Admin مدير المنتدى


عدد المساهمات : 18726 التقييم : 34712 تاريخ التسجيل : 01/07/2009 الدولة : مصر العمل : مدير منتدى هندسة الإنتاج والتصميم الميكانيكى
 | موضوع: كتاب Introduction to the Design and Behavior of Bolted Joints - Non-Gasketed Joints الثلاثاء 03 أكتوبر 2023, 2:12 am | |
| 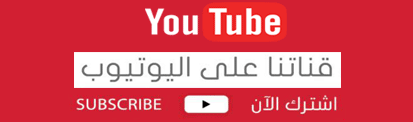
أخواني في الله أحضرت لكم كتاب Introduction to the Design and Behavior of Bolted Joints - Non-Gasketed Joints Fourth Edition John H. Bickford
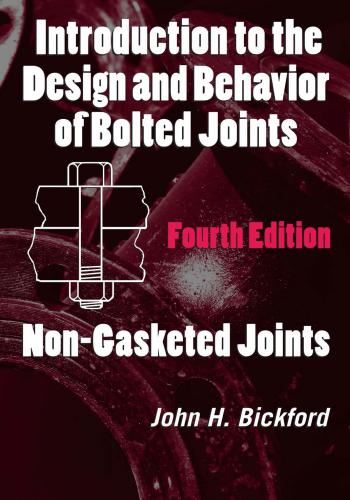 و المحتوى كما يلي :
Table of Contents Preface to the Fourth Edition .xxix Acknowledgments for Volume 1 of the Fourth Edition .xxxi Preface to the Third Edition .xxxiii Preface to the Second Edition .xxxv Preface to the First Edition .xxxvii Acknowledgments for the First Three Editions xli Editor xliii Abstract .xlv Chapter 1 Basic Concepts .1 1.1 Two Types of Bolted Joints .1 1.2 Bolt’s Job .1 1.2.1 Tensile Joints 1 1.2.2 Shear Joints 3 1.3 The Challenge 3 1.3.1 Assembly Process 4 1.3.2 In-Service Behavior .5 1.3.2.1 Joints Loaded in Tension .5 1.3.2.2 Shear Joints 5 1.4 Failure Modes 6 1.5 Design 7 1.5.1 In General .7 1.5.2 Specific Goals of the Designer 7 1.6 Layout of the Book 8 Exercises .8 Chapter 2 Materials 11 2.1 Properties That Affect the Clamping Force .11 2.1.1 Magnitude of the Clamping Force .11 2.1.2 Stability of the Clamping Force .12 2.1.2.1 Thermal Expansion or Contraction . 12 2.1.2.2 Corrosion . 12 2.1.2.3 Fatigue Rupture . 12 2.1.2.4 Loss of Strength with Temperature 12 2.1.2.5 Loss of Clamping Force with Temperature . 13 2.1.2.6 Elastic Stiffness of the Parts . 13 xiii2.1.2.7 Change in Stiffness with Temperature 13 2.1.2.8 Brittle Fracture . 13 2.1.3 Miscellaneous Properties .13 2.2 Fastener Standards .14 2.3 Selecting an Appropriate Standard 14 2.4 Bolting Materials 16 2.5 Tensile Strength of Bolting Materials 16 2.5.1 General Purpose=Automotive Group 17 2.5.2 Structural Steel Group 17 2.5.3 Petrochemical=Power Group .17 2.5.4 Metric Group 17 2.5.5 Extreme-Temperature Materials .18 2.5.5.1 American Society for Testing and Materials (ASTM) F2281 Materials 18 2.5.5.2 Traditional High-Temperature Materials . 18 2.5.6 Corrosion-Resistant Group .19 2.5.7 Two New ASTM Bolting Standards .19 2.5.7.1 Room Temperature Strengths of ASTM F2281 and F2282 Materials . 20 2.6 Metric Fasteners .20 2.7 Equivalent Materials 21 2.8 Some Comments on the Strength of Bolting Materials .21 2.8.1 In General .21 2.8.2 Shear Strength .21 2.8.3 Bearing Yield Strength 23 2.8.4 Hardness versus Strength 23 2.9 Nut Selection 24 2.10 Effects of Temperature on Material Properties 26 2.10.1 Thermal Expansion .27 2.10.2 Miscellaneous Temperature Problems .31 2.11 Other Material Factors to Consider .32 2.11.1 Fatigue Properties .32 2.11.2 Corrosion 32 2.11.3 Miscellaneous Considerations .32 2.12 Joint Materials .32 Exercises .35 References and Bibliography 35 Chapter 3 Stress and Strength Considerations 39 3.1 Types of Strength .39 3.1.1 Tensile Strength 39 3.1.2 Thread-Stripping Strength 39 3.1.3 Shear Strength .40 3.1.4 Brittle Fracture Strength .40 3.1.5 Strengths at High and Low Temperatures 40 3.1.6 Fatigue Strength 40 3.1.7 Stress Corrosion Cracking Strength 40 3.2 Bolt in Tension .41 3.2.1 Elastic Curves for Bolts in Tension .41 3.2.2 Elastic Curves under Repeated Loading .42 xiv3.2.3 Stress Distribution under Tensile Load 42 3.2.4 Stress Concentrations 43 3.2.5 Magnitude of Tensile Stress 43 3.2.6 Stress in the Nut .45 3.3 Strength of a Bolt .48 3.3.1 Proof Strength .48 3.3.2 Tensile Stress Area 49 3.3.3 Other Stress Area Equations .50 3.3.4 Stress Areas—Metric Threads .51 3.3.5 Strength of the Bolt under Static Loads .53 3.4 Strength of the Joint 54 3.4.1 Contact Stress between Fastener and Joint .54 3.4.2 Stresses within and between the Joint Members .56 3.4.3 Static Failure of the Joint .56 3.5 Other Types of Load on a Bolt 57 3.5.1 Strength under Combined Loads 59 Exercises and Problems 59 References and Bibliography 59 Chapter 4 Threads and Their Strength .61 4.1 Thread Forms 61 4.1.1 Thread Forms in General .61 4.1.2 Inch Series Thread Forms .61 4.1.3 Metric Thread Forms 63 4.2 Thread Series 63 4.3 Thread Allowance, Tolerance, and Class .64 4.3.1 Inch Series Threads .64 4.3.1.1 Allowance . 64 4.3.1.2 Tolerance 64 4.3.1.3 Class . 64 4.3.2 Metric Threads 65 4.3.2.1 Tolerance Position (the Allowance) 66 4.3.2.2 Tolerance Grade (the Tolerance) 66 4.3.2.3 Tolerance Class (the Class) . 66 4.3.3 Inch Series and Metric Thread Classes, Compared 66 4.3.4 Coating Allowances 67 4.3.5 Tolerances for Abnormal Lengths of Engagement .67 4.4 Inspection Levels 68 4.5 Thread Nomenclature 69 4.5.1 Inch Series .69 4.5.2 Metric Thread .69 4.6 Coarse- versus Fine- versus Constant-Pitch Threads .70 4.6.1 Coarse-Pitch Threads 70 4.6.2 Fine-Pitch Threads 70 4.6.3 Constant-Pitch Threads 70 4.6.4 Miscellaneous Factors Affecting Choice .70 4.7 The Strength of Threads 71 4.7.1 Basic Considerations .71 xv4.7.2 Thread Strength Equations .71 4.7.3 Thread Strength Computations When Le ¼ D .72 4.7.4 Basic Procedure—An Example .73 4.7.5 Thread Strength Calculations When Le 6¼ D .73 4.7.6 Other Stress Area Formulas 74 4.8 What Happens to Thread Form under Load? .76 4.9 Things That Modify the Static Strength of Threads 76 4.9.1 Common Factors 76 4.9.2 Which Is Usually Stronger—Nut or Bolt? 79 4.9.3 Tables of Tensile Stress and Shear Areas 79 4.10 Other Factors Affecting Strength .81 4.10.1 Pitch Diameter 81 4.10.2 Other Thread Parameters 81 Exercises and Problems 82 References and Bibliography 82 Chapter 5 Stiffness and Strain Considerations 85 5.1 Bolt Deflection .85 5.1.1 Basic Concepts 85 5.1.2 Change in Length of the Bolt .87 5.1.2.1 Effective Length 87 5.1.2.2 Cross-Sectional Areas of the Bolt . 89 5.1.3 Computing Change in Length of the Bolt 89 5.2 Bolt Stiffness Calculations .90 5.2.1 Basic Concepts 90 5.2.2 Example 90 5.2.3 Actual versus Computed Stretch and Stiffness .92 5.2.4 Stiffness of Bolt–Nut–Washer System 92 5.2.5 Alternative Expression for Bolt Stiffness 92 5.2.6 Energy Stored in the Bolt .93 5.3 The Joint 94 5.3.1 Basic Concepts 94 5.3.2 Computing Joint Stiffness .95 5.3.2.1 Stiffness of Concentric Joints . 96 5.3.2.2 Stiffness of Eccentric Joints 97 5.3.3 Stiffness in Practice .100 5.3.3.1 A Quick Way to Estimate the Stiffness of Non-Gasketed Steel Joints 100 5.4 Gasketed Joints 101 5.5 An Alternate Way to Compute Joint Stiffness 103 5.6 Joint Stiffness Ratio or Load Factor .104 5.7 Stiffness—Some Design Goals .104 5.7.1 Energy Stored in the Joint Members 104 5.7.2 Relationship between Stiffness and Stored Energy .105 5.7.3 Stiffness Ratio .106 Exercises and Problems 106 References 107 xviChapter 6 Introduction to Assembly .109 6.1 Initial versus Residual Preload 109 6.2 Starting the Assembly Process .110 6.2.1 Assembling the Parts 110 6.2.2 Tightening the First Bolt 110 6.3 Bolt Preload versus Clamping Force on the Joint .114 6.3.1 Effects of Hole Interference 114 6.3.2 Resistance from Joint Members .116 6.4 Continuing the Snugging Pass .119 6.5 Short-Term Relaxation of Individual Bolts .119 6.5.1 Sources of Short-Term Relaxation .119 6.5.1.1 Poor Thread Engagement 120 6.5.1.2 Thread Engagement Too Short 120 6.5.1.3 Soft Parts 121 6.5.1.4 Bending 121 6.5.1.5 Nonperpendicular Nuts or Bolt Heads 121 6.5.1.6 Fillets or Undersized Holes 121 6.5.1.7 Oversized Holes 121 6.5.1.8 Conical Makeups . 