interval, 151–152 Multisource errors, 241 axis compensation method, 206–210 error compensation for transmission chain, 210–223 geometric error compensation, 224–233 thermal error compensation, 233–239 N NC control programming, 300 Neural network (NN) algorithms,306–309,310f, 315 P Particle swarm optimization (PSO), 307, 308f, 312t Pin-type robot, 360–361, 361t, 361f Point-vector family, 170 approximation algorithm, 61–62, 61f composition, 56, 57f coordinate transformation, 64, 71, 77–79 end surface profile, 62–63, 62f enveloping process, 59–60, 60f first envelope calculation, 63–73, 64f motion trajectory, 58–59, 59f rotational projection, 71–72, 72t, 72f second envelope modification, 74–85 two-dimensional (2D) plane curves, 56–57, 57f three-dimensional (3D) space surfaces, 57–58, 58f Power honing, 39–40 Principle error of hob-relief grinding chip-holding grooves, 118 comparative verification grinding blade pitch circle, 128, 128t equal back angle cam, 126, 127f parameters, 126, 127t preshaving hob, 126, 127f gear-hob manufacturing process, 118 grinding wheel profile, 123–126 tooth tip curve, 119–123 Process management system, 363–369, 364f automatic NC programming, 368 drawing process and production tasks, dynamic issue, 365 dynamic monitoring system, 366–367 equipment and production line, 366 equipment running status monitoring and fault alarm management, 366 optimization decision of process parameters, 368 production schedule information collection and task monitoring, 365 remote diagnosis and management, 368–369 tool change monitoring and management, 367, 367f 378 IndexProcess parameter optimization gear-machining machine, 326–335 gear-tooth machining, 337–345 hobbing precision prediction model, 306–309, 306–308f machining accuracy algorithm flow, 309–310, 310f cumulative pitch errors, 309–310, 312f, 313–315, 314f gear errors, 313, 314t helix errors, 309–310, 311f, 313–315, 313f hobbing parameters, 309 optimal process parameters, 313–315, 315t prediction, 309–310, 312t process parameters and gear errors, 309, 311t single pitch errors, 309–310, 312f, 313–315, 314f tooth profile errors, 309–310, 311f, 313–315, 313f Profile grinding, 6, 7f R Renishaw XL-80 laser, 151–152 Residual stress, 316f alignment fixture, 315–318, 317–318f grinding parameters influence cutting depth, 318–320, 321t, 322f feed speed, 306–307, 320–321, 320t, 322f, 324 gear geometry specification, 318, 319t mathematical relationship, 322–324, 323t, 323f measurement results, 320, 320t parameter levels, 319, 319t wheel speed, 320–321, 321t measurement method, 315–318, 317–318f self-balanced internal stress, 315 surface stress influence, 324–326, 325f, 325t Roller deflection, 113–116, 114–115f Rotary table, 19–21 accuracy, 247–248 damping worm, 249–250, 250f high-precision, high-speed, 244–246, 246f hobbing machine, 247, 247–248f large-scale precision CNC hobbing machine, 247 large-size hydrostatic, 248–251, 249f transmission accuracy, 248 worm gear, 247, 248f worm transmission, 249–250, 250f Rotational projection, 71–72, 72t, 72f S Second envelope process comparative analysis, 80–85 coordinate transformation, 77–79 of point-vector family, 74–77, 75–78f, 83–85, 85f spiral projection, 79–80 Shaving process, 38–39 SIEMENS840Dsl CNC system, 294 Siemens SINUMERIK 840Dsl COM (commercial) technology, 32 full PC integrated control system, 31 human-machine interface (HMI), 30–31 numerical control system, 30 OPC standard, 32 software system, 30, 31f Simulation envelope surface contact line shape on tooth surface error, 95–97, 95–96f distribution, 91–92, 94f errors, 91–92, 93t spatial contact lines, 91 tooth profile error, 103, 104–105f tooth surface error additional rotation of c-axis, 99–100, 99f additional rotation on x-axis, 97–98, 97f Sobol method first-order sensitivity index, 159 flowchart calculation, 160, 160f geometric error probability distribution, 161 global sensitivity analysis method, 157–159 higher-order function terms, 158 identification process, 158 Monte Carlo integral method, 159 sampling sequence probability statistics, 161, 162t sensitivity analysis method, 160–161, 163–165f tooth-surface error component, 161, 165t SPARTApro software, 11–12 Spindle system, 18–19, 242–244, 242–243f, 245f Spiral tooth surface coordinate system, 63 gear end plane profile, 57–58 modeling, 50–52, 50f point-vector family, 66 tool coordinate system, 64 Standard involute profile, 82, 83f Index 379T Temperature field control technology, 14–18, 15f Thermal characteristics in gear grinding, 278–290 heat dissipation, 269–271 heat source analysis, 258–268 for tool holder analysis method, 271 finite element analysis (FEA), 273–274, 273f high-speed dry cutting, 271, 271f thermal-structure coupling analysis, 272, 272f three-dimensional geometric model, 272, 273f Thermal deformation, 12, 187–192, 187–188f, 190f, 233–234, 233f, 235f displacement and temperature test data, 191–192, 191f, 191t experimental test platform, 187–190, 188f, 190f model, 186–187, 187f Thermal errors, 12–13 CNC gear machine tool compensation, 234–239 thermal deformation, 233–234, 233f compensation model, 195–196 technology, 