121 6.5.2 Factors Affecting Short-Term Relaxation 122 6.5.2.1 Bolt Length 123 6.5.2.2 Belleville Washers . 123 6.5.2.3 Number of Joint Members . 123 6.5.2.4 Tightening Speed 123 6.5.2.5 Simultaneous Tightening of Many Fasteners . 124 6.5.2.6 Bent Joint Members . 124 6.5.3 Amount of Relaxation to Expect 124 6.5.4 Torsional Relaxation 125 6.6 Elastic Interactions between Bolts .127 6.7 The Assembly Process Reviewed .132 6.8 Optimizing Assembly Results 134 Exercises .135 References 135 Chapter 7 Torque Control of Preload .137 7.1 Importance of Correct Preload 137 7.1.1 Problems Created by Incorrect Preload 138 7.1.2 How Much Preload? .138 7.1.3 Factors That Affect the Working Loads on Bolts 139 7.2 Torque versus Preload—The Long-Form Equation 140 7.3 Things That Affect the Torque–Preload Relationship .142 7.3.1 Variables That Affect Friction 142 7.3.2 Geometric Variables .143 7.3.3 Strain Energy Losses 144 7.3.4 Prevailing Torque .144 7.3.5 Weight Effect 144 7.3.6 Hole Interference 145 xvii7.3.7 Interference Fit Threads .145 7.3.8 The Mechanic 145 7.3.9 Tool Accuracy .145 7.3.10 Miscellaneous Factors .145 7.4 Torque versus Preload—The Short-Form Equation 146 7.5 Nut Factors 147 7.5.1 Some General Comments 147 7.5.2 Nut Factor Examples and Case Histories .148 7.5.3 Coefficient of Friction versus Nut Factor .151 7.6 Torque Control in Practice 151 7.6.1 What Torque Should I Use? .151 7.6.2 Initial Preload Scatter .152 7.6.3 Low Friction for Best Control 153 7.6.4 The Lines Aren’t Always Straight .153 7.6.5 Other Problems .154 7.7 Some Tools for Torque Control 155 7.7.1 Some Generalities .155 7.7.2 Reaction Forces Created by the Tool .157 7.7.2.1 Shear Loads Created by Torque Wrenches 157 7.7.2.2 Reaction Torques . 158 7.7.3 In the Beginning—A Search for Accuracy 159 7.7.3.1 Manual Torque Wrenches 159 7.7.4 More Torque for Large Fasteners 160 7.7.4.1 Torque Multipliers and Geared Wrenches . 160 7.7.4.2 Hydraulic Wrenches . 160 7.7.5 Toward Higher Speed .160 7.7.5.1 Impact Wrenches 161 7.7.5.2 Pulse Tools . 161 7.7.5.3 Nut Runners . 161 7.7.6 Add Torque Calibration or Torque Monitoring .162 7.7.7 Add Torque Feedback for Still Better Control .164 7.7.8 For More Information 164 7.8 Fasteners That Limit Applied Torque .164 7.8.1 The Twist-Off Bolt 164 7.8.2 The Frangible Nut 165 7.9 Is Torque Control Any Good? .166 7.10 Testing Tools 166 7.11 The Influence of Torque Control on Joint Design .167 7.12 Using Torque to Disassemble a Joint 168 Exercises and Problems 169 References and Bibliography 169 Chapter 8 Torque and Turn Control 173 8.1 Basic Concepts of Turn Control 173 8.2 Turn versus Preload .175 8.2.1 Common Turn–Preload Relationship .175 8.2.2 Other Turn–Preload Curves 176 8.2.2.1 Sheet Metal Joint 176 8.2.2.2 Gasketed Joint 177 xviii8.3 Friction Effects .177 8.4 Torque and Turn in Theory .179 8.4.1 Torque, Turn, and Energy 179 8.4.2 Torque–Turn–Preload Cube .179 8.4.3 The Broader View .179 8.5 Turn-of-Nut Control 181 8.5.1 The Theory .181 8.5.2 The Practice 182 8.5.2.1 Structural Steel . 182 8.5.2.2 Turn-of-Nut Procedure in Production Operations . 183 8.5.2.3 Turn-of-Nut Procedure in Aerospace Assembly 183 8.6 Production Assembly Problems .184 8.7 Popular Control Strategies .186 8.7.1 Torque–Angle Window Control .186 8.7.2 Torque–Time Window Control 187 8.7.3 Hesitation and Pulse Tightening .187 8.7.4 Yield Control 188 8.7.5 Turn-of-Nut Control 190 8.7.6 Prevailing Torque Control 191 8.7.7 Plus—Permanent Records 191 8.7.8 Meanwhile, Out in the Field .191 8.8 Monitoring the Results 192 8.9 Problems Reduced by Torque–Angle Control .193 8.10 How to Get the Most Out of Torque–Angle Control 193 Exercises and Problems 194 Bibliography and References 194 Chapter 9 Other Ways to Control Preload .197 9.1 Stretch Control: The Concept 197 9.2 Problems of Stretch Control 198 9.2.1 Dimensional Variations 198 9.2.2 Change in Temperature 199 9.2.3 Plastic Deformation of the Bolt 199 9.2.4 Bending and Nonperpendicular Surfaces 199 9.2.5 Grip Length 199 9.3 Stretch Measurement Techniques 199 9.3.1 Micrometer Measurements .199 9.3.1.1 Irregular Measurement Surfaces . 199 9.3.1.2 Operator Feel . 200 9.3.1.3 Measurement Accuracy Required 200 9.3.1.4 Depth Micrometers 200 9.3.2 Other Techniques 201 9.3.2.1 Dial Gages 201 9.3.2.2 Commercially Available Gage Bolt 202 9.3.2.3 Ultrasonic Measurements . 202 9.4 How Much Stretch? .202 9.5 Problems Reduced by Stretch Control .203 9.6 How to Get the Most Out of Stretch Control .204 9.7 Direct Preload Control—An Introduction .204 xix9.7.1 Strain-Gaged Bolts 205 9.7.2 Strain-Gaged Force Washers 205 9.7.3 Direct Tension Indicators .205 9.7.4 Squirter Self-Indicating DTIs 207 9.7.5 Twist-Off Tension-Control Bolts 207 9.7.6 Alternative-Design Fasteners 208 9.8 Bolt Tensioners 208 9.8.1 The Hardware .208 9.9 Bolt Heaters .210 9.10 Problems Reduced by Direct Preload Control .210 9.10.1 Direct Tension Indicators .210 9.10.2 Twist-Off Bolts 211 9.10.3 Hydraulic Tensioners 211 9.10.4 Bolt Heaters 211 9.11 Getting the Most Out of Direct Preload Control 211 9.11.1 Twist-Off Bolts and DTI Washers 211 9.11.2 Bolt Tensioners .212 9.11.3 Bolt Heaters 212 9.12 Ultrasonic Measurement of Stretch or Tension .213 9.12.1 In General .213 9.12.2 Principle of Operation .213 9.12.3 How It’s Used .214 9.12.4 Calibration of the Instrument .214 9.12.5 Presently Available Instruments 215 9.13 Ultrasonic Measurements Using Plasma-Coated, Thin Film Transducers 215 Exercises and Problems 215 References 216 Chapter 10 Theoretical Behavior of the Joint under Tensile Loads .219 10.1 Basic Joint Diagram .220 10.1.1 Elastic Curves for Bolt and Joint Members 220 10.1.2 Determining Maximum and Minimum Residual Assembly Preload 220 10.1.2.1 The Equations . 