234–237 continuous generating grinding machine automobile transmission gears, 202 double meshing gear tester, 202, 203f experiment site, 202, 203f gear M-value, 202, 204f installation position, 202, 202f prediction model, 205 probabilistic neural network structure, 205–206, 205–206f radial thermal error modeling steps, 205, 205f temperature curve, 202, 204–205, 204f high-speed dry hobbing machine, 196–202 spiral compensation structure, 237–239, 238f temperature variable, 192–196, 192–193f, 194t vertical gear hobbing machine, 186–196 Thermal-induced error compensation methods, 14 error modeling, 13–14 temperature measurement points, 13 Three-dimensional (3D) modeling software, 11–12, 138–140 Ti6Al4Vdrymilling, 18 Tool error model grinding wheel error, 168–170, 168–169f hob, 161–168, 166–167f worm grinding wheel (see Worm grinding wheel error) Tool holder analysis method, 271 finite element analysis (FEA), 273–274, 273f high-speed dry cutting, 271, 271f numerical simulation analysis steady temperature field, 274–275, 274f steady thermal deformation, 275–276, 276f transient temperature field, 276–277, 277f transient thermal deformation, 277–278, 278f thermal-structure coupling analysis, 272, 272f three-dimensional geometric model, 272, 273f Tool spindle system, 241–244, 242–243f, 245f Tooth flank surface, 120–121, 121f Toothing process parameter optimization, 336–337 energy consumption model, 335–336 genetic algorithm, 336, 337f Tooth profile errors, 103, 104–105f, 111, 313–315, 313f Tooth profile modification coordinate system, 53 curves, 53, 53f, 80–81, 81f point vectors, 81–82 tooth root trimming, 52 Tooth surface integrity, 337–338 Tooth surface precision cutting forces, 308–309 gear hobbing, 306 improved particle swarm optimization (IPSO), 308, 308f mapping, 306–307, 307f neural network (NN) algorithms, 307 particle swarm optimization (PSO), 307, 308f process parameters, 306–307 Tooth surface quality gear-tooth machining, 337–345 optimization process, 337, 338f process parameters, 337 Tooth surfaces, 88f. See also Modified tooth surface axial modification, 54–56, 55f coordinate system, 64 creation coupling model, 208, 208f 380 Indexdistortion control module, 297 errors reduction additional rotation of the X-axis, 100–102, 102–103f contact lines shapes, 92t, 100, 101f during generating machining, 111–118, 112f gear, 80 generation model, 208, 208f grinding gear contact line, 89–90 mapping relationship, 88, 89f simulation process, 90–91, 90–91f measurement, 207, 208f optimization wheel installation angle, 103, 104f wheel profile, 103–104, 105f point vector (see Point-vector family) quality gear-tooth machining, 337–345 optimization process, 337, 338f process parameters, 337 simulation envelope surface, 93–100, 94f spiral, 50–52 twist analysis, 91–93, 92t, 92f calculation model, 108–111 errors reduction, 100–102 machining, 106–108 modified gear, 88–104 simulation envelope surface, 93–100 tool envelope plane, 88–91 Tooth tip curve equal back angle hob, 121–123, 122f hobs geometry, 119–120, 120f tooth flank surface, 120–121, 121f Torque motor, 20–21 Transmission chain errors, 210–213, 211f experiments, 219–223, 220t, 220f compensation of eI, 220–222, 221–222f compensation of el, 222–223, 223f measurement and identification, 213–216, 213–214f, 214t principle, compensation, 216–219, 217–218f Trial-and-error method, 3, 22 Truss-type automatic production line, 361–363, 362f Two-dimensional (2D) simulations, 11–12 V Vertical gear hobbing machine thermal deformation, 186–192, 187–188f, 190f thermal error modeling compensation model, 195–196 temperature variable, 192–196, 192–193f, 194t Vibration error, 143–144 Visual interface design, 298–299 W Workbench, hobbing damping mechanism, 356–358, 357f gear hobbing machine, 356 high-speed dry cutting precision gear, 357, 358f three-dimensional solid model, 356, 357f workbench design principle, 358 Worm gear shaft lead, 116–118, 117f Worm grinding wheel error, 5–6, 6f error separation, 174 forming dressing, 174–175, 174f functional model, 174 gear end face profile, 172, 172f grinding process, 173–174 mapping relationship, 170, 171f point trimming, 174–175, 175f point-vector family, 170 reverse compensation profile, 173, 173f reverse profile compensation, 174–175, 175f spiral surface, 172 tooth-profile error, 172–173 tooth surface of gear, 170, 171f, 172 two-dimensional (2D) point-vector family, 170 Worm-wheel generating grinding gears, 106 Y Y31200CNC6 hobbing machine, 236, 237f Yttrium aluminum garnet (YAG) tool, 17–18 Z Zero-programming system deformation error compensation, 234–235 hobbing machine, 234–235, 237 online temperature sensor arrangement, 235–236, 236f principle, 234 thermal error compensation, 236–237, 237f, 237t working gear and hob parameters, 236, 236t
كلمة سر فك الضغط : books-world.net The Unzip Password : books-world.net أتمنى أن تستفيدوا من محتوى الموضوع وأن ينال إعجابكم رابط من موقع عالم الكتب لتنزيل كتاب Precision CNC Machining for High-Performance Gears - Theory and Technology رابط مباشر لتنزيل كتاب Precision CNC Machining for High-Performance Gears - Theory and Technology 
|
|