220 10.1.2.2 An Example 222 10.1.3 Joint Diagram for Simple Tensile Loads 224 10.1.4 The Parable of the Red Rolls Royce .226 10.1.5 Back to the Joint Diagram—Simple Tensile Load 227 10.2 Details and Variations .228 10.2.1 Changing the Bolt or Joint Stiffness .228 10.2.2 Critical External Load 229 10.2.3 Very Large External Loads .230 10.2.4 Another Form of Joint Diagram 230 10.3 Mathematics of the Joint .232 10.3.1 Basic Equations .232 10.3.2 Continuing the Example .234 10.4 Loading Planes .235 10.4.1 Tension Applied to Interface of Joint Members .236 10.4.2 Mathematics of a Tension Load at the Interface 238 10.4.3 Significance of the Loading Planes .238 10.4.4 Loading Planes within the Joint Members 239 xx10.4.5 Modifying Our Example to Include the Effects of Internal Loading Planes 243 10.5 Dynamic Loads on Tension Joints .243 10.6 The Joint Under a Compressive Load .245 10.7 A Warning .245 Exercises and Problems 246 References 247 Chapter 11 Behavior of the Joint Loaded in Tension: A Closer Look .249 11.1 Effect of Prying Action on Bolt Loads 250 11.1.1 Definition of Prying 250 11.1.2 Discussion of Prying .251 11.1.3 Prying Is Nonlinear .255 11.2 Mathematics of Prying .256 11.2.1 In General .256 11.2.2 VDI’s Analytical Procedure 256 11.2.3 Critical Loads and the Preloads Required to Prevent Joint Separation .260 11.2.4 Bending Stress in the Bolt before Liftoff 261 11.2.5 Effects of Very Large External Loads .263 11.3 Other Nonlinear Factors 263 11.3.1 Nut–Bolt System .263 11.4 Thermal Effects 266 11.4.1 Change in Elasticity 266 11.4.2 Loss of Strength 267 11.4.3 Differential Thermal Expansion 267 11.4.4 Stress Relaxation .271 11.4.5 Creep Rupture 273 11.4.6 Compensating for Thermal Effects .274 11.5 Joint Equations That Include the Effects of Eccentricity and Differential Expansion 276 11.5.1 The Equations .276 11.5.2 An Example 277 Exercises and Problems 281 References 281 Chapter 12 In-Service Behavior of a Shear Joint 283 12.1 Bolted Joints Loaded in Axial Shear .283 12.1.1 In General .283 12.1.2 Friction-Type Joints 284 12.1.2.1 Bolt Load in Friction-Type Joints 284 12.1.2.2 Stresses in Friction-Type Joints 285 12.1.3 Bearing-Type Joints 285 12.1.3.1 Stresses in Bearing-Type Joints . 286 12.2 Factors That Affect Clamping Force in Shear Joints 286 12.3 Response of Shear Joints to External Loads .288 12.4 Joints Loaded in Both Shear and Tension .288 12.5 Present Definitions—Types of Shear Joint 290 Exercises .290 References 291 xxiChapter 13 Introduction to Joint Failure .293 13.1 Mechanical Failure of Bolts .293 13.2 Missing Bolts 294 13.3 Loose Bolts .294 13.4 Bolts Too Tight 295 13.5 Which Failure Modes Must We Worry About? .295 13.6 Concept of Essential Conditions 295 13.7 Importance of Correct Preload 297 13.7.1 Corrosion 297 13.7.2 Stress Corrosion Cracking .297 13.7.3 Fatigue Failure 297 13.7.4 Mechanical Failure 297 13.7.5 Self-Loosening of Fastener 297 13.7.6 Leakage .297 13.8 Load Intensifiers 298 13.9 Failure of Joint Members .298 13.10 Galling 300 13.10.1 Discussion .300 13.10.2 Removing Galled Studs .300 Exercises .301 References 302 Chapter 14 Self-Loosening 303 14.1 The Problem .303 14.2 How Does a Nut Self-Loosen? .303 14.3 Loosening Sequence .306 14.4 Junker’s Theory of Self-Loosening .306 14.4.1 The Equations .307 14.4.2 The Long-Form Equation in Practice .308 14.4.3 The Equation When Applied Torque Is Absent .308 14.4.4 Why Slip Occurs? 309 14.4.5 Other Reasons for Slip 310 14.4.6 Other Theories of Self-Loosening 310 14.5 Testing for Vibration Resistance 310 14.5.1 NAS Test .310 14.5.2 Junker Test 311 14.6 To Resist Vibration 312 14.6.1 Maintaining Preload and Friction .313 14.6.1.1 Conventional Wisdom . 313 14.6.2 Preventing Relative Slip between Surfaces 314 14.6.3 Countering Back-Off Torque 315 14.6.3.1 Prevailing Torque Fasteners . 315 14.6.3.2 Nord-Lock Nuts and Washers 318 14.6.3.3 In General . 318 14.6.4 Double Nuts 319 14.6.5 Mechanically Locked Fasteners 319 14.6.5.1 Lock Wires and Pins . 319 14.6.5.2 Welding . 319 xxii14.6.5.3 Stage 8 Fastening System . 319 14.6.5.4 Huck Lockbolt 320 14.6.5.5 Honeybee Robotics . 320 14.6.5.6 A-Lock Bolt and Nut . 321 14.6.5.7 Omni-Lok Fasteners . 322 14.6.6 Chemically Bonded Fasteners .322 14.6.6.1 Rust 322 14.6.6.2 Anaerobic Adhesives 322 14.6.7 Vibration-Resistant Washers 323 14.6.7.1 Washers That Maintain Tension in the Fastener . 323 14.6.7.2 Toothed Washer . 323 14.6.7.3 Helical Spring Washer 324 14.6.7.4 Nord-Lock Washer . 324 14.6.8 Comparison of Options 324 Exercises .324 References and Bibliography 325 Chapter 15 Fatigue Failure .327 15.1 Fatigue Process 327 15.1.1 Sequence of a Fatigue Failure .327 15.1.1.1 Crack Initiation 327 15.1.1.2 Crack Growth . 328 15.1.1.3 Crack Propagation 328 15.1.1.4 Final Rupture . 328 15.1.2 Types of Fatigue Failure .328 15.1.3 Appearance of the Break 329 15.2 What Determines Fatigue Life? .329 15.2.1 S–N Diagrams .330 15.2.2 Material versus ‘‘The Part’’ .332 15.2.3 Summary .332 15.3 Other Types of Diagram 333 15.3.1 Constant Life Diagram .333 15.3.2 Center Portion of Constant Life Diagram 334 15.3.3 Approximate Constant Life Diagram .334 15.3.4 Endurance Limit Diagram 336 15.3.5 Fatigue Life Data for Fasteners 337 15.4 Influence of Preload and Joint Stiffness .338 15.4.1 Fatigue in a Linear Joint .338 15.4.2 Nonlinear Joints 339 15.4.3 What Is the Optimum Preload? 341 15.4.4 Fatigue and the VDI Joint Design Equations .341 15.5 Minimizing Fatigue Problems 343 15.5.1 Minimizing Stress Levels .344 15.5.1.1 Increased Thread Root Radius . 344 15.5.1.2 Rolled Threads . 344 15.5.1.3 Fillets 345 15.5.1.4 Perpendicularity 345 15.5.1.5 Overlapping Stress Concentrations . 345 15.5.1.6 Thread Run-Out . 345 xxiii15.5.1.7 Thread Stress Distribution 345 15.5.1.8 Bending . 347 15.5.1.9 Corrosion 347 15.5.1.10 Flanged Head and Nut . 347 15.5.1.11 Surface Condition . 348 15.5.2 Reducing Load Excursions .348 15.5.2.1 Prevent Prying . 348 15.5.2.2 Proper Selection of Preload 348 15.5.2.3 Control of Bolt-to-Joint Stiffness Ratios 348 15.5.2.4 Achieving the Correct Preload 348 15.6 Predicting Fatigue Life or Endurance Limit 348 15.7 Fatigue of Shear Joint Members 349 15.8 Case Histories 351 15.8.1 Transmission Towers 351 15.8.2 Gas Compressor Distance Piece 351 Exercises .352 References and Bibliography 352 Chapter 16 Corrosion .355 16.1 Corrosion Mechanism 355 16.1.1 Galvanic Series 355 16.1.2 Corrosion Cell .356 16.1.3 Types of Cells 357 16.1.3.1 Two-Metal Corrosion . 357 16.1.3.2 Broken Oxide Film . 358 16.1.3.3 Stress Corrosion Cracking 358 16.1.3.4 Crevice Corrosion . 359 16.1.3.5 Fretting Corrosion 359 16.2 Hydrogen Embrittlement .360 16.2.1 Stress Cracking Failure Modes .360 16.2.2 Hydrogen Embrittlement Mechanism of Failure 360 16.2.3 Susceptible and Safe Materials 361 16.2.4 Testing for Embrittlement .362 16.2.5 Fighting Hydrogen Embrittlement 363 16.3 Stress Corrosion Cracking .363 16.3.1 Mechanism of Failure .363 16.3.2 The Concept of KISCC .364 16.3.3 Factors Affecting KISCC 365 16.3.3.1 Bolt Material . 365 16.3.3.2 The Environment 365 16.3.3.3 Thread-Forming Procedure 365 16.3.3.4 Bolt Strength or Hardness 365 16.3.3.5 Type of Electrolyte 367 16.3.3.6 Temperature 367 16.3.3.7 Bolt Diameter and Thread Pitch . 367 16.3.4 Combating SCC 368 16.3.4.1 Susceptibility of the Material 368 16.3.4.2 Eliminating the Electrolyte . 369 16.3.4.3 Keeping Stress Levels below a Threshold Limit . 370 xxiv16.3.5 Surface Coatings or Treatment .374 16.3.6 Detecting Early SCC Cracks .376 16.4 Other Types of Stress Cracking .376 16.4.1 Stress Embrittlement .376 16.4.2 Hydrogen-Assisted Cracking 376 16.5 Minimizing Corrosion Problems 377 16.5.1 In General .377 16.5.2 Detailed Techniques 377 16.6 Fastener Coatings 379 16.6.1 In General .379 16.6.2 Organic Coatings 380 16.6.2.1 Paints 380 16.6.2.2 Phos-Oil Coatings . 381 16.6.2.3 Solid-Film Organic Coatings 381 16.6.3 Inorganic or Metallic Coatings .381 16.6.3.1 Electroplated Coatings 382 16.6.3.2 Hot-Dip Coatings . 382 16.6.3.3 Mechanical Plating . 382 16.6.3.4 Miscellaneous Coating Processes 383 16.6.4 Composite Coatings 383 16.6.5 Rating Corrosion Resistance 387 16.6.6 Substitutes for Cadmium Plate .387 Exercises .388 References and Bibliography 388 Chapter 17 Selecting Preload for an Existing Joint 391 17.1 How Much Clamping Force Do We Want? 391 17.1.1 Factors to Consider 391 17.1.1.1 Joint Slip . 392 17.1.1.2 Self-Loosening 392 17.1.1.3 Pressure Loads 392 17.1.1.4 Joint Separation 393 17.1.1.5 Fatigue 393 17.1.2 Placing an Upper Limit on the Clamping Force .393 17.1.2.1 Yield Strength of the Bolt . 394 17.1.2.2 Thread-Stripping Strength 394 17.1.2.3 Design-Allowable Bolt Stress and Assembly Stress Limits . 394 17.1.2.4 Torsional Stress Factor . 394 17.1.2.5 Shear Stress Allowance . 395 17.1.2.6 Stress Cracking . 395 17.1.2.7 Combined Loads . 395 17.1.2.8 Damage to Joint Members . 395 17.1.2.9 Distortion of Joint Members 395 17.1.2.10 Gasket Crush 396 17.1.3 Summarizing Clamping Force Limits .396 17.2 Simple Ways to Select Assembly Preloads .397 17.2.1 Best Guide: Past Experience .397 17.2.2 Second Best: Ask the Designer .398 17.2.3 Unimportant Joint: No Prior Experience .398 xxv17.2.4 When More Care Is Indicated 398 17.2.5 If Improvements Are Required .400 17.2.6 Selecting Preload for Critical Joints 400 17.3 Estimating the In-Service Clamping Force 400 17.3.1 Basic Assumptions 402 17.3.2 Combining the Scatter Effects 402 17.4 Relating Desired to Anticipated Bolt Tensions 408 17.5 Which Variables to Include in the Analysis .410 17.5.1 In General .410 17.5.2 Possible Factors to Include .411 17.5.3 Which Should We Include? .411 17.6 ASTM F16.96 Subcommittee on Bolting Technology .412 17.7 A More Rigorous Procedure 412 17.7.1 Experiments Required for True Accuracy 413 17.7.2 The Equations .413 17.7.3 Minimum Clamping Force—Some Examples .414 17.7.3.1 First Example—Using Worst-Case Values . 414 17.7.3.2 Second Example—Using Statistically Combined Values 415 17.7.3.3 Third Example—Using Average Values . 416 17.7.3.4 Fourth Example—Using Feedback Control Values . 417 17.7.4 Maximum Bolt Tension 417 17.8 NASA’s Space Shuttle Preload Selection Procedure 418 17.8.1 Calculating Maximum and Minimum Preloads 418 17.8.2 Confirming the Preload Calculations 420 17.8.3 Discussion .420 Exercises .421 References and Bibliography 421 Chapter 18 Design of Joints Loaded in Tension .423 18.1 A Major Goal: Reliable Joints .423 18.1.1 Checklist for Reliable Bolted Joints 423 18.2 Typical Design Steps 424 18.2.1 Initial Definitions and Specifications 425 18.2.2 Preliminary Design 425 18.2.3 Load Estimates .425 18.2.4 Review Preliminary Layouts: Define the Bolts .426 18.2.5 Clamping Force Required .426 18.2.5.1 Minimum Clamp 426 18.2.5.2 Maximum Clamp 427 18.3 Joint Design in the Real World .427 18.4 VDI Joint Design Procedure 427 18.4.1 Terms and Units .428 18.4.2 Design Goals .429 18.4.3 General Procedure 429 18.4.4 Estimating Assembly Preloads: Preliminary Estimate of Minimum and Maximum Assembly Preloads 430 18.4.5 Adding the Effects of the External Load 431 18.4.6 Is the Required Force Good Enough? 432 18.4.7 Further Considerations .433 xxvi18.4.7.1 Static Strength of the Bolt 433 18.4.7.2 Fatigue 433 18.4.7.3 Bearing Stress 434 18.4.7.4 Shear Stress . 434 18.4.7.5 Bending Stress . 434 18.4.7.6 Eccentric Loading . 434 18.4.8 Revised Bolt Specifications .435 18.5 An Example .435 18.5.1 Inputs 435 18.5.2 Calculations .436 18.5.2.1 Maximum and Minimum Assembly Preloads . 436 18.5.2.2 Static Strength of the Bolts . 436 18.5.2.3 Fatigue Strength . 437 18.5.2.4 Contact Stress . 437 18.6 Other Factors to Consider When Designing a Joint 437 18.6.1 Thread Strength 437 18.6.2 Flexible Bolts 438 18.6.3 Accessibility .438 18.6.4 Shear versus Tensile Loads .438 18.6.5 Load Magnifiers 438 18.6.6 Minimizing Embedment 438 18.6.7 Differential Expansion 438 18.6.8 Other Stresses in Joint Members .438 18.6.9 Locking Devices 439 18.6.10 Hole Interference .439 18.6.11 Safety Factors .439 18.6.12 Selecting a Torque to be Used at Assembly 439 Exercises .440 References 440 Bibliography .440 Chapter 19 Design of Joints Loaded in Shear 443 19.1 An Overview 443 19.2 The VDI Procedure Applied to Shear Joints .444 19.3 How Shear Joints Resist Shear Loads .446 19.3.1 In General .446 19.3.2 Concept of Slip-Critical Joints 446 19.4 Strength of Friction-Type Joints 448 19.4.1 In General .448 19.4.2 Allowable Stress Procedure .449 19.4.3 Other Factors to Consider 449 19.4.4 Slip Coefficients in Structural Steel .450 19.4.5 An Example 451 19.4.5.1 Minimum Preload Required to Prevent Slip . 453 19.4.5.2 Alternate Using the Allowable Stress Procedure 454 19.5 Strength of Bearing-Type Joints 455 19.5.1 Shear Strength of Bolts .455 19.5.1.1 Distribution of Load among the Bolts 455 19.5.1.2 Shear Strength Calculations 456 xxvii19.5.2 Tensile Strength of Joint Plates .457 19.5.3 Bearing Stress 457 19.5.4 Tearout Strength .458 19.5.5 Summary .459 19.5.6 Clamping Force Required by a Bearing-Type Joint .459 19.6 Eccentrically Loaded Shear Joints .459 19.6.1 Rotation about an Instant Center .459 19.6.2 Rotation about the Centroid of the Bolt Group .461 19.6.2.1 Find the Centroid of the Bolt Group . 461 19.6.2.2 Estimating the Shear Stress on the Most Remote Bolt . 462 19.7 Allowable Stress versus Load and Resistance Factor Design 465 Exercises .466 References 466 Appendix A Units and Symbol Log .467 Appendix B Glossary of Fastener and Bolted Joint Terms 475 Appendix C Sources of Bolting Information and Standards 483 Appendix D English and Metric Conversion Factors .485 Appendix E Tensile Stress Areas for English and Metric Threads with Estimated ‘‘Typical’’ Preloads and Torques for As-Received Steel Fasteners .487 Appendix F Basic Head, Thread, and Nut Lengths .497 Index .505 Index A A325 bolt, elastic curve for, 183 Acme thread, 61–62 Airframe, 115 Air-tool control system, 188 AISC allowable stress limit, 464 AISC bolt specifications, 449 AISI H-11 bolts, 364 Allowable stress, 465 A-lock bolt and nut, 321 American Bureau of Shipping, 14 American Institute of Steel Construction (AISC) Load, 290 American National Standards Institute (ANSI), 14 American Society for Testing and Materials (ASTM), 14–17 American Society of Mechanical Engineers (ASME), 14 Anaerobic adhesives, 322–323 ANSI washer, standard thickness, 56 Anticipated loads and strength, 465 ASME Boiler and Pressure Vessel Code, 50 Assembly stress limits, 394 torque selection for, 439–440 Assembly preloads calculations for, 436 estimation of, 430–431 selection of, 398–400 Assembly process, 4, 6, 22, 114 first bolt tightening, 110–114 optimizing assembly outcomes, 134–135 parts assembling, 110 tool work and clamping force, factors affecting relationship, 133 Association of American Railroads, 14 ASTM A193 B7 bolts, 110 ASTM A325 bolts, 206 ASTM A490 bolts and strength loss, 42 ASTM A193 materials and temperature limits, 18 ASTM B-117 and corrosion resistance rating, 387 ASTM B7 fasteners, 200 ASTM F2281 and F2282 materials, room temperature strengths, 18–20 ASTM F16.96 subcommittee, on bolting technology, 412 Automotive-tightening procedures, 191 Average assembly preload, 223 Axial bolt load, 250, 252 Axial shear bolted joints loaded in, 283–284 joints, static failure modes of, 56–57, 299 load, 450, 452 Axial tension load for bolt, 255 Axis of gyration of joint, 256–257 B Bearing stress, 434, 457–458 Bearing-type joints, 285 clamping force for, 459 static failure of, 56 strength determining factors for, 455 stresses in, 286 Belleville washer, 123, 275, 316 Bending stresses, 262, 434 Bent bolt, ‘‘radius of curvature’’, 58 Bent joint members, 124 Bolted joints behavior and life of, 2 clamping force and, 4, 426–427 design of, 7 failure on Skylab program, 155 load estimation, 425–426 preliminary design, 425 problems in, 3 types of, 1–2 (see also Shear joints; Tensile joints) typical design steps for, 424 Bolt head and nut, contact surfaces, 54–55 Bolt-hole interference, 193 Bolting information and standards, 483–484 Bolting materials hardness and strength of, 23 properties of, 16 505resistance to corrosion, 12 shear strength of, 21 temperature effect on, 12–13, 26 tensile strength of, 16 Bolting spec by RCSC, 290 Bolting standards, see Fastener standards Bolting technology, ASTM F16.96 subcommittee on, 412 Bolting Technology Council (BTC), 143, 412 Bolt loads and interface clamping force, thermal effects on compensation for, 274–276 creep and stress relaxation, 271–273 differential thermal expansion and contraction, 267–271 modulus of elasticity and tensile strength, 266–267 Bolt-nut system, 24–25 Bolt-nut-washer system, stiffness of, 92 Bolt preload and clamping force, 114–118 limits, 444 in shear joint, 286 Bolt(s) clamping capacity of, 12 cross-sectional areas of, 89, 453 deformation of, 85, 93 design allowable stresses for, 394 diameter, thread pitch and, 367–368 diameter of, 72 dimensions, 497 distribution of load, 455–456 effective length of, 87–89 elastic curves for, 87 elastic interactions between, 127–132 elongation of, 91, 173 energy storage capacity of, 8, 93 flexible, 438 and hole, 114–116 hydrogen embrittlement cracking of, 7 length, 123 load types on, 57 mechanical failure of, 293 shear strength of, 455 short and stubby, 89 short-term relaxation of amount to expect, 124–125 factors affecting in, 122–124 sources of, 119–120 torsional relaxation, 125–127 static strength of, 53, 433, 436–437 stiffness of (see Bolt stiffness) strength, KISCC value and, 365–367 tension in (see Bolt tension) tightening, 48, 111, 140 yield strength of, 394 Bolts and joint members differential expansion between, 5 elastic deformation of, 3 shear strength of, 3 stiffness of, 27 Bolt stiffness, 87, 175 calculations of, 90–91 design goals of, 104–106 expression for, 92–93 Bolt stretch component, of reaction torque, 141 Bolt tension, 2, 256 anticipated, 408–410 elastic curves for, 41–42 at initial preload, 137 maximum, 417–418 at residual preload, 137 in service, 137 tension and compression stress in, 43 Bolt tensioners, see Tensioners Bolt thread root stresses, 76 Bolt-to-bolt preloads, 143 Bolt-to-joint stiffness ratios, 287 Bolt yield, 256 Brittle fracture, 13, 40 Broken bolt, examination, 329 BS 4882 and equivalent materials, service temperature limits, 29 Butt joint, see Shear joint Buttress thread, 61–62 C Centroid, of bolt group, 461–464 Clamping force, 4, 114, 219–221, 226, 234, 240, 261–262, 274, 444, 459 bolted joints design and, 426–427 considering factors, 391–393 instability of, 28 limits, 396–397 loss of, 13, 30 magnitude of, 11 properties affecting, 11 requirements for joint, 393–396 in shear joints, 3, 286–288 stability of, 12 Clutch, types of, 162 C-Micrometer, see Micrometers Coarse-and fine-inch series and metric fastener series, 68 Coarse-pitch threads, 63, 70 Combined loads, 395 Compressive force and deflection, of blocks, 94–95 506 Introduction to the Design and Behavior of Bolted JointsConcentric joints, stiffness of, 96–97 Conical makeups, preloaded fastener relaxation in, 121–122 Constant-pitch threads applications, 70 Contact stress, 437 Conventional nut, relative stress level in, 47 Corrosion, 12, 32, 297 cadmium plate, substitutes for, 387–388 composite coatings, 383–387 hydrogen-assisted cracking, 376 hydrogen embrittlement, 360–363 inorganic coatings, 381–383 mechanism (see Corrosion mechanism) organic coatings, 380–381 reduction of, 377–379 resistance rating, 387 SCC combating, 368–374 early cracks, detection of, 376 failure mechanism, 363–364 KISCC concept, 364–368 surface coatings, 374–376 stress embrittlement, 376 Corrosion mechanism corrosion cell, 356–360 galvanic series, 355–356 Corrosion protection, 451 Corrosion-resistant materials, 19, 378 Crack growth monitoring, computer-controlled equipment for, 362 Cracking susceptibility and temperature, 367 Crack initiation, 327 Crack propagation, 328 Creep, 27, 120, 123, 271, 445 relaxation, 433 rupture, 273 Crevice corrosion, 359 Critical external load, 229 Critical hardness, 23 Critical joints, preload selection for, 400 Cryogenic bolting materials, room temperature strengths for, 31 Cryogenic temperatures, 18, 31 Cut and rolled threads, 143 D Deformations, in joint and bolt, 174–175 Depth micrometers, 200 Differential expansion, 258, 265, 268, 269, 271, 275, 433, 438 Direct tension indicators (DTI), see Washers, tension indicating Double nut, 316, 319 Drunken thread, 81 Ductile bolts, 185 Ductile fastener, 41 E Eccentric joints, stiffness equations of, 97–100 Eccentric load, 434–435, 460, 463 Eccentric nut, 316 Elastic curves, for bolts, 221 Elastic interactions, 152, 445 Elasticity modulus, 13, 27, 87–88 Elastic limit, 41 Elastic stiffness, 13 Electroplated coatings, 382 Elongated expansion bolt, 275 Elongation chart, for bolts, 203 Embedment, relaxation, 4, 119–120, 122, 152, 189 Endurance limit, 12, 32, 330–332, 335, 342–344, 348–349 Engine head bolts, preloads in, 149 Equi-torq motor, 188 Exotic aerospace bolting materials, service temperature limits of, 29 Expansion, coefficients of, 445 F Fastener, 208 chemically bonded, 322–323 diameter of, 16, 71 initial preload scatter for, 152 international metric standard for, 20 and joint, contact stress between, 54 length change for, 90 limiting torque of, 164 shape of, 16 standards, 14–15 static failure of, 138 tensile force of, 48 Fastener coatings, 379 cadmium plate, substitutes for, 387–388 composite, 383–387 corrosion resistance, rating, 387 inorganic, 381–383 organic, 380–381 Fastener control, production method of, 191 Fastener joint system, energy delivered to, 112 Fastener materials; see also Bolting materials relative weights of, 33 selection of, 32 shear strength of, 71 Fatigue, 6, 393, 433–434 break surface of bolt, failed in, 329 Index 507case histories of, 351–352 cracks, 329, 344, 352 cracks and failures, 329 eliminating problems, 343–348 factors affect life, 332–333 failure, 138, 327–328 life, 32, 329–337 in linear joint, 338–339 loading conditions, variety of, 335 and mechanical failure of joint, 297, 327 process of, 327–328 resistance, 332 resistant fasteners, 344 rupture, 12 of shear joint members, 349–351 strength, 32, 40, 332, 350, 433–434 types of, 328–329 and VDI joint design equations, 341–343 Federal Standard FED-STD-H 28=2B, 61 Fillets, 121 Fine-pitch threads, 63 applications of, 70 lengths for, 67 Finite-element analysis, 413 Flanged nut, 316 Flange rotation, 250 Force ratio, see Load factor Fracture mechanics, 350 Frangible nut, 165 Free-spinning lock nuts and bolts, 317 Fretting corrosion, 359–360 Friction coefficient, 451 effects, 177 joints, 56 restraint, 141, 175 variables affecting, 142–143 Friction-type joints, 447, 449 bolt holes, 284–285 stresses in, 285 G Galling, 300–301 Galvanic series, 355–356 Galvanized coating, 450–451 Gasket creep, 274 Gasket crush, 396 Gasketed joints, 6, 56, 174–175 relaxation of, 178 stiffness of, 101–103 turn–preload curve for, 177 Gaskets, 274 creep and relaxation of, 177 force-deflection behavior of, 103 Geared wrenches, 156, 160 Graphite-based lubricants, friction coefficient for, 149 H Heaters, bolt, 210 Helical spring washer, 324 Hex bolts, 498 finished, 499 heavy, 499, 500 metric, 501–502 Hex cap screws, 499–500 metric, 502–503 High-temperature materials, 18 Hole–bolt interface problems, 115 Hole interference, 114, 439 Honeybee robotics, 320 Hooke’s law, 85, 93, 197, 269 Hot-dip coatings, 382 Hot torque, 275 Huck lockbolt, 320 Hydraulic tensioners, 117–119; see also Tensioners Hydraulic wrenches, torque accuracy of, 159–160 Hydrogen-assisted cracking, 376 Hydrogen embrittlement combating, 363 failure mechanism, 360–361 materials, safe and susceptible, 361–362 stress cracking failure modes, 360 testing for, 362 Hysteresis effects, 265 I IFI, see Industrial Fastener Institute Impact wrenches, torque accuracy for, 161 Inch series and metric thread classes, 66–67 Inch series external (bolt) thread code, 69 Inch series thread forms, 61 Inch series threads allowance of, 64 class of, 64 coatings of, 67 tolerance of, 64 Inconel bolts, 53, 116 Industrial Fastener Institute, 14, 316, 362 Infinite life, 336, 342 Inorganic coatings, see Metallic coating Inorganic zinc-rich paint, 451 In-service clamping force, estimation basic assumptions of, 402 508 Introduction to the Design and Behavior of Bolted Jointsscatter effects and, 402–408 variables in, 401 In-service tension in bolts, 109 Interference fit holes, 115 International Standards Organization (ISO), 14 J Joint behavior, 249 design, 452 designer goals and problems of, 4, 7 eccentrically loaded, 257 hardness, on torque tool selection, 157 plates, 457 separation, 138, 393 slip, 138, 392 yields, 153 Joint behavior, under loads compressive load and, 245 critical external load and, 229–230 equations, for studying, 232–235 fluctuating external load and, 243–244 joint diagrams, 220–225 loading planes and, 235–242 residual assembly preload determination, 220–224 Rolls Royce example, 226–227 simple tensile loads and, 244–266 stiffness, effect of, 228 Joint diagram, and joint behavior axial compression, load under, 246 fluctuating loads and, 244–245 joint surface, external load at, 237 for preloaded joints, 220–221 for simple tensile loads, 224–227 stiffness change and, 228 Joint failure, 293 essential conditions for, 295–297 failure mode and preload, relationship, 297 failure modes, types of, 295 fatigue and mechanical, 297 Joint loaded in tension analysis of behavior on prying action, 250–255 impact of change in temperature, 266–276 joint equations for eccentricity and differential expansion, 276–280 mathematics of prying in, 256–263 nonlinear behavior of, 263–266 Joint materials bearing yield strength of, 23 failures of, 35 room temperature strength of, 32–35 Joint members, 123 bolt preload and clamping force on, 114 classification of, 157 damage and distortion, 395 deflection of, 95, 105 disassembly of, torque to, 168–169 energy stored in, 104 equal compressive stress in, 54 failure of, 298 interface contact pressure, 258 relative interface pressure between, 55 resistance from, 116–118 snugging of, 175 as springs, 94 static failure of, 56 strength of, 54 stresses in, 438–439 stresses of, 56 Joints loaded in tension, design calculations, 436–437 considering factors, 437–440 in real world, 427 reliable bolted joints, checklist for, 423–424 steps for, 424–427 VDI joint design procedure, 427–435 Joint stiffness, 276, 250, 253, 265 computation of, 95, 103 and deformation, 96 estimation of, 100 influence of preload and, 338–343 ratio, 104 Joint-to-bolt deflection ratio, 223 Joint-to-bolt stiffness ratio, 100, 102 Junker vibration test machine, 311–312 K K ISCC concept, 364–365; see also Stress corrosion cracking bolt material and hardness, 365–367 electrolyte, type of, 367 environment, 365 temperature, 367 thread-forming procedure, 365 thread pitch, bolt diameter and, 367–368 L Lap joint, see Shear joint Lead screw, 174 Leakage, 297; see also Gaskets Levers to pry bolt, 250–251 Linear elastic fracture mechanics (LEFM) equation, 364–365; see also KISCC concept Load cycles, 328, 337, 341 Index 509excursion, 338–342, 348 factor, 104, 233 intensifiers, 298 magnifiers, 438 Load and Resistance Factor Design (LRFD) specification, 290, 465 Loading plane factor, 240, 242 Loading planes, and joint behavior definition of, 236 effects of, 243 joint members and, 239–243 significance of, 238–239 Locking fasteners, 312, 318, 320 Lock wires and pins, 319 Loose bolts, 294 Low-alloy, quenched, and tempered steels (LAQT steels), 21 thermal expansion for, 27 ultimate strength and hardness for, 24 yield strength and hardness for, 22, 24 Low-alloy quenched and tempered (LAQT) steels, 365–367, 370 Low-weight fasteners, 13 LRFD specification, 448 Lubricants preloads and stresses for, 488 torque for, 487–488 Lubricants and antiseize compounds, break out torques for, 147–148 Lubricated and unlubricated bolts, torque in, 154 M Manual torque wrenches; see also Torque wrenches torque accuracy of, 159–160 Manual turn-of-nut techniques, 192 Maximum bolt load, 276, 280 Mechanically locked fasteners, 319–320, 319–322 Metallic coating, 381; see also Fastener coatings electroplated coatings, 382 hot-dip coatings, 382 mechanical plating, 382–383 miscellaneous coating processes, 383 Metallized aluminum and zinc, 451 Metric fasteners, 15, 20 Metric series threads, coatings of, 67 Metric standards, 20 Metric thread forms, U.S. standards for, 63 Metric threads code for, 69 stress areas of, 51 tolerance class, grade and position for, 66 types of, 65 Micrometers, 199–201 Microprocessor control, for torque–angle tools, 185 MIL-STD-1315-5A, hydrogen embrittlement testing and, 362 Minimum clamping force, using average values, 416–417 feedback control values, 417 statistically combined values, 415–416 worst-case values, 414–415 Minimum per-bolt clamping force, 276 Missing bolts, 294 Molydisulfide lubricants, coefficients of friction for, 149 Motosh equation, 309 MP35N, SCC and, 369 MP35N bolt nut factor in, 149 re-tightening of, 149 M12 steel bolts, torque in, 153 Multispindle air-tool control system, 190 N NASA’s space shuttle preload selection procedure, 418–420 NAS vibration test, 311 National Institute of Standards and Technology (NIST), 14 Non-gasketed joints, 100, 102 Nonlinear joints, 339–341 Nonstandard fasteners, design limits for, 49 Nord-Lock nuts and washers, 316, 318 Nut, 501 stress in, 45–48 tension in (see Tension nuts) torque-turn curve of, 103 turning of, 173 vibration loosening of, 138 Nut and bolt flank angles of, 76 relative motion of, 173 Nut and bolt threads, pitch of, stress distribution in, 45, 47 Nut-bolt systems, nonlinear factors, 263 combined stiffness and hysteresis effects, 265 distance, washers (DLW) of system as function of applied load, 264–265 Superbolt torquenut as model for, 266 Nut dilation, 4, 26, 76–77 Nut factors, 150, 323 accuracy of, 148 case histories of, 148–151 for ceramic-based material, 147–148 and coefficient of friction, 151 lubricity effect on, 151 510 Introduction to the Design and Behavior of Bolted Jointsfor moly-based material, 147–148 for steel fasteners, 146–147 for unlubricated steel, 148 Nut friction torque, 141 Nut-joint friction, 142 Nut materials proof load of, 26 selection of, 24 strength of, 26 Nut runner, multispindle, 162 Nut runner multipliers, see Torque multipliers Nuts or bolt heads, nonperpendicular, 121 Nut strength and bolt strength, 79 Nut threads, diameter of, 71 Nut-to-bolt threads coefficient of friction between, 77 relative strength of, 77 rotary motion of, 77 thread bending factor for, 77 Nylon insert nut, 316 O Omni-lok fasteners, 322 Optimum preload, 341 Organic coatings; see also Fastener coatings paints, 380 phos-oil, 381 of solid-film lubricant, 381 Oversized holes, 121 Oxide film, broken, 358 P Petrochemical bolting materials and stress relaxation, 28 Phos-oil coatings, 381 Pipe stress, 118 Pitch diameter, of thread, 81 Plastic deformation, 2, 182 Polytetrafluoroethylene (PTFE), 381, 383 Power Dyne instrument, 215 Preload control of, 173 eccentric elastoplastic joint, 257 in engine head bolts, 149 friction and maintaining of, 313–314 initial and residual, 109 in joint, step-by-step buildup of, 176 preventing relative slip, 314–315 problems of, 138 in SAE Grade 8 bolt, 152, 184 torque control of, 140, 166 Preload, for existing joint assembly preloads selection, 397–400 bolting technology, ASTM F16.96 subcommittee on, 412 bolt tensions anticipated, 408–410 maximum, 417–418 clamping force considering factors, 391–393 limits, 396–397 minimum, 414–417 upper limit on, 393–396 equations, 413–414 experiments for, 413 in-service clamping force estimation, 400–408 NASA’s space shuttle preload selection procedure, 418–420 variables for, 410–412 Preload, in bolts direct control of, 204–208 optimizing, 211–213 problems solved by, 210–211 stretch control of, 197–199 Preload-indicating washer (PLI), 206 Pressure loads, 392–393 Pressure vessel joint, 110 Pressure Vessel Research Committee (PVRC), 147 Pretensioned joints, 290 Prevailing torque, 144; see also Torque control of, 191 Proof loads, 48 Proof strength, 16, 48 Proportional limit, 41 Prying action on bolt loads, 250 external load and reaction force for, 252 forces, 252–254 load, 253 mathematics of bending stress in bolt before liftoff, 261–263 critical loads and preloads, 260–261 equations for load factor F, 259–260 and external loads, effects of, 263 VDI’S analytical procedure, 256–260 nonlinear nature, 255–256 Puget Sound Naval Shipyard, 117 Pulse tools, 161 R Reaction torques, 157–159 Relaxation processes, 5 Reliable bolted joints, checklist for, 423–424 Remote bolt and calculation shear stress, 462–464 Research Council on Structural Connections (RCSC), 207, 290, 443, 451, 465 Index 511Residual assembly preload, 223 Residual preload, 139 bolt tension at, 137 in structural steel bolts, 30 Residual stress, 28 Resilience, 104, 258–260, 271, 277, 278 Room temperature strengths, 21 Rust, 322 S SAE Grade 8 bolt preload in, 152, 184 stiffness and change in length of, 90 SAE’s J429, 15, 17 Scatter effects, combining, 402–408 SCC, see Stress corrosion cracking Screwdrivers, 161 Self-loosening, 459 Junker’s theory of, 306–309 loosening sequence, 306 occurrence of, 303–306 relative resistance to, 316 testing for vibration resistance, 310 Self-loosening, 292 Shear joints, 1, 283, 443 bolt’s job in, 3 clamping force in, 3 eccentrically loaded, 459–465 failing of., 287 in-service behavior of, 5–6 response to external loads, 288 slip-critical joints, load resistance for, 446–448 VDI procedure for, 444–446 Shear-loaded joints, fatigue failure of, 115 Shear loads, in structural steel joints, 57 Shear strength, calculation, 3, 21–22, 35, 40, 58, 71, 455–457 Shear stress, 287, 434, 462 allowance, 395 and tensile loads, 438 Sheet metal joint, turn–preload curves of, 176–177 Simple tensile loads, joint diagram for, 224, 227 Skidmore–Wilhelm device, 163, 207 Slip, 6 coefficient, 450–452 and preload, 453–454 resistance, 448–449, 450 Slip, thread and nut or joint helix angle of threads, reducing of, 315 preventing or minimizing of, 314 sequence of events, 309–310 Slip-critical joints, 290, 446–440 S–N diagrams, 330–332 Snugging pass, 119 Snugging torque, 110, 119, 181 Snug-tightened joints, 290 Society of Automotive Engineers (SAE), 14 Spring constant, 86, 173–174, 232 Spring washer, 316 Square bolts, 498 Stage 8 fastening system, 319 Steel fasteners, nut factor K value for, 146–147 Stiff joint, torque–preload behavior of, 176 Stiffness bolt, 225, 232, 264–265, 270 bolt–nut–washer system, 92 concentric joints, 96 eccentric joints, 97–100 joint (see Joint stiffness) of non-gasketed steel joints, 100 and stored energy, 105–106 and stretch, 92 Stiffness ratio, 8, 106 bolt and joint, 252–253, 270, 274–275 joint (see Load factor) Strain energy losses, 144 Strain-gauges, 205; see also Stretch, measurement of Strength of bolt, 78 at high and low temperatures, 40 of threads, 71 types of, 39–40 Stress amplitude, 343 concentrations, 43, 329 cracking, 6, 395 embrittlement, 376 gradient, 350 levels, factors increase of, 298 procedure, 449, 454 relaxation, 13, 27–28 Stress area equations, for fastener materials, 50 Stress corrosion cracking, 40, 138, 297, 355, 358–359 combating electrolyte elimination, 369–370 material susceptibility, 368–369 threshold limit, 370–374 failure mechanism, 363–364 KISCC concept (see KISCC concept) SCC cracks, early detection of, 376 surface coatings, 374–376 Stress design procedure, allowable, 465 Stress–strain performance, 332 Stretch, measurement of dial gages and, 201–202 ultrasonic measurement, 202 512 Introduction to the Design and Behavior of Bolted Jointsultrasonic technique, 213–215 using micrometers, 199–201 Stretch control advantages of, 198, 203–204 basic concept, 197 optimizing, 204 problems with, 198–199 Stripped thread, 71 Structural steel bolts residual preload in, 30 temperature effect on, 30 turn-of-nut procedure for, 182 Structural steel bolts and modified Goodman curve, 337 Structural strength, 465 Superbolt torquenut, 265 T Tapped holes, see Nut Target preload, see Average assembly preload Tearout strength, 458–459 Tensile capacity of bolt to shear stress, 289 Tensile joints bolt’s job in, 1 in-service behavior of, 5 Tensile loads, 42, 57, 250, 251, 253, 256, 258, 276–277, 280 Tensile loads, and joint behavior equations, for studying, 232–235 imple tensile loads and, 244–266 joint diagrams of, 220–225 loading planes and, 235–242 residual assembly preload determination, 220–224 Rolls Royce example, 226–227 stiffness, effect of, 228 Tensile strength, 16, 39, 59 in automotive group, 17 joints plates for, 457 in metric group, 17 in petrochemical=power group, 17 in structural steel group, 17 Tensile stress, 88, 289 along lines parallel to bolt axis, 43 magnitude of, 43–45 in rod of nonuniform diameter, 85–86 Tensile stress area for higher-strength steels, 52 of standard thread, 49 Tensile-tensile (nonreversing) load, 343 Tensioners, for bolts, 208–212 Tension-monitoring device, 192 Tension nuts relative stress level in, 47 stress distribution in, 45–46 Thermal expansion, 12, 27 Thin joints, stiffness ratio vs. slenderness ratio for, 102 Thread and bolt, stress areas of, 51 characteristics of, 70 class 2A, stress area of, 49, 67 engagement, 72, 120 friction torque, 141, 144 inspection levels for, 68–69 lubricants, 153 root, pitch, and nominal diameter of, 52 series, 63 static strength of, 76–79 strength of, 71 Thread bending, strength reduction factor for, 78 Threaded fasteners, 24, 61 torque to, 155 Thread forms, 61 applications of, 61 under load, 76 Threadless fastener, 45 Threads per inch, of UNC and UNF thread, 63 Thread strength, 437–438 computation procedures, 72–73 equations, 71 factors affecting, 81 loss of, 80–81 Thread stress and shear areas metric M series, 75 UNC=UNF=8UN, 74 Thread stress area, 74–75 Thread-stripping areas, 72, 79 strength, 39–40, 70, 80, 394 Threshold limit, SCC combating and, 370–374 Tightening speed, 123 Titanium alloys, 369 Titanium tension nuts, 45 Tolerance abnormal lengths of engagement, 67 inch series threads, 64 metric threads, 66 Tool work on bolt or nut and clamping force, 133 Toothed washer, 316, 323 Torque and angle, 179 back-off, 312, 315 for different lubricants, 487–488 equations applied, 307–308, 315 fasteners, 315, 322 feedback control on, 164 Index 513monitoring (see Torque calibration) multipliers, 159–160 nut, 312, 317 preloads and stresses for, 488 prevailing, 304, 312, 315 selection for assembly, 439–440 units (see Torque units) Torque and preload long form equation of, 140–142 short-form equation of, 146 Torque and turn, theory of, 179–181 Torque-angle control, see Torque-turn control Torque-angle tools, production assembly problems of, 184–186 Torque-angle window control, 186–187 Torque calibration, 162 disadvantage of, 163 for structural steel torque wrenches, 162 Torque–clamping force relationship., 114–117 Torque control, 151 advantages of, 166 on joint design, 167–168 low friction for, 153 tools for, 155 Torque-preload relationship, factors affecting, 154–155 friction, 142 geometric variables, 143 hole interference, 145 interference fit threads, 145 mechanic, 145 prevailing torque, 144 strain energy losses, 144 tool accuracy, 145 weight effect, 144 Torque-time curve, 187 Torque-time window control, 187 Torque tools, 156 for high speed production applications, 160 maintenance of, 156 power supplies for, 156 reaction forces, 157 testing of, 166 Torque transducer, 164, 184 Torque-turn air tools, 183 Torque-turn control, 179 advantages of, 193 optimization of, 193–194 techniques of, 176, 181 Torque-turn curve, 185 Torque-turn-preload cube, 179 friction change in, 180 Torque-turn system, 186 Torque-turn tool, 192 Torque units english tensile stress areas, 489–495 metric tensile stress areas, 496 Torque wrenches, shear loads of, 157–158 Torquing operations, hard-copy records of, 191 Torsional energy, 178 Torsional stress, 58, 182, 394–395 Turn control, 173, 178 Turn-of-nut control, 179, 181 in aerospace assembly, 183 for automotive joints, 191 nut rotation from snug tight condition for, 182 in production operations, 183 in structural steel applications, 181 for structural steel bolts, 182 theory of, 181–182 Turn-past-snug tightening procedure, 183 Twist-off bolt, 164–165 Twist-off fastener, in airframes, 165 Two-metal corrosion, 357–358 U Ultimate strength, 16, 41; see also Tensile strength of exotic bolting materials, at cryogenic temperatures, 31 and hardness for LAQT steels, 24 Ultimate tensile strength (UTS), 332–333, 336, 402, 409 Ultrasonic extensometers, 192 Ultrasonic measurement, of stretch, 214–215, 215 UN, UNR, and UNJ, threads form, 61 UN and UNJ threads, tensile stress and thread root areas for, 50–51 Undersized holes, 121 V VDI Directive 2230, 413, 435 VDI equations, use of, 435–437 VDI joint design procedure, 427 assembly preloads, estimation of, 430–431 bolt, static strength of, 433 design goals, 429 eccentric loading, 434–435 external load effects, 431–432 fatigue, 433–434 force required for, 432–433 revised bolt specifications, 435 stress, 434 terms and units, 428–429 VDI procedure, for shear joints, 446–448 Verein Deutscher Ingenieure (VDI), 97, 100, 256 Vibration loosening, see Self–loosening 514 Introduction to the Design and Behavior of Bolted JointsVibration resistance, testing for, 310 Junker test, 311–312 NAS test, 310–311 Vibration-resistant nuts, 316 Vibration-resistant washers, 323–324 Vinyl coatings, 451 W Washers strain gaged, 205 tension indicating, 205–208 Whitworth thread, 61–62 Working loads on bolts, factors affecting, 139 Wrenches, torque range for, 156 Y Yield control, 188–190 Yield strength, 16, 41 of bolt, 394 of inconel 600 bolt, 53 of joint material, 23 vs. hardness for LAQT steels, 22, 2
كلمة سر فك الضغط : books-world.net The Unzip Password : books-world.net أتمنى أن تستفيدوا من محتوى الموضوع وأن ينال إعجابكم رابط من موقع عالم الكتب لتنزيل كتاب Introduction to the Design and Behavior of Bolted Joints - Non-Gasketed Joints رابط مباشر لتنزيل كتاب Introduction to the Design and Behavior of Bolted Joints - Non-Gasketed Joints 
|
|